- お役立ち記事
- The secret to selecting materials that balances cost control and quality assurance that purchasing departments should keep in mind
The secret to selecting materials that balances cost control and quality assurance that purchasing departments should keep in mind
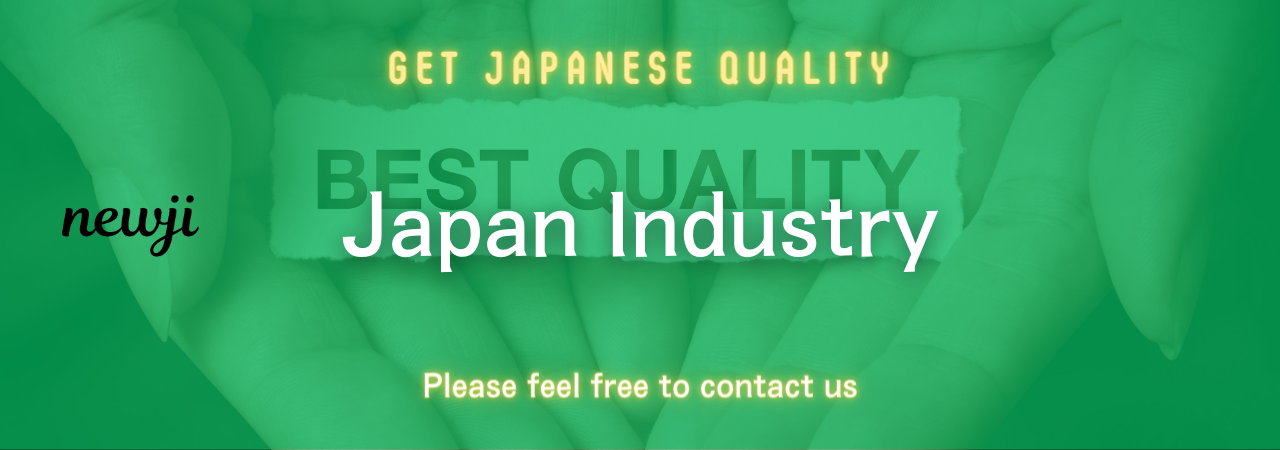
目次
Understanding the Importance of Material Selection
When it comes to purchasing departments, selecting the right materials can make or break a company’s ability to balance cost control with quality assurance.
The pressure is always on to minimize expenses while maintaining a high standard of quality.
This delicate balance is vital to both the competitiveness and reputation of the business.
By understanding the principles behind material selection and utilizing effective strategies, purchasing managers can ensure they are making informed decisions.
Why Material Selection Matters
The choice of materials affects numerous aspects of business operations, from production efficiency to customer satisfaction.
Choosing poor-quality materials can lead to product failures, increase returns, and damage the brand’s credibility.
On the other hand, high-quality materials may significantly increase production costs, potentially making the products too expensive for the target market.
Finding a middle ground between cost and quality is essential to maintaining profitability.
Key Considerations for Material Selection
To achieve a balance between cost and quality, there are several key factors that purchasing departments should consider.
1. Understand the Product Requirements
The first step in selecting materials is to fully understand the product’s functional and performance requirements.
Knowing what is expected of the product in terms of durability, strength, and aesthetics can guide the selection of materials that will meet these criteria cost-effectively.
By identifying the essential features that must be prioritized, you can narrow down your material choices to those that offer necessary properties.
2. Evaluate Total Cost of Ownership
When considering materials, it is crucial to look beyond the initial purchase price.
The total cost of ownership (TCO) includes not only the purchasing cost but also maintenance, transportation, and disposal costs.
A cheaper material might appear cost-effective upfront but could incur significant costs in maintenance or have a shorter lifespan, which increases expenses over time.
Thinking long term and calculating the TCO can provide a clearer picture of the material’s true cost-effectiveness.
3. Assess Supplier Reliability and Stability
The reliability of suppliers is another key factor in balancing cost and quality.
A dependable supplier consistently provides quality materials and delivers on time, minimizing disruptions in the supply chain.
Building strong relationships with reputable suppliers can also lead to better deals, bulk purchase discounts, or even custom material solutions tailored to specific needs.
Furthermore, understanding a supplier’s financial stability can prevent future delivery hurdles caused by their business issues.
Strategies for Cost Control
Controlling costs while assuring quality is a challenge but not an impossible task for purchasing departments.
Here are some strategies to keep expenses in check.
1. Leverage Volume Discounts
Purchasing in larger quantities can usually qualify for significant discounts.
Understanding historical demand pattern and forecasting accurately allows for bulk purchasing without overstocking.
Working closely with your supplier to manage inventory levels can optimize this strategy.
2. Consider Alternative Materials
Researching and testing alternative materials can lead to substantial savings.
New materials or process innovations can sometimes provide similar or superior properties at a reduced cost.
Benchmarking industry standards can also reveal new material trends that competitors are benefiting from.
3. Regular Supplier Audits
Consistently monitoring supplier performance ensures that they maintain the quality and cost standards agreed upon.
Regular audits can catch potential problems before they escalate, safeguarding the company’s interests.
Effective communication with suppliers about expectations and feedback is critical in establishing a mutually beneficial relationship.
Achieving Quality Assurance
While focusing on cost control, it is crucial not to neglect quality assurance.
Here’s how you can ensure materials meet standards without overspending.
1. Set Clear Quality Standards
Establish detailed quality standards that materials must meet.
These standards should be clear, measurable, and agreed upon with your suppliers from the beginning of the relationship.
Clear standards give both parties a framework to measure compliance and address any deviations swiftly.
2. Implement Comprehensive Testing Procedures
Conducting thorough testing of materials before incorporating them into production can identify potential issues early.
This step is vital in ensuring that materials conform to quality standards, avoiding costly defects and recalls further down the line.
Testing should not only measure compliance but also explore ways to improve processes and materials over time.
3. Foster a Culture of Continuous Improvement
Encourage your team and suppliers to continuously look for improvements in material selection and usage.
Creating an environment where feedback is valued can lead to innovations and efficiencies that reduce costs without sacrificing quality.
Systematically reviewing and refining purchasing strategies helps keep the department agile and responsive to market changes.
Conclusion: Striking a Balance
Material selection is an essential part of the purchasing process that directly impacts both cost control and quality assurance.
Although challenging, the task can be simplified by understanding product requirements, evaluating total costs, ensuring supplier reliability, and maintaining rigorous standards and testing.
By leveraging these strategies, purchasing departments can balance cost and quality effectively, contributing to the organization’s success in the marketplace.
資料ダウンロード
QCD調達購買管理クラウド「newji」は、調達購買部門で必要なQCD管理全てを備えた、現場特化型兼クラウド型の今世紀最高の購買管理システムとなります。
ユーザー登録
調達購買業務の効率化だけでなく、システムを導入することで、コスト削減や製品・資材のステータス可視化のほか、属人化していた購買情報の共有化による内部不正防止や統制にも役立ちます。
NEWJI DX
製造業に特化したデジタルトランスフォーメーション(DX)の実現を目指す請負開発型のコンサルティングサービスです。AI、iPaaS、および先端の技術を駆使して、製造プロセスの効率化、業務効率化、チームワーク強化、コスト削減、品質向上を実現します。このサービスは、製造業の課題を深く理解し、それに対する最適なデジタルソリューションを提供することで、企業が持続的な成長とイノベーションを達成できるようサポートします。
オンライン講座
製造業、主に購買・調達部門にお勤めの方々に向けた情報を配信しております。
新任の方やベテランの方、管理職を対象とした幅広いコンテンツをご用意しております。
お問い合わせ
コストダウンが利益に直結する術だと理解していても、なかなか前に進めることができない状況。そんな時は、newjiのコストダウン自動化機能で大きく利益貢献しよう!
(Β版非公開)