- お役立ち記事
- Quality and cost points that purchasing departments should consider when renewing supplier contracts
Quality and cost points that purchasing departments should consider when renewing supplier contracts
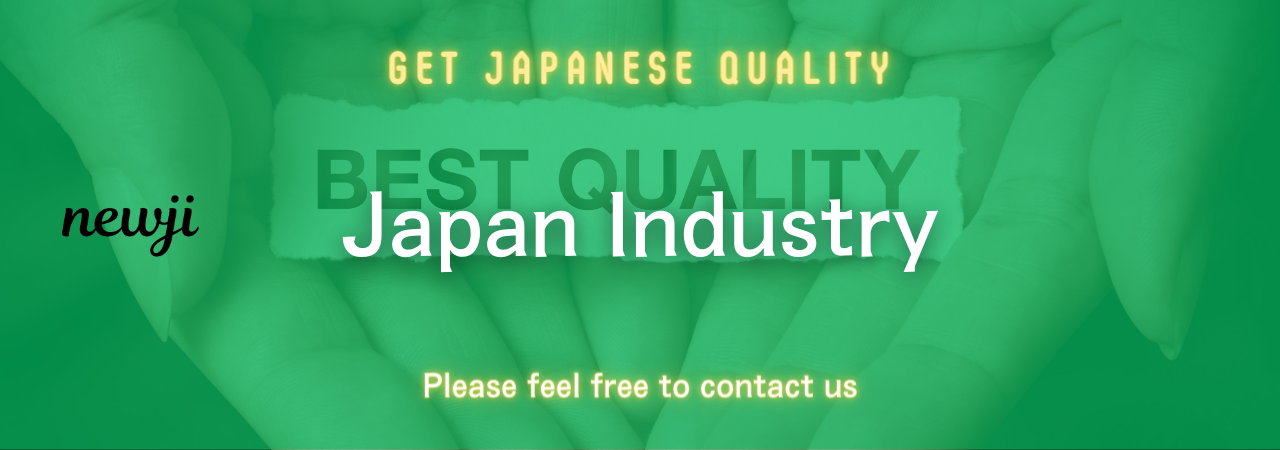
Understanding the Importance of Quality and Cost in Supplier Contracts
When renewing supplier contracts, purchasing departments face the critical task of balancing quality and cost.
This balance is essential to ensuring that companies receive the best value from their suppliers while maintaining high standards.
A well-negotiated contract can lead to a successful partnership that contributes to the company’s overall success.
Therefore, purchasing departments need to carefully evaluate both quality and cost factors during the renewal process.
In this article, we will explore the key considerations that purchasing teams should focus on to achieve a balance that benefits both the company and the supplier.
The Role of Quality in Supplier Contracts
Quality is a cornerstone of any supplier agreement.
It is vital because it directly impacts the final product or service that a company offers its customers.
High-quality inputs ensure that the end product meets customer expectations, enhancing the brand’s reputation and customer satisfaction.
Purchasing departments should establish clear quality standards that suppliers must meet or exceed.
The criteria should be detailed in the contract, covering aspects such as materials, production processes, and delivery timelines.
By setting these standards, companies can hold suppliers accountable and ensure conformity with the specified requirements.
To assess a supplier’s quality, purchasing teams may conduct thorough audits and inspections.
This includes evaluating the supplier’s production facilities, quality control processes, and compliance with industry standards.
By understanding a supplier’s capabilities, companies can make informed decisions about renewing contracts with vendors who consistently deliver quality products or services.
The Significance of Cost Considerations
While quality is crucial, cost is an equally important factor in renewing supplier contracts.
Controlling costs is key to maintaining a company’s profitability and competitive edge.
Purchasing departments must carefully analyze and compare supplier costs to determine the best value for money.
When examining costs, it’s important to look beyond initial price tags.
Contracts should include detailed breakdowns of expenses, such as raw materials, labor, transportation, and potential hidden fees.
Purchasing teams should also factor in costs associated with potential disruptions, such as delays and returns.
Negotiation plays a significant role in cost control.
Purchasing departments should work closely with suppliers to negotiate terms that are favorable for both parties.
This may involve exploring options for bulk purchasing, long-term agreements, or flexible payment terms that reduce financial strain.
Balancing Quality and Cost for Optimal Results
Achieving a balance between quality and cost is a strategic process that involves careful planning and analysis.
Purchasing departments should not sacrifice one for the other when renewing supplier contracts.
Instead, they should aim for a synergy that maximizes value.
To strike this balance, it’s beneficial to establish key performance indicators (KPIs) that monitor supplier performance.
KPIs can track metrics like product defect rates, on-time delivery statistics, and adherence to cost estimates.
These indicators provide valuable insights into how well a supplier is meeting the company’s quality and cost expectations.
Additionally, fostering strong relationships with suppliers is vital for successful contract renewals.
Building a partnership based on trust and transparency can lead to mutual benefits, such as improved quality and cost efficiency.
Regular communication with suppliers, discussing successes and areas for improvement, strengthens this relationship and facilitates smoother negotiations.
Adapting to Market Trends and Innovations
The business landscape is constantly evolving, and what worked previously might not be suitable for future needs.
Therefore, purchasing departments should remain adaptable and open to change when renewing contracts.
Staying informed about market trends and technological innovations allows companies to make data-driven decisions that enhance quality and reduce costs.
For example, advancements in manufacturing processes or materials can lead to quality improvements without significant cost increases.
Purchasing teams should assess whether their suppliers are leveraging these innovations to stay competitive.
If a supplier is invested in continuous improvement, it may indicate their commitment to providing quality services at competitive prices.
Evaluating Supplier Performance Over Time
Renewing supplier contracts is not just a one-time event; it is an ongoing process that requires continuous evaluation.
Purchasing departments should maintain detailed records of past performance, including quality assessments and cost analyses.
Regular performance reviews enable companies to identify patterns and trends in a supplier’s performance.
This historical data is invaluable during contract negotiations, helping teams make decisions based on facts rather than assumptions.
If a supplier consistently meets quality standards and offers competitive pricing, it strengthens their case for contract renewal.
On the other hand, persistent issues in quality or cost overruns may prompt reevaluation and consideration of alternative suppliers.
Conclusion
In conclusion, purchasing departments play a critical role in balancing quality and cost when renewing supplier contracts.
By focusing on clear quality standards, effective cost management, and strong supplier relationships, companies can optimize their supply chain operations.
Through ongoing evaluation and adaptation to market changes, purchasing teams can ensure that their supplier contracts align with the company’s objectives and customer expectations.
Ultimately, striking the right balance between quality and cost contributes to the organization’s overall success and competitiveness in the market.
資料ダウンロード
QCD調達購買管理クラウド「newji」は、調達購買部門で必要なQCD管理全てを備えた、現場特化型兼クラウド型の今世紀最高の購買管理システムとなります。
ユーザー登録
調達購買業務の効率化だけでなく、システムを導入することで、コスト削減や製品・資材のステータス可視化のほか、属人化していた購買情報の共有化による内部不正防止や統制にも役立ちます。
NEWJI DX
製造業に特化したデジタルトランスフォーメーション(DX)の実現を目指す請負開発型のコンサルティングサービスです。AI、iPaaS、および先端の技術を駆使して、製造プロセスの効率化、業務効率化、チームワーク強化、コスト削減、品質向上を実現します。このサービスは、製造業の課題を深く理解し、それに対する最適なデジタルソリューションを提供することで、企業が持続的な成長とイノベーションを達成できるようサポートします。
オンライン講座
製造業、主に購買・調達部門にお勤めの方々に向けた情報を配信しております。
新任の方やベテランの方、管理職を対象とした幅広いコンテンツをご用意しております。
お問い合わせ
コストダウンが利益に直結する術だと理解していても、なかなか前に進めることができない状況。そんな時は、newjiのコストダウン自動化機能で大きく利益貢献しよう!
(Β版非公開)