- お役立ち記事
- Strengthen quality control at business partners! Establishment of audit standards for purchasing personnel to practice
Strengthen quality control at business partners! Establishment of audit standards for purchasing personnel to practice
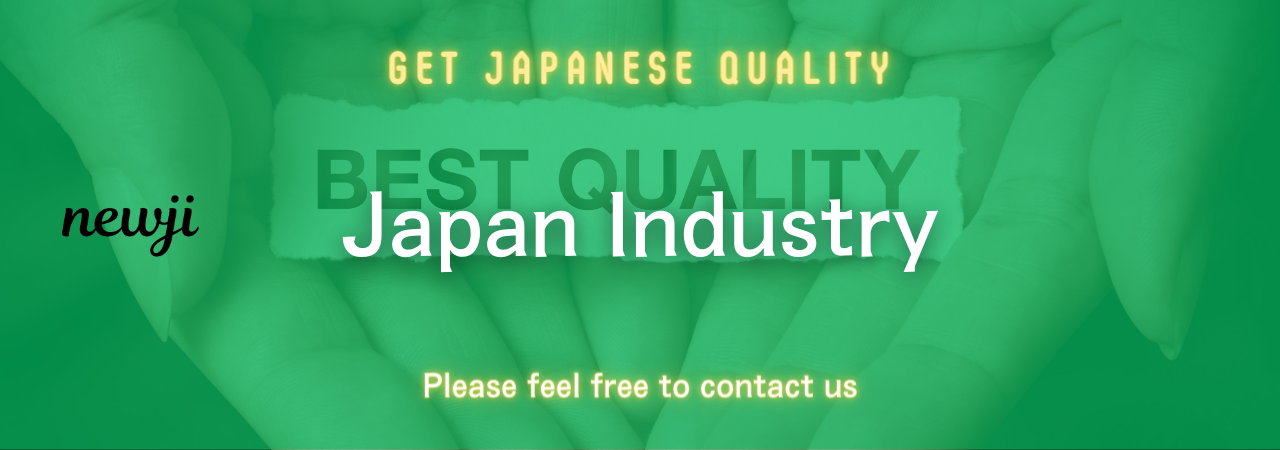
目次
Understanding the Importance of Quality Control
In today’s highly competitive business landscape, ensuring the quality of products is paramount for maintaining customer satisfaction and trust.
Quality control is a vital aspect that businesses cannot afford to overlook, especially when dealing with external partners or suppliers.
Implementing strict quality control measures can prevent costly errors and foster strong, long-lasting relationships with business partners.
Ensuring quality control at your business partners involves establishing comprehensive audit standards.
By doing so, purchasing personnel can maintain a clear understanding of the quality expectations and benchmarks that need to be met.
This not only assures the consistent quality of products but also strengthens the overall supply chain.
Establishing Effective Audit Standards
Developing audit standards requires a systematic approach to address various aspects of production and supply.
When purchasing personnel conduct audits, they evaluate compliance with these established guidelines.
It’s essential to define key areas to focus on during audits, ensuring all relevant factors are assessed.
1. Identify Critical Quality Metrics
To establish robust audit standards, businesses need to identify the critical quality metrics that pertain to their specific industry and products.
These metrics vary from one industry to another but typically involve parameters such as material specifications, manufacturing processes, and end-product testing.
It’s crucial to prioritize these metrics to ensure that the most vital aspects of product quality are always addressed.
By establishing clear key performance indicators (KPIs), purchasing personnel can objectively assess whether a business partner meets the required quality standards.
2. Develop Comprehensive Checklists
Having a detailed checklist is invaluable during audits.
It ensures purchasing personnel cover all necessary aspects, leaving no stone unturned.
A well-structured checklist provides a methodical approach to review quality control processes, documentation, and compliance with industry standards.
The checklist should include tangible elements such as documentation reviews, testing logs, raw material inspection records, and calibration of equipment.
Furthermore, it should also address intangible aspects like employee training and overall management of quality control within the partner organization.
3. Conduct Regular and Random Audits
Regular audits are fundamental in ensuring compliance and maintaining a consistent level of quality.
However, random audits can offer a more accurate picture of the day-to-day operations within a business partner’s facility.
These unannounced visits can reveal discrepancies and areas that may need improvement, providing a more comprehensive understanding of the partner’s commitment to quality.
Balancing between scheduled and random audits allows purchasing personnel to identify ongoing trends, address any recurring issues, and establish an open line of communication with the business partners.
Empowering Purchasing Personnel with Proper Training
For the audit standards to be effectively implemented, purchasing personnel need to be well-trained to conduct thorough audits.
They should be equipped with the knowledge and skills to identify quality issues and ensure compliance with the established standards.
1. In-depth Training Programs
Investing in comprehensive training programs is essential to empower purchasing personnel with the necessary tools and knowledge.
These programs should cover the fundamentals of quality control, industry-specific standards, and audit procedures.
Training should not be a one-time event, but rather a continuous learning process.
Regular updates and refresher courses keep personnel informed about new developments and emerging best practices in quality control.
2. Use of Advanced Tools and Technologies
The incorporation of advanced tools and technologies can significantly enhance the capabilities of purchasing personnel during audits.
Software solutions for data collection, analysis, and reporting can streamline the audit process, making it more efficient and effective.
By utilizing technology, auditors can obtain real-time data and insights, enabling quicker decision-making and identification of potential quality issues with business partners.
Building Strong Relationships with Business Partners
Quality control is not just about ensuring compliance and avoiding defects; it’s also about building and nurturing robust relationships with business partners.
Effective communication and collaboration are crucial elements in achieving this goal.
1. Transparent Communication
Open and transparent communication between the purchasing personnel and business partners is vital for establishing a successful quality control framework.
Sharing expectations, audit findings, and areas of improvement fosters a culture of collaboration and mutual understanding.
Regular meetings and discussions can help address any concerns and encourage partners to take proactive measures in adhering to quality standards.
This open dialogue incentivizes business partners to invest in their own quality control processes, creating a win-win situation for both parties.
2. Collaborative Improvements
Involving business partners in the process of improving quality control can lead to more sustainable changes.
Encouraging partners to suggest improvements and innovations ensures that all parties are committed to achieving the highest levels of quality.
Collaborative problem-solving sessions and knowledge-sharing workshops can be instrumental in developing best practices, ultimately strengthening the entire supply chain.
Conclusion
Strengthening quality control at business partners by establishing audit standards is an essential strategy for any business looking to maintain its reputation and customer satisfaction.
Through effective audits, proper training, the use of advanced technology, and fostering collaborative relationships with partners, purchasing personnel can significantly contribute to maintaining high-quality standards.
By taking these proactive steps, businesses can ensure that their products consistently meet or exceed industry standards, thereby enhancing customer confidence and achieving long-term success.
資料ダウンロード
QCD調達購買管理クラウド「newji」は、調達購買部門で必要なQCD管理全てを備えた、現場特化型兼クラウド型の今世紀最高の購買管理システムとなります。
ユーザー登録
調達購買業務の効率化だけでなく、システムを導入することで、コスト削減や製品・資材のステータス可視化のほか、属人化していた購買情報の共有化による内部不正防止や統制にも役立ちます。
NEWJI DX
製造業に特化したデジタルトランスフォーメーション(DX)の実現を目指す請負開発型のコンサルティングサービスです。AI、iPaaS、および先端の技術を駆使して、製造プロセスの効率化、業務効率化、チームワーク強化、コスト削減、品質向上を実現します。このサービスは、製造業の課題を深く理解し、それに対する最適なデジタルソリューションを提供することで、企業が持続的な成長とイノベーションを達成できるようサポートします。
オンライン講座
製造業、主に購買・調達部門にお勤めの方々に向けた情報を配信しております。
新任の方やベテランの方、管理職を対象とした幅広いコンテンツをご用意しております。
お問い合わせ
コストダウンが利益に直結する術だと理解していても、なかなか前に進めることができない状況。そんな時は、newjiのコストダウン自動化機能で大きく利益貢献しよう!
(Β版非公開)