- お役立ち記事
- New evaluation metrics and application examples for purchasing departments to manage material procurement risks
New evaluation metrics and application examples for purchasing departments to manage material procurement risks
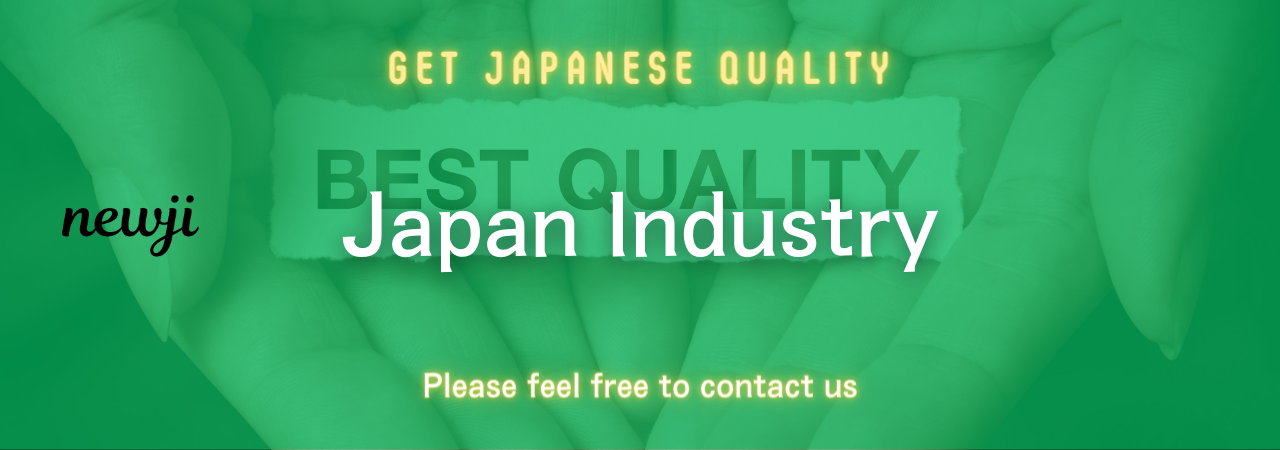
目次
Understanding Procurement Risks
In the complex arena of material procurement, managing risks is a vital aspect that purchasing departments must handle effectively.
Procurement risks refer to the potential for failures in acquiring goods and services that are crucial for a company’s operations.
These risks can stem from a variety of sources including supplier issues, market volatility, logistical challenges, and compliance with regulations.
Failure to manage these risks may lead to supply chain disruptions, increased costs, and even reputational damage.
Given the multifaceted nature of procurement risks, adopting robust evaluation metrics and strategies is essential for purchasing departments.
These metrics help in quantifying and mitigating potential risks, thus ensuring the smooth flow of materials necessary for production and operational processes.
Key Metrics for Evaluating Procurement Risks
To effectively manage procurement risks, purchasing departments can rely on a variety of evaluation metrics.
These provide a structured approach to identify, analyze, and mitigate potential vulnerabilities in the supply chain.
Supplier Reliability Index
A crucial metric in managing procurement risk is the Supplier Reliability Index.
This index evaluates a supplier’s performance based on historical data, including reliability in meeting delivery schedules, quality standards, and responsiveness to inquiries.
A high reliability score indicates a supplier that is trustworthy, reducing the likelihood of supply chain disruptions.
Market Risk Analysis
Market risk analysis involves assessing the potential impact of various market factors on procurement.
These factors include price fluctuations, market trends, and geopolitical developments that could affect the availability and cost of materials.
By analyzing market risks, departments can implement strategies such as hedging or diversifying supplier bases.
Cost-Benefit Analysis
Cost-benefit analysis is a strategic tool for evaluating procurement decisions.
It involves comparing the expected costs of purchasing a particular material with the anticipated benefits, such as enhanced production efficiency or quality improvements.
This metric helps determine the financial viability of procurement choices while considering potential risks.
Compliance and Regulatory Risk
Purchasing departments must also consider compliance and regulatory risks.
This metric measures the potential impact of non-compliance with industry standards or government regulations.
By ensuring compliance, companies can avoid legal penalties and maintain their reputation.
Application Examples for Managing Procurement Risks
By understanding and applying these evaluation metrics, purchasing departments can significantly enhance their risk management processes.
Here are some application examples that illustrate how these metrics can be effectively utilized.
Case Study: Diversifying the Supplier Base
A manufacturing company faced risks due to heavy reliance on a single supplier for critical components.
Using the Supplier Reliability Index, they discovered potential vulnerabilities in the supplier’s ability to meet growing demand.
In response, the company diversified its supplier base to include multiple reliable vendors.
This decision reduced dependency on one supplier and minimized risks associated with production downtime and quality issues.
Market Risk Adaptation in a Fabrication Firm
A fabrication firm monitored price trends and geopolitical developments through Market Risk Analysis.
By identifying potential market risks early, they could implement hedging strategies to lock in material prices for future contracts.
This approach allowed the firm to stabilize costs, preventing unforeseen spikes from affecting profitability.
Cost-Benefit Analysis in a Tech Company
A tech company performed a Cost-Benefit Analysis for the procurement of new hardware components.
The analysis revealed that while initial costs were high, the long-term benefits of increased processing speed and reduced operational downtimes outweighed the expenses.
Such evaluations ensured that procurement decisions aligned with the company’s financial and strategic goals while minimizing risks.
Navigating Compliance Risks in the Pharmaceutical Industry
In the pharmaceutical industry, compliance is critical.
A pharmaceutical company assessed Compliance and Regulatory Risks when importing raw materials from different countries.
By ensuring all suppliers adhered to international quality standards and local regulations, the company avoided legal issues and maintained its product quality, safeguarding its market reputation.
The Future of Procurement Risk Management
The landscape of procurement risk management is evolving, with increasing emphasis on digital solutions and predictive analytics.
Technologies like AI and machine learning are now being integrated into procurement processes to anticipate risks with greater accuracy.
Digital platforms can automate data collection and analysis, providing real-time insights into supplier performance, market trends, and regulatory changes.
As these technologies continue to advance, purchasing departments will benefit from more agile and responsive risk management strategies.
This evolution will facilitate proactive decision-making, minimizing potential disruptions and optimizing the procurement process.
In this dynamic environment, continuous learning and adaptation will be key to managing procurement risks effectively.
In conclusion, by employing comprehensive evaluation metrics and adaptive strategies, purchasing departments can significantly mitigate risks associated with material procurement.
The integration of digital technologies further enhances risk management capabilities, setting a strong foundation for sustainable and efficient procurement operations.
資料ダウンロード
QCD調達購買管理クラウド「newji」は、調達購買部門で必要なQCD管理全てを備えた、現場特化型兼クラウド型の今世紀最高の購買管理システムとなります。
ユーザー登録
調達購買業務の効率化だけでなく、システムを導入することで、コスト削減や製品・資材のステータス可視化のほか、属人化していた購買情報の共有化による内部不正防止や統制にも役立ちます。
NEWJI DX
製造業に特化したデジタルトランスフォーメーション(DX)の実現を目指す請負開発型のコンサルティングサービスです。AI、iPaaS、および先端の技術を駆使して、製造プロセスの効率化、業務効率化、チームワーク強化、コスト削減、品質向上を実現します。このサービスは、製造業の課題を深く理解し、それに対する最適なデジタルソリューションを提供することで、企業が持続的な成長とイノベーションを達成できるようサポートします。
オンライン講座
製造業、主に購買・調達部門にお勤めの方々に向けた情報を配信しております。
新任の方やベテランの方、管理職を対象とした幅広いコンテンツをご用意しております。
お問い合わせ
コストダウンが利益に直結する術だと理解していても、なかなか前に進めることができない状況。そんな時は、newjiのコストダウン自動化機能で大きく利益貢献しよう!
(Β版非公開)