- お役立ち記事
- A must-read for purchasing departments! What is the key to reducing maintenance costs for automated machinery?
A must-read for purchasing departments! What is the key to reducing maintenance costs for automated machinery?
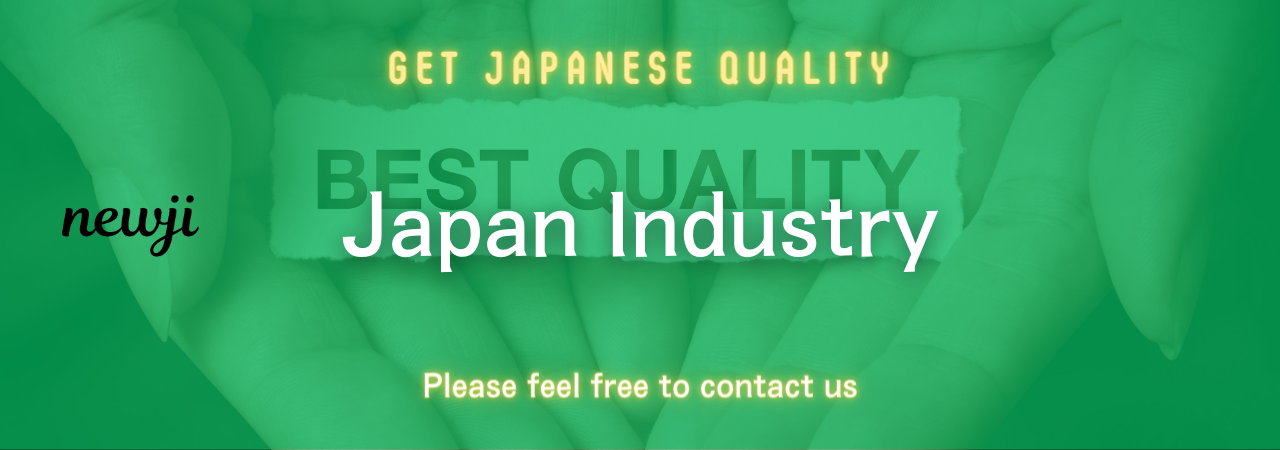
When it comes to maintaining automated machinery, reducing maintenance costs is a significant concern for purchasing departments.
Automated machinery, while incredibly beneficial in improving efficiency and productivity, can also incur high maintenance expenses if not managed properly.
In this article, we will explore key strategies to help reduce these costs effectively, ensuring your department can maximize the benefits of automated technology without overwhelming financial burdens.
目次
Understanding the Importance of Maintenance
Before diving into cost-reduction strategies, it’s crucial to understand why maintenance is important for automated machinery.
Proper maintenance ensures machines operate at optimal performance levels, minimizes downtime, and extends the lifespan of your equipment.
This not only enhances productivity but also ensures a safe working environment.
Machines that are not well-maintained can lead to frequent breakdowns and may result in costly repairs or replacements.
Regular upkeep helps prevent these issues, providing a more reliable and efficient production process.
Regular Preventive Maintenance
One of the most effective ways to reduce maintenance costs is through regular preventive maintenance.
This involves scheduling routine inspections and servicing of machinery to identify potential issues before they become major problems.
Preventive maintenance can include activities such as lubrication, adjustments, and replacing worn-out parts.
By addressing minor issues early, you can avoid costly repairs and extended downtime.
Moreover, implementing a preventive maintenance schedule increases the overall lifespan of machinery, reducing the frequency with which equipment needs to be replaced.
Investment in training staff to perform routine checks can further enhance this process.
Using Technology for Monitoring
Leveraging technology plays a significant role in cutting maintenance costs for automated machinery.
Implementing advanced monitoring systems allows your team to track the performance and health of your machinery in real-time.
Condition monitoring systems can easily diagnose issues through sensors and software analytics, allowing for adjustments without causing disruptions.
Predictive maintenance, guided by data analytics, enables you to predict failures before they happen, letting you schedule maintenance accordingly, avoiding unexpected costs.
Keeping Detailed Maintenance Records
Keeping comprehensive and organized maintenance records is another crucial aspect of reducing maintenance costs.
Documentation of all service activities, repairs, and part replacements should be maintained meticulously.
These records help track the history of each machine, allowing you to identify patterns or recurring issues.
They aid in making informed decisions regarding future repairs and replacements.
Extensive maintenance records act as a knowledge base that can guide new team members in understanding past challenges and solutions.
Selecting the Right Machinery
Selecting the right machinery that complements your business needs can significantly influence maintenance costs.
During procurement, purchasing departments should consider the quality and reliability of equipment rather than just the price.
Lower initial costs may tempt you initially, but opting for machines with good performance records and available service support reduces long-term expenses.
Consult manufacturer reviews, opt for brands with excellent after-sales services, and ensure that parts are easily available.
Engaging Compliance and Regular Training
Compliance with manufacturer guidelines and engaging in regular staff training also goes a long way in minimizing maintenance expenses.
Following proper operating procedures ensures that the machinery performs efficiently without undue wear and tear.
Regular technical training for operators will equip them with the knowledge and skills needed to handle the machinery properly.
Educated staff can identify anomalies quickly and ensure that preventive measures are implemented swiftly.
Investing in Quality Spare Parts
While it might be tempting to purchase less expensive spare parts to save on costs, investing in high-quality parts can save your department more in the long run.
Cheap parts may fail prematurely, leading to repeated investments.
High-quality parts, though more expensive initially, last longer, provide better performance, and reduce the frequency of replacements.
Establish strong relationships with reliable suppliers to ensure you are getting quality parts at competitive prices.
Considering Total Cost of Ownership (TCO)
When acquiring new machinery, evaluating the total cost of ownership (TCO) is crucial.
The TCO encompasses all direct and indirect costs associated with the machinery, including purchase price, operating costs, and maintenance expenses over the machine’s lifespan.
By considering the TCO, purchasing departments can make more informed decisions, selecting machinery that presents a cost-effective option without compromising quality.
Using the TCO approach ensures that the initial procurement is aligned with long-term financial and operational goals.
Encouraging Employee Involvement
Engaging employees in maintenance strategies can lead to substantial cost savings.
Encourage operators to report any signs of malfunctioning immediately to prevent the worsening of problems.
Implementing a reward or recognition system for employees who participate actively in the upkeep of machinery can foster a proactive culture within the organization.
Employees who feel valued and involved are likely to take better care of the machines they operate.
Conclusion
Reducing maintenance costs of automated machinery requires a comprehensive strategy that encompasses preventive maintenance, technology adoption, and employee engagement.
By prioritizing quality, compliance, and regular training, purchasing departments can ensure that the machinery continues to operate efficiently, providing maximum productivity and return on investment.
Consider these essential strategies to lower maintenance expenses without compromising the smooth operation of your automated machinery.
Maintain detailed records, invest in quality, and involve your team to keep your production running seamlessly.
資料ダウンロード
QCD調達購買管理クラウド「newji」は、調達購買部門で必要なQCD管理全てを備えた、現場特化型兼クラウド型の今世紀最高の購買管理システムとなります。
ユーザー登録
調達購買業務の効率化だけでなく、システムを導入することで、コスト削減や製品・資材のステータス可視化のほか、属人化していた購買情報の共有化による内部不正防止や統制にも役立ちます。
NEWJI DX
製造業に特化したデジタルトランスフォーメーション(DX)の実現を目指す請負開発型のコンサルティングサービスです。AI、iPaaS、および先端の技術を駆使して、製造プロセスの効率化、業務効率化、チームワーク強化、コスト削減、品質向上を実現します。このサービスは、製造業の課題を深く理解し、それに対する最適なデジタルソリューションを提供することで、企業が持続的な成長とイノベーションを達成できるようサポートします。
オンライン講座
製造業、主に購買・調達部門にお勤めの方々に向けた情報を配信しております。
新任の方やベテランの方、管理職を対象とした幅広いコンテンツをご用意しております。
お問い合わせ
コストダウンが利益に直結する術だと理解していても、なかなか前に進めることができない状況。そんな時は、newjiのコストダウン自動化機能で大きく利益貢献しよう!
(Β版非公開)