- お役立ち記事
- A collaborative strategy for purchasing departments to drive supply chain efficiency
A collaborative strategy for purchasing departments to drive supply chain efficiency
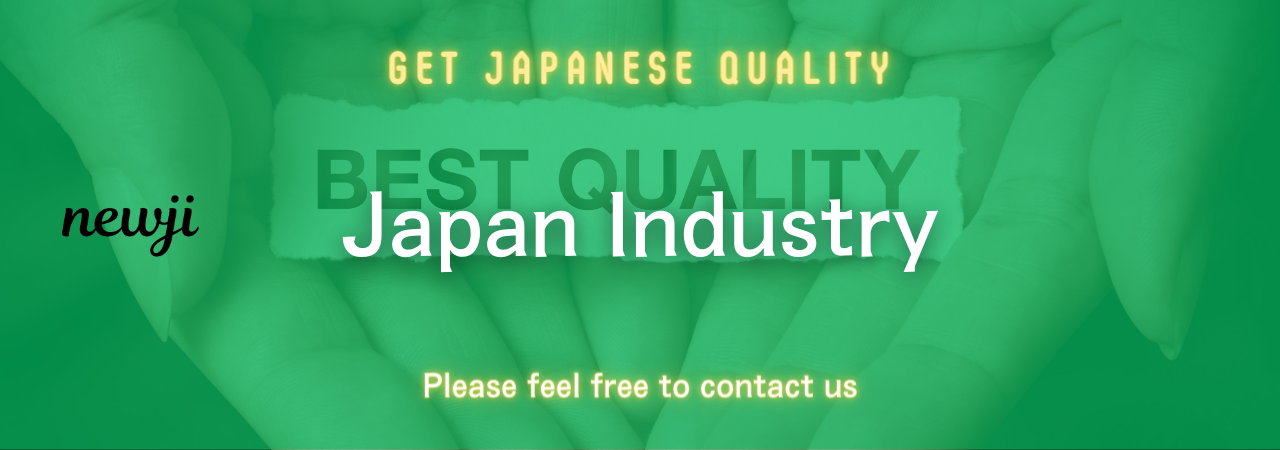
目次
Understanding the Role of the Purchasing Department
The purchasing department plays a crucial role in the overall efficiency of a supply chain.
They are responsible for acquiring the goods and services that a company needs to operate.
Their work ensures that production is not stalled due to a lack of materials, maintaining a consistent flow through the supply chain.
Their effectiveness impacts not just immediate concerns, such as cost and quality, but also broader aspects like supplier relationships and long-term business strategies.
In a competitive market, these responsibilities mean purchasing departments must operate both strategically and collaboratively.
The Importance of Collaboration
Collaboration in the context of a purchasing department means working closely with various stakeholders, such as suppliers, internal departments, and even competitors.
The aim is to create a more efficient, responsive, and robust supply chain.
Effective collaboration can lead to numerous benefits, including cost savings, improved quality, and reduced lead times.
Working together consistently helps in better forecasting of demand, optimizing inventory levels, and ensuring timely delivery of products.
Such synergy can lead to innovation, as shared insights enable more creative solutions that might be missed when working in silos.
Building Strong Supplier Relationships
One of the key aspects of a collaborative strategy in purchasing is fostering strong relationships with suppliers.
When a purchasing department views suppliers as partners rather than mere vendors, both parties can work towards mutual goals.
Regular communication and feedback are essential to building trust and understanding.
This partnership can lead to better-negotiated contracts with favorable terms for both the purchaser and supplier.
Moreover, involving suppliers early in the product development process can lead to enhanced innovation and product improvements.
Such involvement often results in suppliers being more invested in the success of the project, leading to potential advantages such as priority delivery or access to limited resources.
Integrating Technology in Purchasing
Incorporating technology into the purchasing process is a powerful way to enhance collaboration and efficiency.
Using digital tools can automate routine tasks, provide data-driven insights, and enable seamless communication pathways.
Supply chain management software can provide real-time updates on inventory levels, order statuses, and supplier performance.
This visibility helps the purchasing department to make informed decisions quickly and accurately.
Furthermore, technology can facilitate better collaboration through platforms that enable secure and efficient communication with suppliers and internal teams.
E-procurement systems, for example, can streamline the purchasing process, reducing the time spent on manual tasks.
Challenges in Technology Integration
Despite its benefits, integrating technology into purchasing can present challenges.
There is often a steep learning curve involved with new systems, and resistance to change can hinder adoption.
Investing in the right training for staff and ensuring that systems are user-friendly can mitigate these issues.
Data security is another concern, as sensitive information must be protected against breaches.
Robust security measures and regular audits help to safeguard company data while maintaining trust with suppliers.
Cross-Departmental Collaboration
Purchasing departments must work closely with other internal departments to improve supply chain efficiency.
For example, collaborating with the finance department ensures that purchasing decisions align with the company’s budget and financial strategies.
It also helps in negotiating better payment terms with suppliers, providing cash flow flexibility for the company.
Involving the marketing department in discussions can help anticipate market demands, allowing the purchasing department to plan for changes in supply needs effectively.
Working with operations, on the other hand, ensures that production schedules and material deliveries are synchronized, minimizing downtime and optimizing resource use.
Benchmarking and Performance Measurement
To drive supply chain efficiency, it is vital for purchasing departments to continuously measure and evaluate their performance.
Benchmarking against industry standards and competitors provides insights into where improvements are needed.
Key performance indicators (KPIs) such as cost savings, procurement cycle time, and supplier performance need regular analysis.
A clear understanding of these metrics can highlight inefficiencies and guide strategic adjustments.
Using these evaluations, purchasing departments can redefine priorities, focusing efforts on areas that offer the most significant potential for improvement.
This approach ensures that the department remains a proactive contributor to the company’s success rather than a reactive element.
The Future of Purchasing in Supply Chain Efficiency
As global supply chains become more complex, the purchasing department’s role will continue to evolve.
Sustainability, for example, is becoming a significant consideration, with companies aiming to reduce their carbon footprints and operate more responsibly.
Purchasing departments can contribute by sourcing eco-friendly materials and working with suppliers committed to sustainability.
Moreover, as supply chains become more digitized and data-driven, purchasing departments will need to harness analytical skills to interpret data and make strategic decisions.
This evolution will enhance their ability to not only react to market changes but anticipate them, positioning companies to thrive in rapidly changing environments.
In conclusion, a collaborative strategy within purchasing departments is essential for driving supply chain efficiency.
By fostering relationships, integrating technology, working across departments, and focusing on continuous improvement, purchasing departments can become pivotal in enhancing overall business performance.
資料ダウンロード
QCD調達購買管理クラウド「newji」は、調達購買部門で必要なQCD管理全てを備えた、現場特化型兼クラウド型の今世紀最高の購買管理システムとなります。
ユーザー登録
調達購買業務の効率化だけでなく、システムを導入することで、コスト削減や製品・資材のステータス可視化のほか、属人化していた購買情報の共有化による内部不正防止や統制にも役立ちます。
NEWJI DX
製造業に特化したデジタルトランスフォーメーション(DX)の実現を目指す請負開発型のコンサルティングサービスです。AI、iPaaS、および先端の技術を駆使して、製造プロセスの効率化、業務効率化、チームワーク強化、コスト削減、品質向上を実現します。このサービスは、製造業の課題を深く理解し、それに対する最適なデジタルソリューションを提供することで、企業が持続的な成長とイノベーションを達成できるようサポートします。
オンライン講座
製造業、主に購買・調達部門にお勤めの方々に向けた情報を配信しております。
新任の方やベテランの方、管理職を対象とした幅広いコンテンツをご用意しております。
お問い合わせ
コストダウンが利益に直結する術だと理解していても、なかなか前に進めることができない状況。そんな時は、newjiのコストダウン自動化機能で大きく利益貢献しよう!
(Β版非公開)