- お役立ち記事
- Specific measures for the purchasing department to shorten material procurement lead times
Specific measures for the purchasing department to shorten material procurement lead times
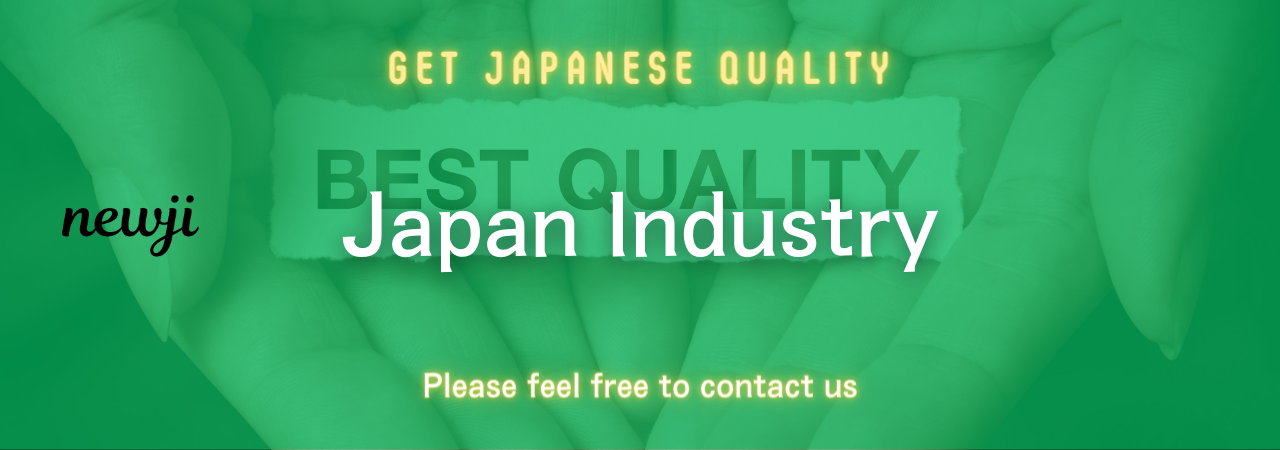
目次
Understanding Lead Times in Material Procurement
The purchasing department plays a crucial role in acquiring the materials necessary for a company’s manufacturing and operational processes.
One of the challenges faced by purchasing departments is managing lead times effectively.
Lead time is the period between placing an order and receiving the materials.
Understanding the factors contributing to lead times and implementing measures to shorten them can greatly enhance efficiency and productivity in the supply chain.
Factors Affecting Material Procurement Lead Times
Lead times in material procurement are influenced by a variety of factors.
First, supplier reliability is a major determinant.
Suppliers with consistent track records and efficient operations can fulfill orders more quickly.
Second, the complexity of the order itself may affect lead time.
Orders involving customized products or materials often take longer due to the additional processing required.
Third, transportation and shipping logistics significantly impact lead times, especially for international shipments which may face customs and regulatory delays.
Finally, internal company processes, such as approval workflows and inventory management systems, can also lengthen lead times if they are not streamlined.
Strategies to Shorten Lead Times
Establish Strong Relationships with Suppliers
Building strong, collaborative relationships with suppliers is vital for shortening lead times.
Open communication ensures that any potential delays are anticipated and can be managed proactively.
A good relationship also means that your company may be prioritized over others, leading to faster processing.
Consider working closely with suppliers to forecast demand accurately, thereby allowing them to prepare and allocate resources efficiently.
Diversify Your Supplier Base
Relying on a single supplier can be risky and may lead to longer lead times if issues arise.
Diversifying the supplier base can provide competitive options and safeguard against potential delays from any one supplier.
Having multiple sources for materials can reduce dependency and ensure that if one supplier is unable to deliver on time, others can step in without disrupting the process.
Streamline Internal Processes
Review and optimize internal processes related to procurement to shorten lead times.
Automating routine tasks such as order processing, approvals, and inventory checks can significantly reduce the time it takes to get orders out the door.
Implementing a centralized procurement platform that integrates with other systems within the company can provide better visibility and control over the entire procurement process.
Use Technology to Your Advantage
Leveraging technology can play a major role in reducing lead times.
E-procurement systems can simplify transaction processes and provide real-time data that help in making quick decisions.
Additionally, demand forecasting software can predict future needs accurately, allowing for better planning and order placement.
Tracking systems, such as GPS and RFID, can be used to monitor shipments and manage any logistical delays proactively.
Optimize Inventory Management
Effective inventory management is key to reducing lead times.
Utilize inventory management systems to maintain optimal stock levels and prevent stockouts or overstocking.
Safety stock levels should be reviewed frequently and adjusted based on consumption patterns and supplier reliability.
By managing inventory more effectively, orders can be placed just in time, reducing the need for large stockpiles and improving cash flow.
Negotiate Favorable Terms with Suppliers
Negotiating terms such as lead times, shipping methods, and order sizes with suppliers can also help shorten procurement times.
If possible, try securing contracts that include commitments for expedited delivery when necessary.
Additionally, discuss options for emergency shipments or partial deliveries that can keep operations running while waiting for full orders to arrive.
Monitor and Evaluate Performance
Regularly monitor and evaluate the performance of your suppliers and procurement processes.
Using key performance indicators (KPIs) related to lead times, delivery accuracy, and order fulfillment can provide valuable insights.
This information can be used to identify bottlenecks and areas for improvement, leading to more effective procurement strategies over time.
Conclusion
Shortening material procurement lead times requires a multi-faceted approach involving supplier management, internal process optimization, technology utilization, and strategic negotiation.
By understanding the factors that contribute to delays and implementing the strategies outlined above, purchasing departments can enhance their efficiency and responsiveness, ultimately contributing to the overall success and competitiveness of their organization.
資料ダウンロード
QCD調達購買管理クラウド「newji」は、調達購買部門で必要なQCD管理全てを備えた、現場特化型兼クラウド型の今世紀最高の購買管理システムとなります。
ユーザー登録
調達購買業務の効率化だけでなく、システムを導入することで、コスト削減や製品・資材のステータス可視化のほか、属人化していた購買情報の共有化による内部不正防止や統制にも役立ちます。
NEWJI DX
製造業に特化したデジタルトランスフォーメーション(DX)の実現を目指す請負開発型のコンサルティングサービスです。AI、iPaaS、および先端の技術を駆使して、製造プロセスの効率化、業務効率化、チームワーク強化、コスト削減、品質向上を実現します。このサービスは、製造業の課題を深く理解し、それに対する最適なデジタルソリューションを提供することで、企業が持続的な成長とイノベーションを達成できるようサポートします。
オンライン講座
製造業、主に購買・調達部門にお勤めの方々に向けた情報を配信しております。
新任の方やベテランの方、管理職を対象とした幅広いコンテンツをご用意しております。
お問い合わせ
コストダウンが利益に直結する術だと理解していても、なかなか前に進めることができない状況。そんな時は、newjiのコストダウン自動化機能で大きく利益貢献しよう!
(Β版非公開)