- お役立ち記事
- Collection of best practices for purchasing departments to reduce material supply risks
Collection of best practices for purchasing departments to reduce material supply risks
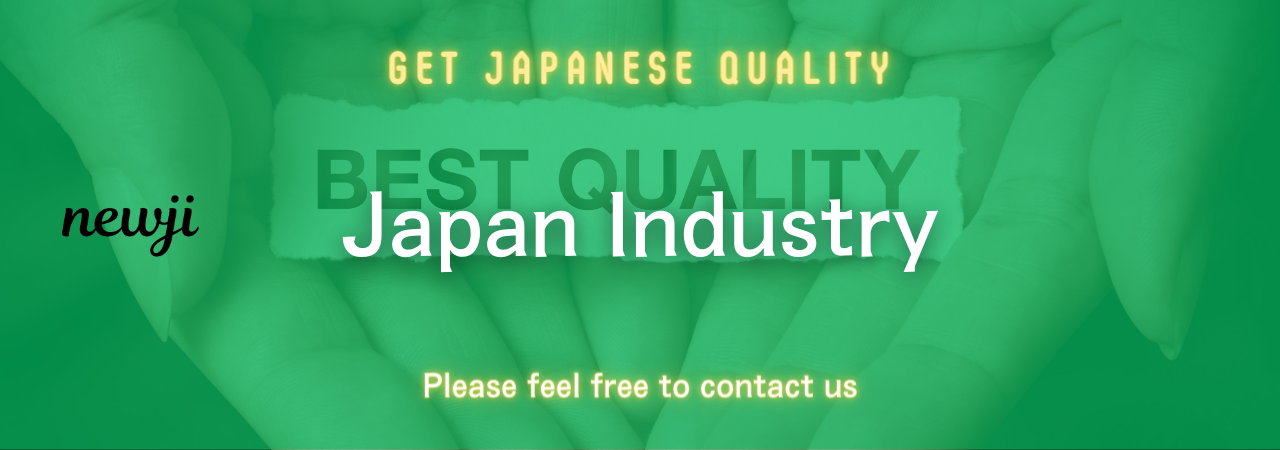
目次
Understanding Material Supply Risks
When it comes to purchasing departments, managing material supply risks is of utmost importance for seamless operations.
Material supply risks refer to the potential disruptions that can affect the availability and timely delivery of materials needed for production.
These risks can arise from various factors, including global economic shifts, natural disasters, geopolitical instability, and supplier inconsistencies.
To minimize these risks, purchasing departments must adopt comprehensive strategies that ensure the stability and reliability of their supply chains.
Understanding these risks is the first step toward effectively mitigating their impact.
Diversifying Suppliers
One of the best practices in reducing material supply risks is diversifying suppliers.
Relying on a single supplier can lead to significant vulnerabilities if that supplier encounters difficulties.
By expanding the network of suppliers, companies can diminish the impact of regional disruptions or issues specific to a single supplier.
It’s advisable to establish relationships with multiple suppliers from different geographic regions.
This diversification strategy allows purchasing departments to have backup options and maintain supply continuity even if one supplier is unable to deliver.
Conducting Supplier Assessments
Before engaging with new suppliers, conducting thorough assessments is crucial.
These assessments should include evaluating the supplier’s financial stability, production capabilities, quality standards, and adherence to delivery timelines.
Visiting supplier facilities and understanding their operations in detail can provide insights into their capabilities and reliability.
Additionally, it’s beneficial to monitor suppliers continuously and reassess them periodically to ensure they maintain their level of service.
Building Strategic Partnerships
Establishing strategic partnerships with key suppliers can significantly reduce material supply risks.
These partnerships are more than just transactional relationships.
They involve collaboration and deeper integration between companies and their suppliers.
By working closely with suppliers, purchasing departments can foster mutual trust and understanding.
This close relationship encourages suppliers to prioritize the company and provide a more reliable source of materials.
Moreover, strategic partnerships often involve collaborative planning and forecasting, which allows suppliers to better anticipate the company’s needs and prepare accordingly.
Implementing Contractual Safeguards
Contractual agreements should include safeguards that protect against material supply risks.
These contracts may include clauses for penalties or compensation in case of delivery failures or delays.
Furthermore, incorporating terms that allow flexibility can be beneficial.
For instance, agreed-upon lead times, minimum order quantities, and buffer stock obligations can serve as contingencies in unexpected situations.
Contracts should be revisited regularly to ensure they align with current market conditions and the company’s risk tolerance.
Investing in Technology
Technological advancements play a vital role in managing material supply risks.
By leveraging technology, purchasing departments can gain visibility across their supply chains and make data-driven decisions.
Implementing supply chain management software can help track orders, monitor supplier performance, and anticipate potential disruptions.
Advanced analytics and forecasting tools can also predict future material demand, allowing purchasing departments to plan more effectively.
Additionally, using technology to automate and streamline procurement processes reduces manual errors and enhances efficiency.
Embracing Risk Management Frameworks
A structured risk management framework is an essential component in reducing material supply risks.
Such frameworks involve identifying potential risks, assessing their impact, and developing mitigation strategies.
Regular risk assessments help in understanding the dynamic nature of supply chain risks and prompt necessary modifications in supply chain strategies.
Risk management frameworks also often encourage creating a risk-aware culture within the organization, where continuous monitoring and proactive measures are prioritized.
Establishing Open Communication Channels
Effective communication is fundamental in reducing material supply risks.
Open channels of communication between purchasing departments and suppliers can help address issues promptly and effectively.
Purchasing departments should foster a culture of open dialogue and ensure suppliers are comfortable sharing information about potential challenges or changes in the market.
Transparency in communication enables both parties to collaborate effectively and find solutions to avoid disruptions.
Regular meetings, updates, and feedback sessions can strengthen the relationship and reduce uncertainty in the supply chain.
Developing Contingency Plans
Having contingency plans in place is a vital practice for managing material supply risks.
Contingency plans are predetermined strategies that kick into action when an unforeseen supply chain disruption occurs.
These plans should identify alternative suppliers, transportation routes, and methods to quickly adjust to changes.
Regularly testing and refining these plans through simulation exercises can ensure their effectiveness when needed.
By preparing for potential disruptions, purchasing departments can mitigate risks and ensure continuous supply chain operations.
Maintaining Adequate Inventory Levels
Balancing inventory levels is a critical aspect of risk management.
While excessive inventory can increase holding costs, inadequate inventory heightens the possibility of production halts due to supply disruptions.
Purchasing departments should strive to maintain optimal inventory levels that provide a buffer against supply chain disturbances without incurring unnecessary costs.
Using inventory management tools and just-in-time principles can assist in optimizing inventory levels efficiently.
Keeping Up with Market Trends
Staying informed about market trends and emerging risks is crucial for purchasing departments.
Regularly reviewing market reports, attending industry seminars, and engaging with experts can provide insights into potential supply chain challenges.
Understanding trends such as shifting trade policies, innovations in production processes, and fluctuations in material prices can equip purchasing departments with the knowledge to proactively address material supply risks.
By employing these best practices, purchasing departments can effectively reduce material supply risks and ensure the stability and resilience of their supply chains.
Through careful planning, strategic partnerships, and the utilization of technology, organizations can safeguard their operations and navigate an ever-evolving market landscape with confidence.
資料ダウンロード
QCD調達購買管理クラウド「newji」は、調達購買部門で必要なQCD管理全てを備えた、現場特化型兼クラウド型の今世紀最高の購買管理システムとなります。
ユーザー登録
調達購買業務の効率化だけでなく、システムを導入することで、コスト削減や製品・資材のステータス可視化のほか、属人化していた購買情報の共有化による内部不正防止や統制にも役立ちます。
NEWJI DX
製造業に特化したデジタルトランスフォーメーション(DX)の実現を目指す請負開発型のコンサルティングサービスです。AI、iPaaS、および先端の技術を駆使して、製造プロセスの効率化、業務効率化、チームワーク強化、コスト削減、品質向上を実現します。このサービスは、製造業の課題を深く理解し、それに対する最適なデジタルソリューションを提供することで、企業が持続的な成長とイノベーションを達成できるようサポートします。
オンライン講座
製造業、主に購買・調達部門にお勤めの方々に向けた情報を配信しております。
新任の方やベテランの方、管理職を対象とした幅広いコンテンツをご用意しております。
お問い合わせ
コストダウンが利益に直結する術だと理解していても、なかなか前に進めることができない状況。そんな時は、newjiのコストダウン自動化機能で大きく利益貢献しよう!
(Β版非公開)