- お役立ち記事
- Challenges faced by purchasing departments in improving traceability across the supply chain
Challenges faced by purchasing departments in improving traceability across the supply chain
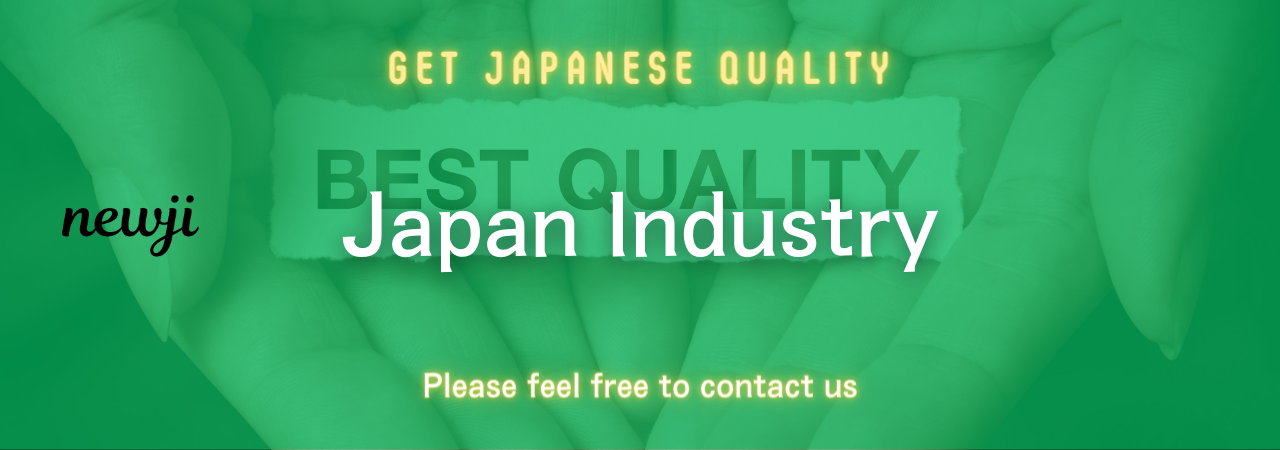
目次
Understanding Traceability in Supply Chains
In today’s global economy, effective supply chain management is crucial for businesses looking to remain competitive and efficient.
A significant component of supply chain management is traceability, which refers to the ability to track the movement of products and materials through each step of the production process.
This tracking is vital for ensuring quality, transparency, and compliance with regulations.
However, achieving robust traceability poses several challenges, particularly for purchasing departments, which play a pivotal role in procurement and supplier management.
The Importance of Traceability in the Supply Chain
Traceability is not just a buzzword; it represents a fundamental element of modern supply chains.
With increasing consumer awareness and stringent regulatory requirements, businesses are under pressure to ensure that their products are safe, ethical, and sustainable.
From raw materials to finished goods, being able to trace the origin and pathway of each component adds value by improving product quality, increasing supply chain transparency, and enhancing accountability.
Furthermore, traceability aids in risk management by enabling quick responses to product recalls, reducing waste, and preventing counterfeiting.
Compliance with Regulations
Governments worldwide are introducing regulations that mandate traceability in supply chains, particularly in sectors like food, pharmaceuticals, and electronics.
For purchasing departments, ensuring compliance means having detailed and accurate information on where materials are sourced and how they are processed.
Failure to comply can lead to heavy fines and penalties, thus making traceability an essential focus area.
Consumer Demands for Transparency
Consumers today are more informed and concerned about the ethical and environmental implications of their purchases.
They demand transparency from brands, wanting assurance that products are made responsibly and sustainably.
For purchasing departments, this means they must select suppliers willing to provide detailed data about their processes and certify the authenticity and quality of their goods.
Challenges in Improving Traceability
While the need for traceability is clear, there are numerous obstacles purchasing departments must overcome to improve it across the supply chain.
Complexity of Global Supply Chains
Today’s supply chains are complex and often span multiple countries, involving countless suppliers and sub-suppliers.
This complexity makes it challenging for purchasing departments to monitor every step and ensure accurate traceability.
Data must be accurately captured and securely shared across different systems, each potentially using different standards and protocols.
Lack of Standardization
There is no universal standard for traceability, which means companies often struggle with incompatible systems and processes.
This lack of standardization can result in data silos and communication barriers, complicating efforts to track products effectively.
Purchasing departments must work to overcome these hurdles by pushing for industry-wide adoption of standardized traceability protocols and technologies.
Technology Integration
Integrating technology into supply chain operations is essential for traceability.
However, the implementation of advanced systems such as blockchain, RFID, and IoT can be prohibitively expensive and requires significant investment in infrastructure and training.
Moreover, the challenge of coordinating various technological solutions across multiple suppliers is daunting, often creating resistance or reluctance to change.
Data Accuracy and Security
Effective traceability relies on the accuracy and integrity of data collected from each point in the supply chain.
Purchasing departments must ensure that the information is reliable and protected, which can be difficult given the extensive networks involved.
Ensuring data security is critical, as any breach could have severe implications for both companies and consumers.
Strategies for Overcoming Traceability Challenges
Though challenges exist, purchasing departments can employ several strategies to enhance traceability within their supply chains.
Developing Strong Supplier Relationships
Building strong partnerships with suppliers is essential.
Purchasing departments can work closely with suppliers to ensure they adhere to traceability practices and are willing to invest in necessary technologies.
Regular audits and assessments can help maintain supply chain integrity and ensure that suppliers are compliant with traceability requirements.
Leveraging Technology Solutions
Technology plays a crucial role in improving traceability.
Solutions like blockchain can provide a transparent, tamper-proof record of transactions, enhancing trust across the supply chain.
RFID and IoT devices can automate tracking and data collection, reducing the likelihood of human error and increasing efficiency.
Purchasing departments should evaluate and implement technology solutions that best fit their supply chain needs.
Standardization and Collaboration
Advocating for industry-wide standardization can greatly improve traceability efforts.
Purchasing departments can collaborate with other organizations, industry groups, and regulatory bodies to develop and adopt uniform standards.
Such collaboration increases interoperability and reduces friction in the supply chain, making it easier to track products globally.
Training and Education
Investing in training for employees and suppliers can foster a deeper understanding of the importance of traceability and the tools required to achieve it.
By educating team members and partners, purchasing departments ensure that all stakeholders are aligned with traceability goals.
Conclusion
Improving traceability across the supply chain is a challenging yet essential undertaking for purchasing departments.
While global supply chains present numerous obstacles, strategic planning, strong supplier relationships, and leveraging technology can enhance traceability efforts significantly.
By focusing on collaboration, standardization, and education, purchasing departments can help their organizations meet regulatory requirements, satisfy consumer demands, and ultimately build more responsible, transparent, and efficient supply chains.
資料ダウンロード
QCD調達購買管理クラウド「newji」は、調達購買部門で必要なQCD管理全てを備えた、現場特化型兼クラウド型の今世紀最高の購買管理システムとなります。
ユーザー登録
調達購買業務の効率化だけでなく、システムを導入することで、コスト削減や製品・資材のステータス可視化のほか、属人化していた購買情報の共有化による内部不正防止や統制にも役立ちます。
NEWJI DX
製造業に特化したデジタルトランスフォーメーション(DX)の実現を目指す請負開発型のコンサルティングサービスです。AI、iPaaS、および先端の技術を駆使して、製造プロセスの効率化、業務効率化、チームワーク強化、コスト削減、品質向上を実現します。このサービスは、製造業の課題を深く理解し、それに対する最適なデジタルソリューションを提供することで、企業が持続的な成長とイノベーションを達成できるようサポートします。
オンライン講座
製造業、主に購買・調達部門にお勤めの方々に向けた情報を配信しております。
新任の方やベテランの方、管理職を対象とした幅広いコンテンツをご用意しております。
お問い合わせ
コストダウンが利益に直結する術だと理解していても、なかなか前に進めることができない状況。そんな時は、newjiのコストダウン自動化機能で大きく利益貢献しよう!
(Β版非公開)