- お役立ち記事
- Practical examples of achieving both quality and cost through multi-supplier procurement
Practical examples of achieving both quality and cost through multi-supplier procurement
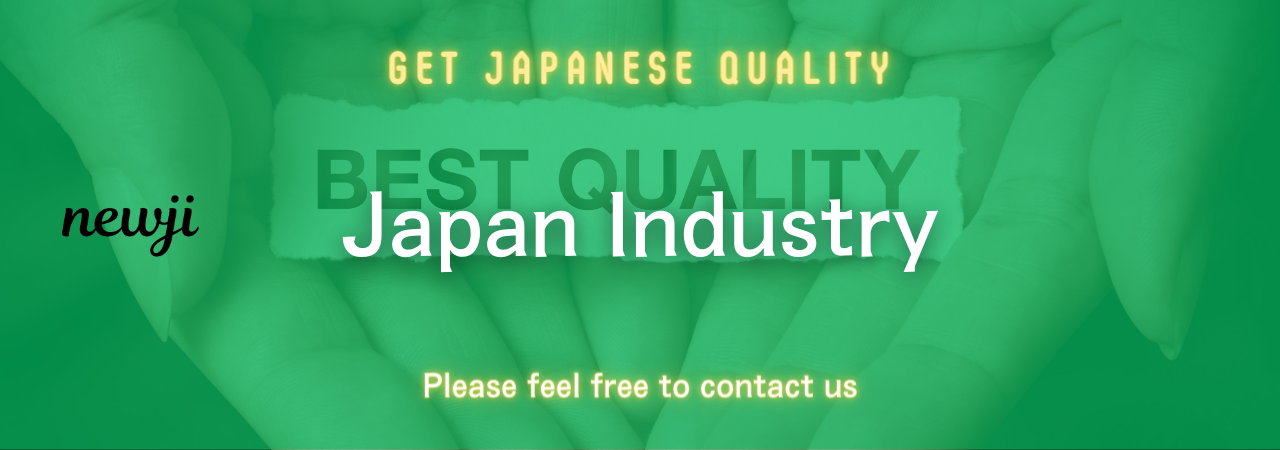
目次
Introduction to Multi-Supplier Procurement
In today’s competitive business environment, companies are constantly looking for ways to improve their operations, reduce costs, and ensure the highest quality of products and services.
One effective strategy that many businesses employ is multi-supplier procurement.
This approach allows companies to engage multiple suppliers, thereby enhancing their ability to manage costs and maintain quality standards.
In this article, we will explore practical examples of how businesses can effectively achieve both quality and cost efficiency through multi-supplier procurement.
The Basics of Multi-Supplier Procurement
Multi-supplier procurement is the practice of acquiring goods or services from several different suppliers rather than relying on a single source.
This approach diversifies risk, fosters competition among suppliers, and provides companies with greater flexibility.
By having multiple suppliers, businesses can ensure a steady supply chain, even if one supplier faces a problem.
Moreover, it allows companies to take advantage of competitive pricing without compromising on quality.
Balancing Quality and Cost
Achieving a balance between quality and cost is the ultimate goal of any procurement strategy.
With multi-supplier procurement, companies can achieve this balance by leveraging competition among suppliers and requiring them to adhere to strict quality standards.
Case Study: A Manufacturing Firm
Consider a manufacturing firm that produces consumer electronics.
By employing a multi-supplier procurement strategy, the firm can source critical components such as microchips, displays, and casings from multiple suppliers.
This strategy enables the firm to negotiate better pricing, as suppliers compete to offer the most favorable terms.
Additionally, the firm requires each supplier to meet specific quality benchmarks before their components are accepted.
As a result, the firm can maintain high-quality standards while minimizing costs.
Case Study: A Retail Company
A retail company that specializes in clothing can benefit significantly from multi-supplier procurement.
By engaging with various textile manufacturers, the retailer can compare prices and quality across different batches of fabrics.
This allows the company to strategically select suppliers that offer the best combination of price and quality.
Moreover, the retailer can quickly switch suppliers if one fails to meet quality expectations or if another offers a better price, thus ensuring continuous improvement and cost efficiency.
Benefits of Multi-Supplier Procurement
Implementing a multi-supplier procurement strategy presents numerous advantages beyond just cost and quality management.
Risk Mitigation
Relying on a single supplier can present significant risks, such as supply chain disruptions, quality issues, or supplier bankruptcy.
By diversifying the supplier base, businesses can mitigate these risks.
If one supplier cannot fulfill their obligations, the company can rely on alternative suppliers to continue operations without significant delays or disruptions.
Innovation and Flexibility
A diverse supplier base encourages innovation.
Suppliers are more likely to introduce new technologies or materials to gain a competitive edge.
Companies can benefit from these innovations by having access to the latest advancements in the industry, further enhancing their offerings.
Moreover, multi-supplier procurement provides greater flexibility.
Companies can scale production up or down based on demand fluctuations without relying heavily on a single supplier’s capabilities.
Strategic Relationships
Building strategic relationships with multiple suppliers can lead to long-term collaboration and trust.
This can result in better terms, access to exclusive deals, and customized solutions tailored to the company’s specific needs.
Strong relationships with suppliers can also foster better communication and cooperation, leading to smoother operations and a more efficient supply chain.
Challenges and Considerations
While multi-supplier procurement offers numerous benefits, it does come with challenges that businesses must consider.
Coordination Complexity
Managing multiple suppliers can be complex and time-consuming.
Companies need to ensure effective communication and coordination among suppliers to avoid confusion or overlap in responsibilities.
This requires robust systems and processes to manage supplier relationships and performance efficiently.
Quality Control
With various suppliers involved, maintaining consistent quality across the board can be challenging.
Businesses must implement rigorous quality control measures, such as regular audits, inspections, and performance reviews to ensure all suppliers meet the required standards.
Supplier Relationships
Balancing relationships with multiple suppliers can be tricky.
Companies must ensure fair competition among suppliers while avoiding favoritism or discrimination.
Maintaining an open and transparent relationship with all suppliers is crucial to fostering trust and collaboration.
Conclusion
Multi-supplier procurement is a powerful strategy that businesses can use to achieve a balance between quality and cost.
By engaging multiple suppliers, companies can leverage competition, ensure supply chain continuity, and foster innovation.
While there are challenges to consider, the benefits of risk mitigation, strategic relationships, and enhanced flexibility make it a worthwhile approach for businesses looking to excel in today’s competitive market.
By carefully implementing and managing multi-supplier procurement, companies can thrive and achieve their operational goals more efficiently.
資料ダウンロード
QCD調達購買管理クラウド「newji」は、調達購買部門で必要なQCD管理全てを備えた、現場特化型兼クラウド型の今世紀最高の購買管理システムとなります。
ユーザー登録
調達購買業務の効率化だけでなく、システムを導入することで、コスト削減や製品・資材のステータス可視化のほか、属人化していた購買情報の共有化による内部不正防止や統制にも役立ちます。
NEWJI DX
製造業に特化したデジタルトランスフォーメーション(DX)の実現を目指す請負開発型のコンサルティングサービスです。AI、iPaaS、および先端の技術を駆使して、製造プロセスの効率化、業務効率化、チームワーク強化、コスト削減、品質向上を実現します。このサービスは、製造業の課題を深く理解し、それに対する最適なデジタルソリューションを提供することで、企業が持続的な成長とイノベーションを達成できるようサポートします。
オンライン講座
製造業、主に購買・調達部門にお勤めの方々に向けた情報を配信しております。
新任の方やベテランの方、管理職を対象とした幅広いコンテンツをご用意しております。
お問い合わせ
コストダウンが利益に直結する術だと理解していても、なかなか前に進めることができない状況。そんな時は、newjiのコストダウン自動化機能で大きく利益貢献しよう!
(Β版非公開)