- お役立ち記事
- Purchasing department supplier evaluation techniques to minimize quality risks
Purchasing department supplier evaluation techniques to minimize quality risks
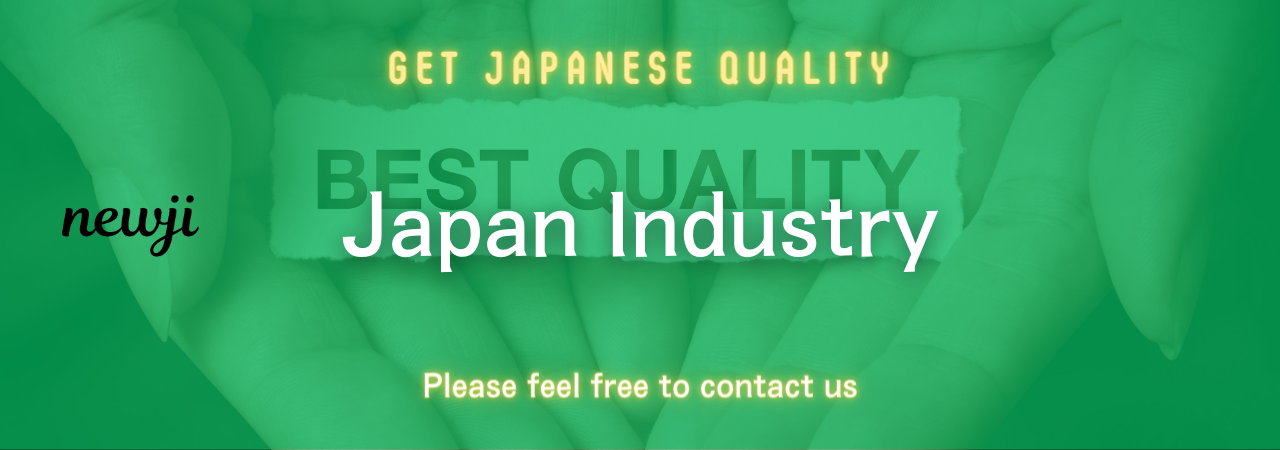
目次
Introduction to Supplier Evaluation
In the dynamic world of procurement, ensuring that the products received meet quality standards is critical.
The purchasing department plays a pivotal role in evaluating suppliers to minimize quality risks.
By implementing effective supplier evaluation techniques, organizations can safeguard their operations and uphold the standards that their businesses and customers expect.
Supplier evaluation is not merely about assessing the performance; it’s also about fostering relationships that can lead to continuous improvement.
Through strategic assessments, purchasing departments can pinpoint which suppliers will deliver consistently and which may pose risks.
Understanding Quality Risks
Before delving into the specifics of supplier evaluation, it’s important to understand what constitutes quality risks.
These risks can drastically impact a company’s operations and include issues such as late deliveries, substandard materials, and non-compliance with regulations.
The ripple effect of these risks can affect production timelines, product reliability, and ultimately, the company’s reputation.
To tackle these challenges, organizations must establish a robust supplier evaluation process.
Ensuring that each supplier is reliable and capable is paramount to sustaining quality.
Key Techniques for Supplier Evaluation
1. Establish Clear Criteria
One of the most foundational techniques in supplier evaluation is setting clear, measurable criteria.
These criteria should reflect the organization’s specific needs and priorities.
They often include factors such as delivery performance, quality of goods, cost-effectiveness, and flexibility.
Clear criteria ensure that evaluations are objective, consistent, and transparent.
They also allow suppliers to understand what is expected of them and align their operations accordingly.
2. Conduct Regular Audits
Supplier audits are essential for evaluating a supplier’s operational capacity and quality management standards.
These audits allow purchasing departments to verify processes, transparency, and adherence to regulatory and internal standards.
Conducting regular audits helps in identifying any gaps or areas for improvement and enables companies to take corrective action proactively.
These audits should include on-site visits as well as inspections of documentation and processes.
3. Implement a Scorecard System
A supplier scorecard is an effective tool for quantifying supplier performance.
By evaluating suppliers against predetermined metrics, purchasing departments can easily assess the overall performance and decide whether to continue or end the partnership.
Scorecards usually include quantitative data points such as delivery timelines and defect rates.
They can also incorporate qualitative assessments such as supplier relationship status and responsiveness.
4. Engage in Continuous Monitoring
Continuous monitoring involves keeping track of supplier performance over time.
This ongoing evaluation process helps in early detection of potential issues and provides an opportunity for timely intervention.
Technological solutions like supply chain management software can assist in tracking real-time performance data, facilitating better decision-making and coordination.
Developing Supplier Relationships
Effective supplier evaluation goes hand-in-hand with developing strong supplier relationships.
Building a collaborative partnership ensures open communication, allowing issues to be resolved more efficiently.
Encouraging feedback and regularly meeting with suppliers can foster a culture of mutual respect and understanding.
Suppliers who feel valued and engaged are more likely to strive for continuous improvement, ultimately reducing quality risks.
Leveraging Technology in Supplier Evaluation
Technological advancements have revolutionized how purchasing departments evaluate suppliers.
Digital tools and software solutions can streamline the process, making it more efficient and less prone to errors.
1. E-Procurement Systems
E-procurement systems offer an integrated platform for managing supplier information, performance evaluations, and communications.
These systems allow for real-time data collection and analysis, which is crucial for prompt decision-making.
2. Data Analytics Tools
Data analytics tools can process large volumes of data and provide insights into supplier performance trends.
These insights enable purchasing departments to make informed decisions based on historical and predictive data trends.
Overcoming Challenges in Supplier Evaluation
While the techniques mentioned are effective, purchasing departments may encounter challenges when implementing supplier evaluations.
These include resistance from suppliers, data collection difficulties, and resource constraints.
Overcoming these challenges requires commitment from organizational leadership and cross-departmental collaboration.
Investing in training for procurement staff and fostering a culture of quality can go a long way in mitigating these obstacles.
Conclusion
Evaluating suppliers is a critical activity for any purchasing department looking to minimize quality risks.
With clear criteria, regular audits, scorecards, continuous monitoring, and strong relationships, organizations can ensure that they collaborate with reliable suppliers.
By leveraging technology and addressing implementation challenges head-on, businesses can establish a robust supplier evaluation process that supports their strategic goals.
The end result is a supply chain that not only meets but exceeds quality expectations, thus protecting the organization’s integrity and success in the long term.
資料ダウンロード
QCD調達購買管理クラウド「newji」は、調達購買部門で必要なQCD管理全てを備えた、現場特化型兼クラウド型の今世紀最高の購買管理システムとなります。
ユーザー登録
調達購買業務の効率化だけでなく、システムを導入することで、コスト削減や製品・資材のステータス可視化のほか、属人化していた購買情報の共有化による内部不正防止や統制にも役立ちます。
NEWJI DX
製造業に特化したデジタルトランスフォーメーション(DX)の実現を目指す請負開発型のコンサルティングサービスです。AI、iPaaS、および先端の技術を駆使して、製造プロセスの効率化、業務効率化、チームワーク強化、コスト削減、品質向上を実現します。このサービスは、製造業の課題を深く理解し、それに対する最適なデジタルソリューションを提供することで、企業が持続的な成長とイノベーションを達成できるようサポートします。
オンライン講座
製造業、主に購買・調達部門にお勤めの方々に向けた情報を配信しております。
新任の方やベテランの方、管理職を対象とした幅広いコンテンツをご用意しております。
お問い合わせ
コストダウンが利益に直結する術だと理解していても、なかなか前に進めることができない状況。そんな時は、newjiのコストダウン自動化機能で大きく利益貢献しよう!
(Β版非公開)