- お役立ち記事
- Management methods to prepare for global logistics issues and procurement risks
Management methods to prepare for global logistics issues and procurement risks
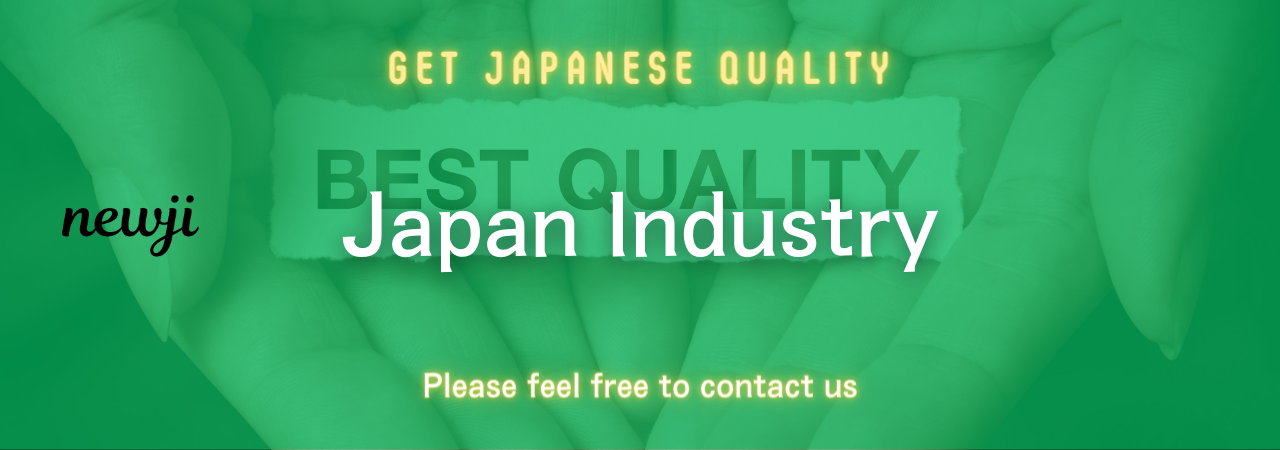
目次
Understanding Global Logistics Issues
Global logistics is a critical aspect of modern business, impacting both the efficiency of operations and the overall success of an organization.
However, this vast network is often susceptible to numerous challenges, due to factors such as economic fluctuations, geopolitical tensions, and natural disasters.
These issues can disrupt supply chains, leading to delays, increased costs, and potential losses.
Logistics issues can arise from various sources.
Trade barriers, such as tariffs and sanctions, can increase operational costs and complicate international transactions.
Transportation bottlenecks, caused by port congestion or labor strikes, can result in significant delays.
Furthermore, technological disruptions, such as cybersecurity threats or equipment failures, also pose significant risks.
Understanding these potential risks is the first step toward managing them effectively.
Businesses must adopt proactive strategies to mitigate the impact of these issues on their operations.
Key Methods for Managing Global Logistics
1. Diversifying Supply Chains
One effective strategy to mitigate logistics risks is to diversify supply chains.
By sourcing materials from multiple suppliers in different regions, companies can reduce their dependency on a single supplier or geographic location.
This not only reduces the risk posed by regional disruptions but also enhances negotiation power and flexibility.
Businesses should regularly evaluate their supply chain networks and consider establishing relationships with suppliers in alternative locations.
In addition, collaborative partnerships can leverage shared resources and insights, fostering resilience against disruptions.
2. Implementing Technology Solutions
Technological advancements are changing the logistics landscape, offering new tools for prediction and optimization.
Investing in technology, such as Internet of Things (IoT) devices and advanced analytics, provides real-time visibility into supply chains.
This visibility enables businesses to anticipate disruptions and respond swiftly.
Moreover, digital platforms can streamline communication and collaboration with partners, improving coordination and efficiency.
Automation and artificial intelligence can optimize inventory management, reducing waste and enhancing agility in response to demand fluctuations.
3. Building Flexible Logistics Strategies
Flexibility is crucial in building resilient logistics operations.
Developing contingency plans is one way to ensure flexibility.
These plans should outline alternate routes, modes of transport, or suppliers, allowing businesses to pivot quickly in response to unexpected events.
Moreover, flexible contracts with logistic service providers can help adapt to changing circumstances.
Adaptive pricing models and service agreements ensure that businesses maintain service levels while managing costs effectively.
Tackling Procurement Risks
Procurement is another vital area closely linked to logistics, facing its own set of challenges.
Risks in procurement could stem from supplier failures, fluctuating prices, or compliance issues.
Such risks not only impact logistics but also affect production schedules and financial performance.
1. Establishing Strong Supplier Relationships
Strong supplier relationships are fundamental in mitigating procurement risks.
Building trust and collaboration with suppliers can enhance reliability and quality assurance.
Regular communication ensures that expectations are aligned, and any potential issues are discussed promptly.
Companies should also assess the financial stability and performance track record of their suppliers.
This evaluation helps identify reliable partners capable of supporting long-term business goals.
2. Leveraging Data Analytics
Data-driven decision-making is critical in managing procurement risks effectively.
Analytics can uncover patterns and trends, allowing businesses to forecast demand accurately and plan procurement activities accordingly.
Predictive analytics can also anticipate supplier disruptions or market changes, providing insights for proactive strategies.
By leveraging data, companies can optimize inventory levels, align procurement strategies with business objectives, and enhance cost efficiency.
3. Emphasizing Sustainable Procurement
Sustainability is becoming a focal point in procurement strategies.
Adopting sustainable practices not only mitigates risks but also enhances brand reputation and consumer trust.
Sourcing materials responsibly and ensuring ethical supply chain operations are key components.
Sustainable procurement initiatives can include selecting suppliers committed to environmental standards or integrating sustainability criteria in supplier evaluations.
These practices can safeguard against regulatory compliance risks and align with broader corporate social responsibility goals.
Conclusion: A Holistic Approach
Managing global logistics issues and procurement risks requires a comprehensive approach anchored in flexibility, technology, and collaboration.
By diversifying supply chains, leveraging technology, and fostering strong supplier relationships, businesses can build resilient operations capable of withstanding disruptions.
Emphasizing data analytics and sustainable procurement enhances decision-making, aligning operations with broader business strategies.
As the global landscape continues to evolve, businesses must remain vigilant and adaptable to succeed in managing logistics and procurement challenges effectively.
A proactive stance, underpinned by strategic planning and innovative solutions, will enable companies to navigate the complexities of global logistics and safeguard against procurement risks.
This holistic approach not only ensures operational continuity but also enhances competitive advantage in today’s dynamic marketplace.
資料ダウンロード
QCD調達購買管理クラウド「newji」は、調達購買部門で必要なQCD管理全てを備えた、現場特化型兼クラウド型の今世紀最高の購買管理システムとなります。
ユーザー登録
調達購買業務の効率化だけでなく、システムを導入することで、コスト削減や製品・資材のステータス可視化のほか、属人化していた購買情報の共有化による内部不正防止や統制にも役立ちます。
NEWJI DX
製造業に特化したデジタルトランスフォーメーション(DX)の実現を目指す請負開発型のコンサルティングサービスです。AI、iPaaS、および先端の技術を駆使して、製造プロセスの効率化、業務効率化、チームワーク強化、コスト削減、品質向上を実現します。このサービスは、製造業の課題を深く理解し、それに対する最適なデジタルソリューションを提供することで、企業が持続的な成長とイノベーションを達成できるようサポートします。
オンライン講座
製造業、主に購買・調達部門にお勤めの方々に向けた情報を配信しております。
新任の方やベテランの方、管理職を対象とした幅広いコンテンツをご用意しております。
お問い合わせ
コストダウンが利益に直結する術だと理解していても、なかなか前に進めることができない状況。そんな時は、newjiのコストダウン自動化機能で大きく利益貢献しよう!
(Β版非公開)