- お役立ち記事
- Digital tools for inventory cost reduction that procurement departments should utilize
Digital tools for inventory cost reduction that procurement departments should utilize
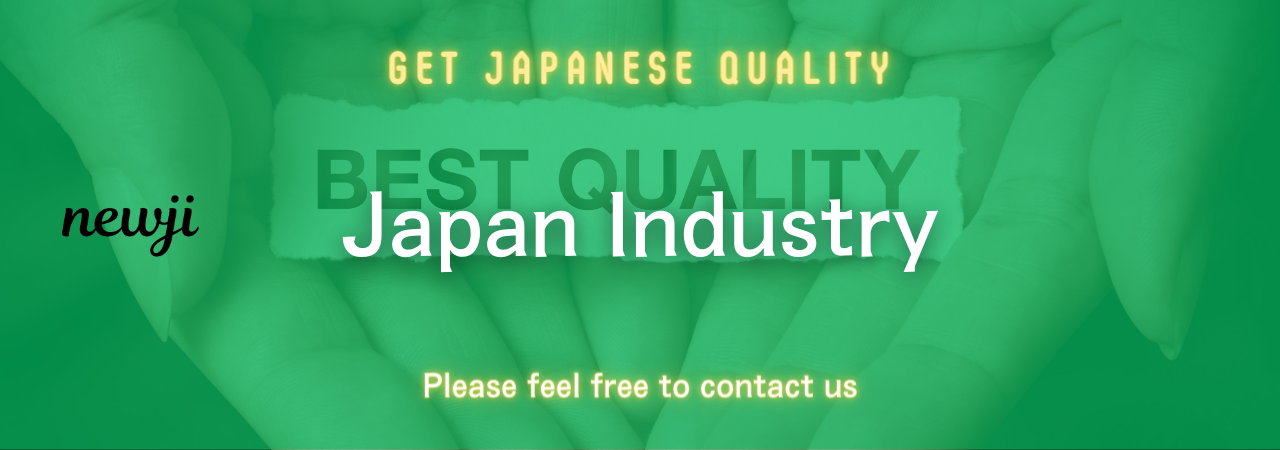
目次
Introduction to Inventory Cost Reduction
Procurement departments play a crucial role in managing inventory, balancing costs, and ensuring that a company has the necessary resources to operate efficiently.
In today’s competitive market, reducing inventory costs is more important than ever.
One effective strategy is leveraging digital tools designed specifically for inventory management.
These tools not only enhance accuracy but also provide insightful data analytics to guide decision-making.
In this article, we’ll explore digital tools that procurement departments should consider utilizing to reduce inventory costs effectively.
Understanding the Importance of Cost Reduction
Before delving into digital tools, it’s essential to understand why reducing inventory costs is vital.
Holding excessive inventory ties up capital that could otherwise be used for other business opportunities.
Furthermore, it increases storage costs and raises the risk of obsolescence.
On the other hand, insufficient inventory can lead to stockouts, disrupting operations and customer satisfaction.
Therefore, striking the right balance through effective inventory management is key to maintaining financial health and operational efficiency.
Digital Tools That Make a Difference
Several digital tools can help procurement departments streamline their processes, improve accuracy, and cut inventory costs.
Here are some of the most impactful ones:
Inventory Management Software
Inventory management software is the cornerstone of cost reduction in procurement.
These tools offer features such as real-time tracking, automated ordering, and comprehensive reporting.
By providing visibility into stock levels, they help avoid overstocking and understocking.
Moreover, these systems can be integrated with other business software, allowing for seamless data flow and enhanced decision-making.
Demand Forecasting Tools
Predicting future demand accurately is critical for optimizing inventory levels.
Demand forecasting tools use historical data, market trends, and statistical algorithms to predict future inventory requirements.
This allows procurement departments to make informed purchasing decisions, reducing excess inventory and minimizing stockouts.
Accurate demand forecasting is especially beneficial for seasonal businesses or those with fluctuating demand.
Supplier Relationship Management (SRM) Software
Building and maintaining healthy relationships with suppliers is key to cost reduction.
SRM software facilitates communication, negotiation, and performance monitoring with suppliers.
By having a clear view of supplier performance and pricing trends, procurement departments can negotiate better terms and ensure timely deliveries.
Additionally, SRM tools help identify areas for improvement, fostering long-term strategic partnerships with suppliers.
Automated Replenishment Systems
Automated replenishment systems are designed to streamline the ordering process.
These tools automatically reorder stock based on predefined triggers, such as minimum stock levels or predicted demand.
This reduces the need for manual intervention, minimizes human error, and ensures timely restocking.
Automated replenishment systems not only save time but also help maintain optimal inventory levels, ultimately reducing holding costs.
Advanced Analytics and Reporting
Data-driven decision-making is a hallmark of successful inventory management.
Advanced analytics tools provide detailed insights into inventory turnover, carrying costs, and demand patterns.
These reports enable procurement departments to identify inefficiencies, uncover cost-saving opportunities, and make data-backed decisions.
Leveraging powerful data analytics ensures that inventory strategies align with overall business goals.
Implementation Tips for Procurement Departments
Successfully adopting digital tools for inventory cost reduction involves more than just selecting the right software.
Here are some strategies to ensure a smooth implementation:
Assess Your Current Inventory Systems
Before incorporating digital tools, evaluate your existing inventory processes.
Identify weaknesses and areas where digital solutions can provide the most value.
A thorough assessment will guide tool selection and highlight processes that need improvement.
Set Clear Objectives
Define specific, measurable objectives for inventory cost reduction.
Your goals might include decreasing carrying costs, increasing inventory turnover, or reducing stockouts.
Clear objectives help guide the selection of digital tools and keep implementation focused.
Train Your Team
Ensure that your procurement team is well-trained on any new digital tools.
Comprehensive training will maximize the tools’ efficiency and enable your team to leverage all available features.
Consider ongoing training to keep up with software updates and best practices.
Monitor and Adjust
Regularly monitor the performance of your digital tools and their impact on inventory costs.
Collect feedback from your team and suppliers to identify any challenges or areas for improvement.
Continuously adjust your strategies and processes based on data and feedback to achieve optimal results.
Conclusion: Embracing Digital Transformation
Incorporating digital tools into procurement processes is essential for reducing inventory costs and improving overall business efficiency.
By utilizing inventory management software, demand forecasting tools, SRM systems, automated replenishment, and advanced analytics, procurement departments can make informed decisions, reduce waste, and optimize stock levels.
Successful implementation requires careful planning, clear objectives, and ongoing monitoring.
Embracing these digital tools is a strategic step towards achieving more efficient inventory management and maintaining a competitive edge in the marketplace.
資料ダウンロード
QCD調達購買管理クラウド「newji」は、調達購買部門で必要なQCD管理全てを備えた、現場特化型兼クラウド型の今世紀最高の購買管理システムとなります。
ユーザー登録
調達購買業務の効率化だけでなく、システムを導入することで、コスト削減や製品・資材のステータス可視化のほか、属人化していた購買情報の共有化による内部不正防止や統制にも役立ちます。
NEWJI DX
製造業に特化したデジタルトランスフォーメーション(DX)の実現を目指す請負開発型のコンサルティングサービスです。AI、iPaaS、および先端の技術を駆使して、製造プロセスの効率化、業務効率化、チームワーク強化、コスト削減、品質向上を実現します。このサービスは、製造業の課題を深く理解し、それに対する最適なデジタルソリューションを提供することで、企業が持続的な成長とイノベーションを達成できるようサポートします。
オンライン講座
製造業、主に購買・調達部門にお勤めの方々に向けた情報を配信しております。
新任の方やベテランの方、管理職を対象とした幅広いコンテンツをご用意しております。
お問い合わせ
コストダウンが利益に直結する術だと理解していても、なかなか前に進めることができない状況。そんな時は、newjiのコストダウン自動化機能で大きく利益貢献しよう!
(Β版非公開)