- お役立ち記事
- Measures to secure alternative suppliers for the purchasing department to avoid the risk of material shortages
Measures to secure alternative suppliers for the purchasing department to avoid the risk of material shortages
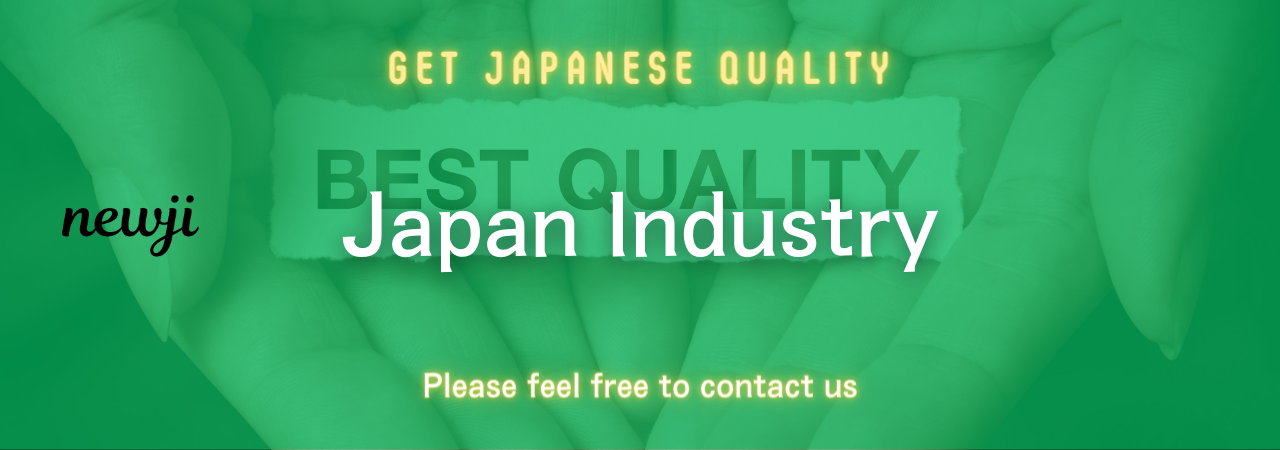
目次
Understanding Supply Chain Risks
In today’s globalized economy, businesses rely heavily on efficient supply chains to ensure they meet customer demands on time.
However, disruptions in the supply chain are not uncommon, and they can lead to material shortages, posing significant risks to business operations.
For purchasing departments, securing alternative suppliers is crucial to minimize these risks and maintain a steady flow of materials.
Identifying Potential Risks
To effectively secure alternative suppliers, it’s vital to first identify the potential risks that could lead to material shortages.
These risks can be categorized into several types:
– **Natural Disasters:** Events like earthquakes, floods, and hurricanes can disrupt production facilities and transport routes.
– **Political Instability:** Regions experiencing political unrest or changes in trade policies can affect supply chains.
– **Economic Fluctuations:** Sudden changes in the economic environment, such as currency fluctuations or market instability, can impact supplier operations.
– **Technological Failures:** Disruptions caused by cyberattacks or IT system failures can halt supply processes.
Understanding these risks allows purchasing departments to develop a comprehensive risk management strategy.
Developing a Contingency Plan
Once the potential risks are recognized, the next step is to develop a contingency plan.
This plan should outline the actions to be taken in response to a supply chain disruption and should include the identification of alternative suppliers.
Steps in Creating a Contingency Plan
1. **Risk Assessment:** Analyze the likelihood and impact of each potential risk on your supply chain.
2. **Supplier Identification:** Research and identify alternative suppliers who can provide the required materials.
3. **Supplier Evaluation:** Evaluate these suppliers based on criteria such as reliability, cost, and quality to ensure they meet your business needs.
4. **Contract Negotiation:** Establish agreements with these suppliers, including terms and conditions that allow flexible adjustment in times of need.
5. **Communication Plan:** Develop a communication strategy to promptly inform stakeholders about supply chain disruptions and the activation of contingency plans.
6. **Regular Review:** Periodically review and update the contingency plan to incorporate changes in market conditions or company requirements.
Building Strong Supplier Relationships
A robust relationship with suppliers is essential in securing reliable alternative sources.
This involves establishing open communication channels and fostering mutual trust and respect.
Good relationships can lead to favorable contract terms, prioritization during high demand, and better collaboration in problem-solving situations.
Ways to Strengthen Supplier Relationships
– **Regular Communication:** Maintain constant interaction with suppliers to discuss any concerns or changes.
– **Mutual Goals:** Align your business goals with those of your suppliers to create a shared vision for success.
– **Performance Monitoring:** Regularly assess supplier performance and provide feedback to ensure continued mutual improvement.
– **Conflict Resolution:** Address any disputes promptly and constructively to maintain a positive relationship.
Leveraging Technology
Incorporating technology into supply chain management makes it easier to identify and secure alternative suppliers.
Digital tools can enhance visibility, efficiency, and coordination in the supply chain.
Technological Tools for Supplier Management
– **Supply Chain Management Software:** This software provides real-time insights into supplier performance and supply chain disruptions.
– **Predictive Analytics:** These tools analyze data trends to predict potential disruptions and identify alternative suppliers proactively.
– **Blockchain Technology:** Ensures transparency and traceability in the supply chain, helping verify supplier credibility.
– **Artificial Intelligence:** AI can automate supplier evaluation processes and analyze vast amounts of data for better decision-making.
Conducting Regular Audits
Regular audits help ensure that alternative suppliers continue to meet the necessary standards and requirements.
This involves a thorough evaluation of their operational efficiency, compliance with regulations, financial stability, and capacity to scale production if needed.
Audit Best Practices
– **Scheduled Audits:** Perform audits at regular intervals to continuously assess supplier performance.
– **Unscheduled Audits:** Conduct surprise audits to get an accurate picture of the supplier’s capabilities.
– **Performance Metrics:** Use specific metrics to evaluate supplier efficiency, such as delivery times, defect rate, and cost management.
– **Feedback Loop:** Provide suppliers with audit results to encourage improvements and adjustments where necessary.
Staying Informed
Keeping abreast of the latest market trends and updates in regulations or political situations can assist purchasing departments in anticipating and adjusting to potential supply chain disruptions.
Methods to Stay Informed
– **Industry Reports:** Regularly read reports and analyses from reputable sources in your industry.
– **Networking:** Participate in industry conferences and trade shows to learn from peers and experts.
– **News Alerts:** Set up notifications for news related to your supply chain or supplier locations.
– **Consultation with Experts:** Engage with supply chain management consultants to gain deeper insights into upcoming challenges and opportunities.
Conclusion
Securing alternative suppliers is crucial for purchasing departments aiming to mitigate the risk of material shortages.
By understanding supply chain risks, developing a comprehensive contingency plan, building strong relationships with suppliers, leveraging technology, and conducting regular audits, businesses can ensure resilience and adaptability in their supply chain operations.
Continual learning and adaptation to market changes are also essential to staying ahead of potential disruptions.
資料ダウンロード
QCD調達購買管理クラウド「newji」は、調達購買部門で必要なQCD管理全てを備えた、現場特化型兼クラウド型の今世紀最高の購買管理システムとなります。
ユーザー登録
調達購買業務の効率化だけでなく、システムを導入することで、コスト削減や製品・資材のステータス可視化のほか、属人化していた購買情報の共有化による内部不正防止や統制にも役立ちます。
NEWJI DX
製造業に特化したデジタルトランスフォーメーション(DX)の実現を目指す請負開発型のコンサルティングサービスです。AI、iPaaS、および先端の技術を駆使して、製造プロセスの効率化、業務効率化、チームワーク強化、コスト削減、品質向上を実現します。このサービスは、製造業の課題を深く理解し、それに対する最適なデジタルソリューションを提供することで、企業が持続的な成長とイノベーションを達成できるようサポートします。
オンライン講座
製造業、主に購買・調達部門にお勤めの方々に向けた情報を配信しております。
新任の方やベテランの方、管理職を対象とした幅広いコンテンツをご用意しております。
お問い合わせ
コストダウンが利益に直結する術だと理解していても、なかなか前に進めることができない状況。そんな時は、newjiのコストダウン自動化機能で大きく利益貢献しよう!
(Β版非公開)