- お役立ち記事
- Formulation and usage example of emergency procurement flow for purchasing department in response to material shortages
Formulation and usage example of emergency procurement flow for purchasing department in response to material shortages
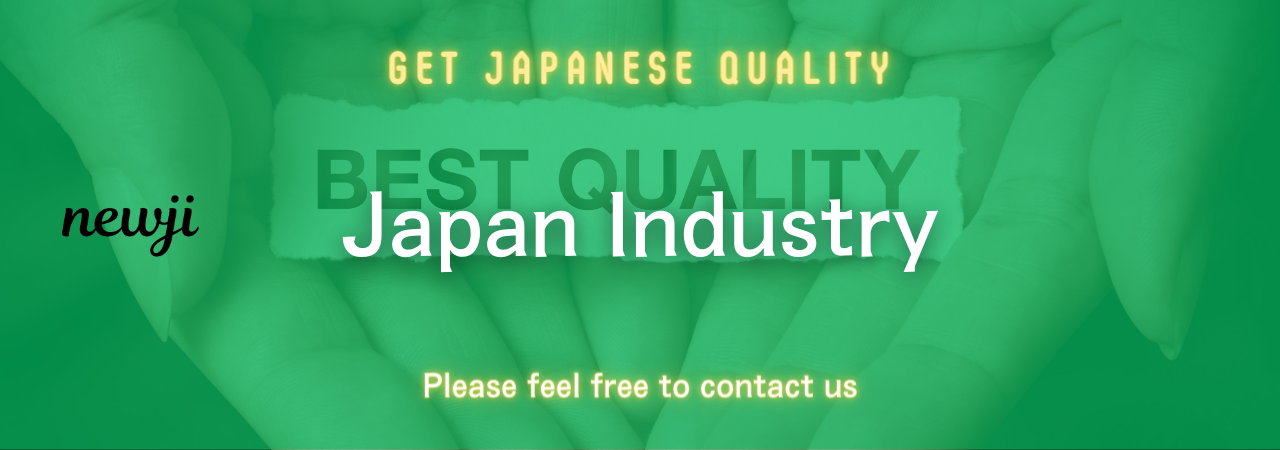
目次
Understanding Emergency Procurement
In today’s fast-paced world, unexpected situations often arise that necessitate immediate action from various departments within an organization.
One such situation is a sudden material shortage, which can disrupt normal operations and hamper production schedules.
To address this, many companies have developed emergency procurement flows specifically for their purchasing departments.
These processes ensure that the organization can quickly and efficiently respond to unforeseen circumstances, minimizing downtime and maintaining productivity.
What Is Emergency Procurement?
Emergency procurement refers to the rapid acquisition of goods or services in response to an unforeseen requirement.
Unlike regular procurement processes, which involve thorough planning, market research, and lengthy timelines, emergency procurement is executed with urgency.
Its primary aim is to secure the necessary materials swiftly to avoid any interruptions in operations.
Importance of Having an Emergency Procurement Plan
Having an emergency procurement plan in place is crucial for several reasons.
Firstly, it strengthens the resilience of the organization, ensuring that it can continue functioning despite unexpected challenges.
Secondly, it helps in maintaining customer satisfaction by avoiding delays in production or service delivery.
Lastly, it allows the company to make informed and controlled decisions, even under pressure, thus reducing the risk of avoidable mistakes and overspending.
Formulating an Effective Emergency Procurement Flow
Developing an effective emergency procurement flow requires careful consideration and detailed planning.
Here are some key steps to consider:
1. Identify Potential Risks
The first step in formulating an emergency procurement flow is to identify possible risks that might lead to material shortages.
This could include natural disasters, supplier failures, political unrest, or even sudden surges in demand.
Understanding these risks will help in crafting a targeted and effective procurement response.
2. Assess Current Inventory
A thorough assessment of the current inventory levels will provide valuable insights into how long current stocks can last during an emergency.
This assessment will aid in determining how quickly a response needs to be mobilized.
3. Establish Clear Procurement Policies
Establishing clear, concise procurement policies ensures that everyone involved understands their roles and responsibilities.
This includes end-to-end procedures for sourcing, ordering, and receiving emergency supplies, as well as designating decision-makers who can authorize urgent purchases.
4. Build Strong Supplier Relationships
Having a robust network of reliable suppliers is essential for successful emergency procurement.
Organizations should work closely with multiple vendors to ensure quick access to needed materials and negotiate agreements that include emergency clauses for expedited delivery terms.
5. Train the Procurement Team
Training the procurement team in emergency response procedures is crucial.
Regular workshops and drills can help familiarize the team with the process, allowing them to act confidently and efficiently during an actual crisis.
6. Implement Technological Solutions
Leveraging technology can greatly enhance the efficiency of the emergency procurement process.
Procurement software or ERP systems can speed up information sharing, tracking, and documentation, which is vital when decisions need to be made quickly.
Examples of Emergency Procurement Plans in Action
1. Natural Disaster Response
In the event of a natural disaster, such as an earthquake or flood, an emergency procurement plan would quickly mobilize to secure necessary materials like emergency supplies, repair equipment, or raw materials to maintain normal operations or support recovery efforts.
The swift action facilitated by pre-established procurement channels and supplier agreements can help mitigate the disaster’s impact on the business.
2. Supplier Failure
If a key supplier unexpectedly fails to deliver, an emergency procurement procedure allows the purchasing department to swiftly pivot to alternative suppliers.
Pre-negotiated contracts with backup suppliers ensure that production lines remain operational without significant delays.
3. Demand Spike
A sudden spike in demand for a product can strain existing resources.
In such scenarios, the emergency procurement flow enables rapid assessment of inventory needs and quick placement of orders with suppliers to replenish stock levels, thus preventing stockouts and capitalizing on the demand surge.
Final Thoughts
Emergency procurement is an indispensable part of modern business operations, especially in an era marked by rapid change and unforeseen challenges.
By having a well-defined emergency procurement flow, companies can enhance their resilience and adaptability, ensuring continuous operations in the face of adversity.
Purchasing departments, equipped with a robust plan, become a critical asset for maintaining stability and competitive advantage.
Adopting these practices not only prepares an organization for material shortages but also fosters a proactive approach to overall risk management.
資料ダウンロード
QCD調達購買管理クラウド「newji」は、調達購買部門で必要なQCD管理全てを備えた、現場特化型兼クラウド型の今世紀最高の購買管理システムとなります。
ユーザー登録
調達購買業務の効率化だけでなく、システムを導入することで、コスト削減や製品・資材のステータス可視化のほか、属人化していた購買情報の共有化による内部不正防止や統制にも役立ちます。
NEWJI DX
製造業に特化したデジタルトランスフォーメーション(DX)の実現を目指す請負開発型のコンサルティングサービスです。AI、iPaaS、および先端の技術を駆使して、製造プロセスの効率化、業務効率化、チームワーク強化、コスト削減、品質向上を実現します。このサービスは、製造業の課題を深く理解し、それに対する最適なデジタルソリューションを提供することで、企業が持続的な成長とイノベーションを達成できるようサポートします。
オンライン講座
製造業、主に購買・調達部門にお勤めの方々に向けた情報を配信しております。
新任の方やベテランの方、管理職を対象とした幅広いコンテンツをご用意しております。
お問い合わせ
コストダウンが利益に直結する術だと理解していても、なかなか前に進めることができない状況。そんな時は、newjiのコストダウン自動化機能で大きく利益貢献しよう!
(Β版非公開)