- お役立ち記事
- Lead time reduction is important in the procurement process and how to proceed effectively
Lead time reduction is important in the procurement process and how to proceed effectively
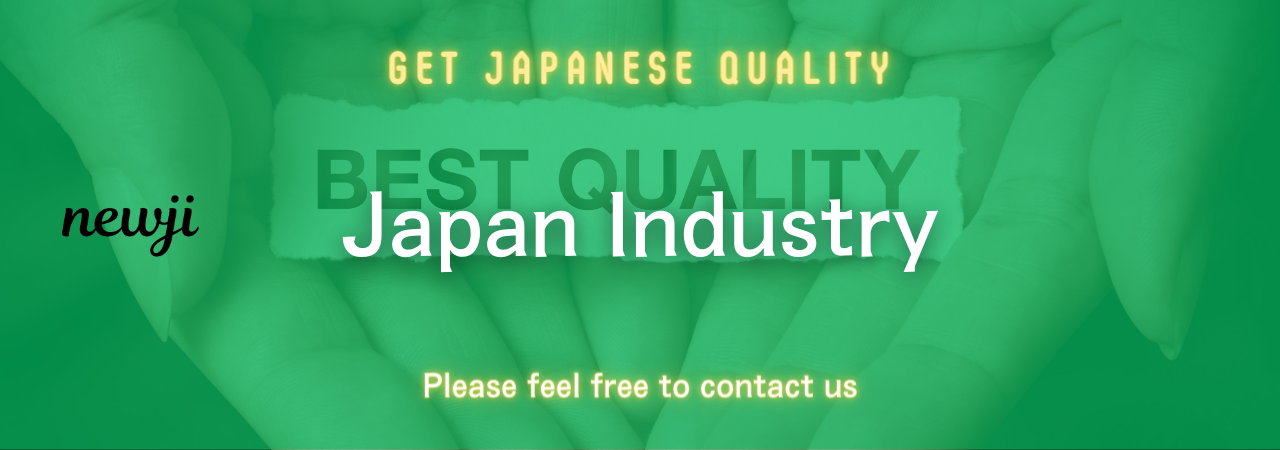
Understanding Lead Time in Procurement
In any business, especially those involved in manufacturing and retail, the procurement process is a vital component.
The timely acquisition of goods and services can significantly impact the overall efficiency and success of a company.
A critical aspect of this process is understanding and managing lead time.
Lead time is the duration between the initiation of a purchase request and the final delivery of the product or service.
Reducing lead time is crucial for optimizing the procurement process, ensuring that business operations run smoothly, and maintaining a competitive edge.
The Importance of Lead Time Reduction
Reducing lead time can lead to numerous benefits for a business.
First, it enhances the ability to respond promptly to market demands.
When a company can quickly procure necessary materials, it is better positioned to meet customers’ needs without delays.
Furthermore, shorter lead times can minimize inventory costs.
Businesses often need to keep safety stocks to counteract long lead times, leading to increased storage costs and the risk of inventory obsolescence.
By reducing lead time, companies can lower these costs and use their resources more efficiently.
Moreover, improved lead times can contribute to increased customer satisfaction.
Customers appreciate quick service, and businesses that can deliver swiftly are more likely to retain their clientele and gain positive referrals.
Factors Affecting Lead Time in Procurement
Several factors can influence lead time, and understanding them is crucial for effective reduction.
One significant factor is supplier reliability.
Suppliers that consistently deliver on time contribute positively to reduced lead time.
On the other hand, unreliable suppliers can cause delays, affecting the entire supply chain.
Transportation methods also play a role.
The choice between air, sea, or land transportation can impact how quickly goods are delivered.
Air transport, for example, is usually faster but more expensive than sea transport.
Additionally, internal processes such as approvals, order preparation, and payment processes can affect lead time.
Streamlining these steps can aid in faster procurement.
Strategies for Reducing Lead Time
Reducing lead time involves a combination of different strategies tailored to fit a company’s unique circumstances.
1. Strengthening Supplier Relationships
Building strong relationships with suppliers is highly beneficial.
Engaging with reliable suppliers who understand and align with your business needs can reduce delivery times.
Regular communication and feedback contribute to a more efficient procurement process.
2. Implementing Technology
Utilizing technology can significantly decrease lead times.
Implementing procurement software can automate and hasten processes like approvals and order tracking.
Additionally, advanced forecasting tools can predict demand more accurately, allowing for more efficient inventory management and procurement planning.
3. Reviewing and Optimizing Internal Processes
Taking a critical look at existing internal processes can identify areas of improvement.
Ensure that the approval processes are as straightforward as possible and that there are no unnecessary bureaucratic hurdles.
Automation tools can eliminate manual errors and accelerate processes, from order requests to payments.
4. Diversifying Supplier Base
Relying on a single supplier can be risky and lead to increased lead times if issues arise.
Diversifying the supplier base provides alternatives and increases flexibility and resilience in procurement operations.
It is best to include local and international suppliers to handle different needs effectively.
5. Optimizing Inventory Management
An optimized inventory management system can significantly reduce lead time.
Using strategies like Just-in-Time (JIT) can align inventory closely with production schedules, reducing excess stock and ensuring timely availability of materials.
Advanced inventory management systems can track and predict inventory levels, ensuring that reorder points are efficiently managed.
Monitoring and Measuring Lead Time
For ongoing success, businesses should continuously track and measure their lead times.
Establishing clear KPIs (Key Performance Indicators) related to lead time can help monitor progress and pinpoint issues when they arise.
Regular audits and reviews of procurement processes ensure that lead time reduction strategies continue to be effective and identify new areas for improvement.
Conclusion
In the fast-paced world of business, reducing lead time in procurement is a key component of ensuring agility and efficiency.
By understanding the factors that influence lead time and implementing effective strategies, businesses can enhance their procurement processes.
Ultimately, this leads to cost savings, better inventory management, and improved customer satisfaction.
Staying committed to continuous improvement and leveraging technology will further streamline operations and help companies maintain a competitive edge in their respective industries.
資料ダウンロード
QCD調達購買管理クラウド「newji」は、調達購買部門で必要なQCD管理全てを備えた、現場特化型兼クラウド型の今世紀最高の購買管理システムとなります。
ユーザー登録
調達購買業務の効率化だけでなく、システムを導入することで、コスト削減や製品・資材のステータス可視化のほか、属人化していた購買情報の共有化による内部不正防止や統制にも役立ちます。
NEWJI DX
製造業に特化したデジタルトランスフォーメーション(DX)の実現を目指す請負開発型のコンサルティングサービスです。AI、iPaaS、および先端の技術を駆使して、製造プロセスの効率化、業務効率化、チームワーク強化、コスト削減、品質向上を実現します。このサービスは、製造業の課題を深く理解し、それに対する最適なデジタルソリューションを提供することで、企業が持続的な成長とイノベーションを達成できるようサポートします。
オンライン講座
製造業、主に購買・調達部門にお勤めの方々に向けた情報を配信しております。
新任の方やベテランの方、管理職を対象とした幅広いコンテンツをご用意しております。
お問い合わせ
コストダウンが利益に直結する術だと理解していても、なかなか前に進めることができない状況。そんな時は、newjiのコストダウン自動化機能で大きく利益貢献しよう!
(Β版非公開)