- お役立ち記事
- Successful implementation of supplier management system led by purchasing department
Successful implementation of supplier management system led by purchasing department
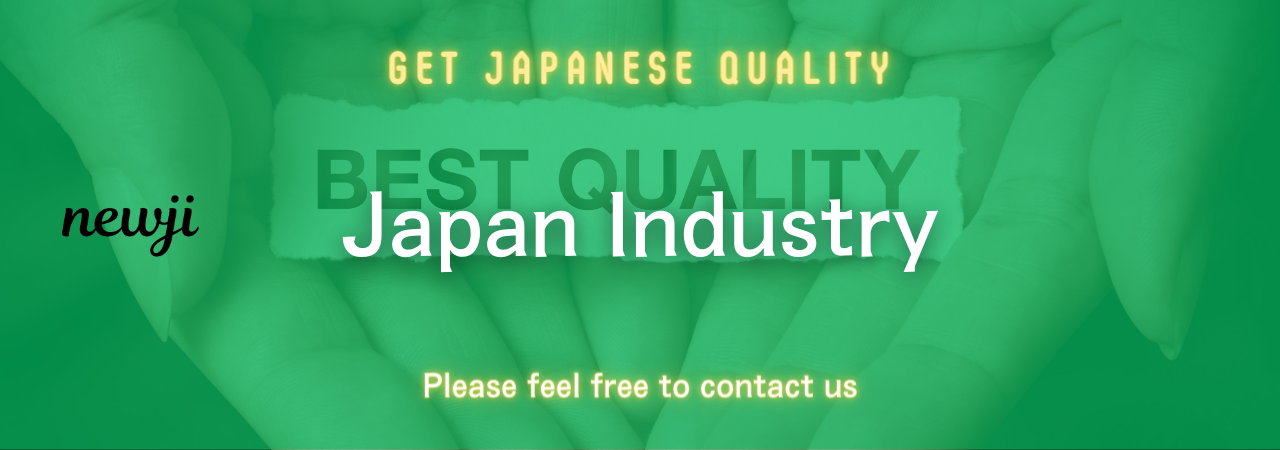
目次
Understanding Supplier Management Systems
Supplier management systems are integral tools used by purchasing departments to streamline interactions with suppliers, manage supply chain operations, and enhance overall business efficiency.
These systems are designed to provide clear visibility and control over supplier performance, contracts, and risks associated with procurement.
With a well-implemented supplier management system, businesses can achieve better collaboration with suppliers, ensure quality products and services, and attain competitive pricing.
Benefits of a Supplier Management System
Implementing a supplier management system offers numerous advantages.
It optimizes procurement processes and facilitates a strategic approach to managing supplier relationships.
Such systems enhance operational efficiency by automating routine tasks like purchase orders, invoices, and performance evaluations.
As a result, the purchasing department can focus on strategic decision-making rather than getting bogged down with administrative duties.
Improved supplier performance is another major benefit.
A comprehensive system allows the purchasing department to monitor supplier activities closely, identifying areas for improvement and providing feedback.
This leads to a more productive partnership and ensures that supplier outputs align with business standards and expectations.
Cost savings can also be realized through a supplier management system.
By granting better access to market data and performance insights, these systems empower the purchasing department to negotiate more favorable terms with suppliers.
This results in reduced procurement costs and improved profit margins for the business.
The Role of the Purchasing Department in Implementation
The purchasing department plays a pivotal role in the successful implementation of a supplier management system.
They are the primary users of these systems and are responsible for overseeing the transition from traditional methods to automated tools.
Strategizing and Planning
Before implementation begins, the purchasing department needs to develop a comprehensive strategy and plan.
This involves assessing current supplier management practices, identifying objectives, and defining the desired outcomes of the new system.
It is crucial to establish clear metrics for success and involve key stakeholders, including IT support and supplier relationship managers, in the planning process.
Collaboration with Suppliers
Effective collaboration with suppliers is vital during the implementation phase.
The purchasing department should communicate the changes to suppliers and involve them in the process.
Providing training sessions and resources can help suppliers understand how to use the new system effectively.
This establishes transparency and fosters cooperation, leading to a smoother transition and better acceptance of the new processes.
Training and Support
Training is a crucial step in implementing a supplier management system.
The purchasing department must ensure that all team members are adequately trained to use the system.
This includes understanding system features, data entry protocols, and reporting tools.
Ongoing support should be available to address any issues or questions that may arise post-implementation.
Overcoming Challenges in Implementation
The transition to a supplier management system is not without challenges.
However, with careful planning and execution, these challenges can be effectively managed.
Data Management
One common challenge is data management.
Transferring existing data to the new system requires meticulous attention to detail to prevent inaccuracies and data loss.
The purchasing department should work closely with IT departments to ensure data integrity and continuity.
Resistance to Change
Resistance to change is another hurdle.
Employees and suppliers may be hesitant to adopt new technologies.
To overcome this, the purchasing department can communicate the benefits of the new system clearly, highlighting how it will improve workflows and provide value to everyone involved.
System Integration
Integration with existing systems is essential for a seamless operation.
The purchasing department must ensure that the new supplier management system can integrate with current enterprise resource planning (ERP) systems or other internal platforms.
This requires technical expertise and may involve working with software vendors to customize solutions as needed.
Measuring Success
After implementing a supplier management system, it’s critical to measure its success.
The purchasing department should track key performance indicators (KPIs) such as supplier compliance rates, cost savings, and procurement cycle times.
Regular reviews and audits should be conducted to evaluate the system’s impact and identify areas for further optimization.
Continuous Improvement
The journey doesn’t end with implementation.
Continuous improvement should be a priority.
The purchasing department can gather feedback from users to refine the system and adapt to evolving business needs.
This proactive approach ensures that the supplier management system remains an effective tool for achieving strategic sourcing goals.
Conclusion
In conclusion, a successful implementation of a supplier management system led by the purchasing department involves thorough planning, effective collaboration, and continuous improvement.
By taking an active role in the process, the purchasing department can ensure that the system delivers enhanced efficiency, improved supplier performance, and significant cost savings for the business.
As technology continues to evolve, embracing these systems becomes increasingly important for maintaining a competitive edge in today’s dynamic market.
資料ダウンロード
QCD調達購買管理クラウド「newji」は、調達購買部門で必要なQCD管理全てを備えた、現場特化型兼クラウド型の今世紀最高の購買管理システムとなります。
ユーザー登録
調達購買業務の効率化だけでなく、システムを導入することで、コスト削減や製品・資材のステータス可視化のほか、属人化していた購買情報の共有化による内部不正防止や統制にも役立ちます。
NEWJI DX
製造業に特化したデジタルトランスフォーメーション(DX)の実現を目指す請負開発型のコンサルティングサービスです。AI、iPaaS、および先端の技術を駆使して、製造プロセスの効率化、業務効率化、チームワーク強化、コスト削減、品質向上を実現します。このサービスは、製造業の課題を深く理解し、それに対する最適なデジタルソリューションを提供することで、企業が持続的な成長とイノベーションを達成できるようサポートします。
オンライン講座
製造業、主に購買・調達部門にお勤めの方々に向けた情報を配信しております。
新任の方やベテランの方、管理職を対象とした幅広いコンテンツをご用意しております。
お問い合わせ
コストダウンが利益に直結する術だと理解していても、なかなか前に進めることができない状況。そんな時は、newjiのコストダウン自動化機能で大きく利益貢献しよう!
(Β版非公開)