- お役立ち記事
- A risk assessment model for purchasing departments to stabilize material supply
A risk assessment model for purchasing departments to stabilize material supply
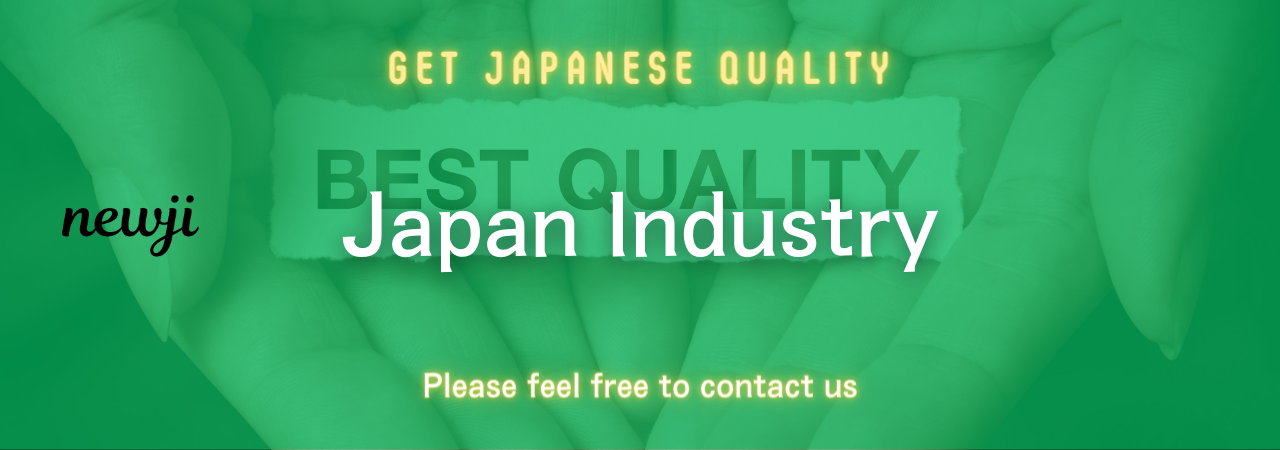
目次
Understanding the Importance of a Risk Assessment Model
In today’s global market, purchasing departments play a crucial role in ensuring a steady supply of materials to keep operations running smoothly.
However, they face a myriad of risks that can potentially disrupt material supply chains.
To counter these challenges, implementing a risk assessment model becomes imperative for purchasing departments to stabilize the supply of materials.
A risk assessment model aids in identifying, analyzing, and mitigating risks within the supply chain.
By focusing on potential threats, purchasing departments can develop strategies to manage and minimize disruptions, ensuring that the flow of materials remains consistent and reliable.
Identifying Risks in the Supply Chain
Purchasing departments must first identify the various risks that could impact their supply chain.
These risks encompass a wide range of factors, including natural disasters, geopolitical tensions, supplier bankruptcy, and even fluctuations in market demand.
Additionally, unforeseen events like pandemics can bring unexpected challenges, affecting supply chains on a global scale.
By cataloging these risks, purchasing departments can begin to understand their potential impact.
This understanding is the first step toward developing a robust risk assessment model that can protect against supply chain interruptions.
Natural Disasters
Natural disasters such as hurricanes, earthquakes, and floods can severely disrupt supply chains.
These events can damage infrastructure, delay shipments, and even halt production for extended periods.
A risk assessment model will help purchasing departments evaluate the likelihood of such events and their possible impact on the supply chain.
Geopolitical Tensions
Political instability, trade tariffs, and sanctions can all influence global supply chains.
These geopolitical factors can restrict access to materials, increase costs, and create uncertainty.
An effective risk assessment model will help identify regions that may be affected by such tensions and establish contingency plans.
Supplier Bankruptcy
Reliance on a single supplier or a limited number of suppliers poses a significant risk should any of them encounter financial difficulties.
Supplier bankruptcy can result in sudden disruptions in the supply chain.
A risk assessment model should include evaluating the financial stability of suppliers and developing strategies to diversify sourcing.
Market Demand Fluctuations
Demand for materials can vary due to economic shifts, consumer preferences, and technological advancements.
These changes can lead to shortages or surpluses, both of which present challenges for purchasing departments.
A risk assessment model should analyze market trends and incorporate forecasting to anticipate shifts in demand.
Developing a Risk Assessment Model
Once potential risks are identified, the next step is developing a risk assessment model tailored to the specific needs of the purchasing department.
This model should include processes for risk evaluation, prioritization, and mitigation.
Risk Evaluation
Risk evaluation requires a thorough analysis of the likelihood and potential impact of each identified risk.
This analysis can be quantitative, utilizing statistical methods, or qualitative, based on expert judgment and historical data.
The goal is to assess the potential severity of each risk and determine which pose the greatest threat to supply chain stability.
Risk Prioritization
With a comprehensive evaluation in place, purchasing departments can prioritize risks based on their likelihood and impact.
High-priority risks should be addressed first, ensuring that mitigation strategies are in place for the most significant threats to the supply chain.
Risk Mitigation Strategies
Risk mitigation involves developing strategies to manage or reduce the impact of identified risks.
This can include diversifying suppliers, investing in inventory buffers, or implementing alternative transportation routes.
Supplier relationship management, fostering strong partnerships, and continuous communication can also mitigate risks by creating more resilient and collaborative supply chains.
Implementing and Monitoring the Model
Implementing a risk assessment model within the purchasing department requires collaboration and coordination with various stakeholders.
Clear communication of the model’s objectives and benefits is essential to gain support and alignment across the organization.
Once implemented, continuous monitoring and review are necessary to ensure the model remains effective.
Regular assessments can identify new risks and evaluate the efficacy of existing mitigation strategies.
Feedback loops and adaptive processes enable purchasing departments to refine and enhance the model over time.
The Benefits of a Risk Assessment Model
Adopting a risk assessment model offers several advantages for purchasing departments.
It enhances visibility into potential risks and provides a structured approach to mitigate them.
This proactive stance leads to improved supply chain stability and resilience, minimizing disruptions and safeguarding operations.
Moreover, by preparing for potential risks, purchasing departments can optimize inventory levels, reduce costs, and enhance supplier relationships.
The foresight and preparedness fostered by a robust risk assessment model contribute to the overall competitive advantage of the organization.
In conclusion, a risk assessment model is an invaluable tool for purchasing departments striving to stabilize material supply.
By identifying, prioritizing, and mitigating risks, these departments can navigate the complexities of global supply chains and maintain a consistent flow of materials.
This proactive approach ensures operational continuity and supports long-term business success.
資料ダウンロード
QCD調達購買管理クラウド「newji」は、調達購買部門で必要なQCD管理全てを備えた、現場特化型兼クラウド型の今世紀最高の購買管理システムとなります。
ユーザー登録
調達購買業務の効率化だけでなく、システムを導入することで、コスト削減や製品・資材のステータス可視化のほか、属人化していた購買情報の共有化による内部不正防止や統制にも役立ちます。
NEWJI DX
製造業に特化したデジタルトランスフォーメーション(DX)の実現を目指す請負開発型のコンサルティングサービスです。AI、iPaaS、および先端の技術を駆使して、製造プロセスの効率化、業務効率化、チームワーク強化、コスト削減、品質向上を実現します。このサービスは、製造業の課題を深く理解し、それに対する最適なデジタルソリューションを提供することで、企業が持続的な成長とイノベーションを達成できるようサポートします。
オンライン講座
製造業、主に購買・調達部門にお勤めの方々に向けた情報を配信しております。
新任の方やベテランの方、管理職を対象とした幅広いコンテンツをご用意しております。
お問い合わせ
コストダウンが利益に直結する術だと理解していても、なかなか前に進めることができない状況。そんな時は、newjiのコストダウン自動化機能で大きく利益貢献しよう!
(Β版非公開)