- お役立ち記事
- Tips for purchasing planning and inventory management to shorten lead times
Tips for purchasing planning and inventory management to shorten lead times
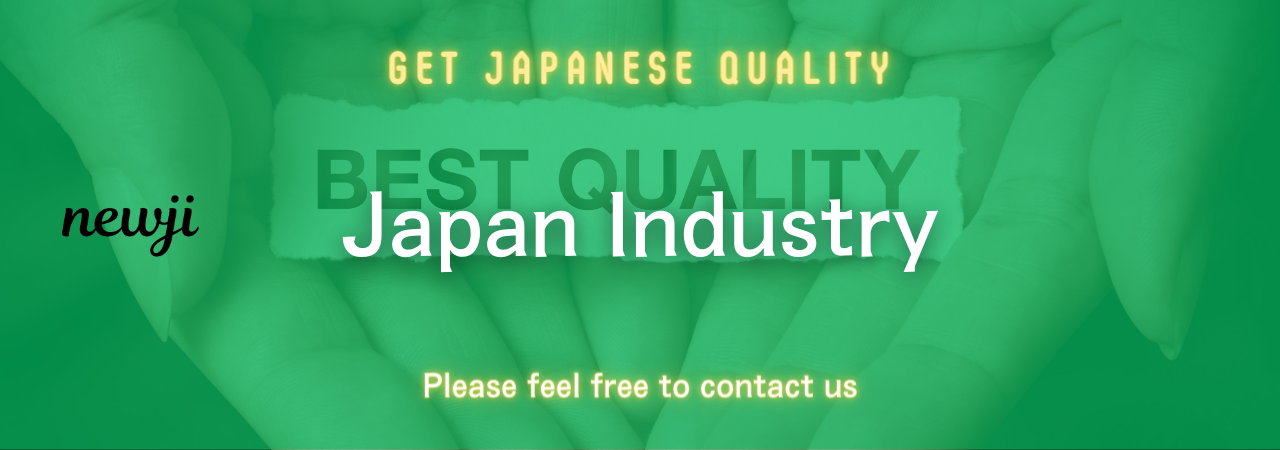
目次
Understanding Lead Times
Before diving deep into strategies for purchasing planning and inventory management, it’s essential to understand what lead times mean.
Lead time is the amount of time it takes from placing an order until the goods are received and ready for sale or use.
This period encompasses all stages in the supply chain, including processing, manufacturing, transportation, and delivery.
Why Lead Times Matter
Shorter lead times can significantly benefit businesses.
They allow for faster response to market trends, reduce holding costs, and improve customer satisfaction.
Understanding and managing lead times can provide a competitive edge.
Effective Purchasing Planning
Proper purchasing planning is crucial in shortening lead times.
It involves forecasting demand, selecting suppliers, and placing orders strategically.
Forecasting Demand
One of the first steps in purchasing planning is accurately forecasting demand.
This helps in avoiding understocking or overstocking.
Utilize historical data, market trends, and customer feedback to predict future demand.
Advanced tools and software can also aid in creating more precise forecasts.
Supplier Selection
Choosing the right suppliers is crucial.
Look for suppliers who are reliable, have a good track record, and can deliver quickly.
Establishing a strong relationship with suppliers can lead to better communication and more favorable terms.
Some businesses opt for multiple suppliers to mitigate risks and reduce lead times.
Strategic Ordering
Once you understand your demand and have chosen your suppliers, place orders strategically.
Consider ordering in larger quantities to benefit from economies of scale, but balance it with storage capabilities and cash flow.
Utilize just-in-time (JIT) ordering to minimize inventory levels and reduce holding costs.
Optimizing Inventory Management
Inventory management is the other side of the coin when it comes to shortening lead times.
Efficient inventory management ensures that products are in stock when needed, without overstocking.
Inventory Control Systems
Investing in an effective inventory control system can drastically improve lead times.
These systems track inventory in real-time, alerting you to low stock levels or slow-moving items.
This information helps in making informed decisions about reordering and stocking.
ABC Analysis
ABC analysis is a method of categorizing inventory based on priority—’A’ items being the most crucial, ‘B’ of moderate importance, and ‘C’ the least.
Focus more on managing ‘A’ items, ensuring they are always readily available, as they usually account for the majority of sales and profitability.
Lean Inventory Practices
Adopting lean inventory practices can contribute to reduced lead times.
This involves minimizing wastage, optimizing stock levels, and improving flow efficiency within the warehouse.
Regularly assess and tweak processes to ensure optimal performance.
Utilizing Technology
Technology plays a pivotal role in enhancing both purchasing planning and inventory management.
Automated Solutions
Integrate automated solutions into your operations.
Automation in ordering, tracking, and inventory management reduces manual errors and speeds up the entire process.
Cloud-based systems also allow for collaboration and efficient communication between all parties involved.
Data Analysis
Use data analysis tools to gain insights into your purchasing and inventory practices.
Analyzing trends and data patterns can unveil areas for improvement and innovation.
Predictive analytics can help in foreseeing demand changes and adjusting strategies in advance.
Building Strong Supplier Relationships
Healthy relationships with suppliers can add immense value to your supply chain.
Communication and Collaboration
Foster open and honest communication channels with your suppliers.
Collaboration enhances understanding of both parties’ needs and constraints, leading to more flexible and efficient processes.
Consider involving suppliers in your planning stages to achieve synchronized operations.
Long-Term Partnerships
Aim to build long-term partnerships rather than searching for new suppliers frequently.
Long-term relationships often lead to better terms, priority service, and cost savings in the long run.
Monitoring and Continuous Improvement
Finally, always monitor your purchasing and inventory practices.
Regular Audits
Perform regular audits of your processes, systems, and supplier performance.
Audits help identify inefficiencies, bottlenecks, and potential improvements.
Use findings to streamline processes and reduce lead times.
Feedback Mechanisms
Establish feedback mechanisms that involve your team, suppliers, and customers.
Feedback can provide invaluable insights into areas of improvement or change.
Be open to adopting new methods or technologies that enhance efficiency.
Continuous improvement is not a one-time task but an ongoing effort to optimize and reduce lead times consistently.
By combining effective purchasing planning, efficient inventory management, strong supplier relationships, and the right technology, businesses can significantly shorten lead times.
Enhanced lead time management leads to better customer satisfaction, reduced costs, and sustainable growth.
資料ダウンロード
QCD調達購買管理クラウド「newji」は、調達購買部門で必要なQCD管理全てを備えた、現場特化型兼クラウド型の今世紀最高の購買管理システムとなります。
ユーザー登録
調達購買業務の効率化だけでなく、システムを導入することで、コスト削減や製品・資材のステータス可視化のほか、属人化していた購買情報の共有化による内部不正防止や統制にも役立ちます。
NEWJI DX
製造業に特化したデジタルトランスフォーメーション(DX)の実現を目指す請負開発型のコンサルティングサービスです。AI、iPaaS、および先端の技術を駆使して、製造プロセスの効率化、業務効率化、チームワーク強化、コスト削減、品質向上を実現します。このサービスは、製造業の課題を深く理解し、それに対する最適なデジタルソリューションを提供することで、企業が持続的な成長とイノベーションを達成できるようサポートします。
オンライン講座
製造業、主に購買・調達部門にお勤めの方々に向けた情報を配信しております。
新任の方やベテランの方、管理職を対象とした幅広いコンテンツをご用意しております。
お問い合わせ
コストダウンが利益に直結する術だと理解していても、なかなか前に進めることができない状況。そんな時は、newjiのコストダウン自動化機能で大きく利益貢献しよう!
(Β版非公開)