- お役立ち記事
- Inventory management method for multiple locations to achieve stable supply throughout the supply chain
Inventory management method for multiple locations to achieve stable supply throughout the supply chain
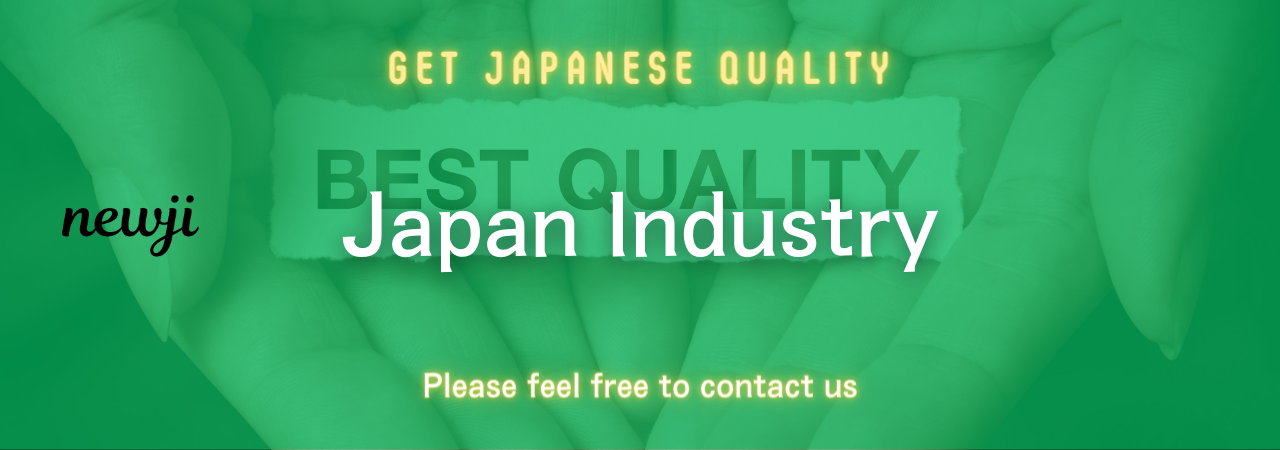
目次
Understanding the Basics of Inventory Management
Inventory management is a crucial aspect of any business that deals with the storage and movement of goods.
It involves overseeing the inflow and outflow of products, ensuring that there is always a balance between supply and demand.
Effective inventory management ensures that a company can maintain smooth operations and provide stable services throughout the entire supply chain.
When dealing with multiple locations, managing inventory can be more complex but no less essential.
The Challenges of Managing Inventory Across Multiple Locations
When businesses expand, they often spread their operations across multiple geographic locations to be closer to their customers or to enter new markets.
While this expansion can lead to increased revenues and market presence, it also presents unique challenges in inventory management.
The complexities include dealing with varying demand cycles, managing transportation logistics, and maintaining enough stock to prevent shortages without overstocking.
Each location might experience different customer demands influenced by local trends or seasons.
A one-size-fits-all approach in such scenarios might lead to inefficiency and wastage.
For instance, retaining excess inventory in a low-demand area could lead to increased storage costs and reduced cash flow.
Importance of Technology in Modern Inventory Management
Technology plays a pivotal role in overcoming the challenges of inventory management across multiple locations.
By utilizing advanced software and tools, businesses can track inventory in real-time, make data-informed decisions, and streamline operations.
Inventory management systems (IMS) provide managers with insights into stock levels, sales patterns, and supplier performance at each location.
With the help of cloud-based solutions, inventory data can be centralized, allowing seamless access and updates from any location.
This kind of technology ensures accuracy and efficiency, preventing errors that are often caused by manual tracking systems.
Key Strategies for Effective Multi-location Inventory Management
1. Accurate Demand Forecasting
One of the most critical aspects of inventory management is forecasting demand with precision.
For businesses operating in multiple locations, understanding and predicting local demand is pivotal.
Demand forecasting involves analyzing historical sales data, market trends, and considering factors such as seasonal shifts and economic conditions.
Using this information, businesses can plan inventory levels that meet the needs of each specific location.
2. Centralized Inventory Data
Centralizing inventory data helps maintain consistent information about stock levels across all locations.
A central system provides an integrated view of the inventory, making it easier to manage supplies and optimize stock levels.
When data is centralized, it simplifies tracking and audits, reduces discrepancies, and allows quick adjustments based on real-time data.
3. Balancing Inventory Levels
It is crucial to maintain an optimal balance of inventory across all locations.
Excessive inventory ties up capital and increases storage costs, while inadequate inventory can lead to stockouts and lost sales.
Using techniques such as just-in-time inventory or minimum inventory levels can ensure that all locations have what they need without overdoing it.
4. Efficient Distribution Systems
An efficient distribution system is vital for maintaining the flow of inventory between locations.
This includes optimizing transportation routes, scheduling regular re-stocking, and employing reliable logistics partners.
Advanced routing software can help minimize transportation costs and time by selecting the best routes and schedules based on various factors including weather and traffic patterns.
5. Regular Performance Evaluation
Regular evaluation of inventory management performance is necessary for identifying areas of improvement.
Key performance metrics may include inventory turnover ratio, carrying costs, backorder rate, and service levels.
By analyzing these metrics, managers can pinpoint inefficiencies and implement corrective measures promptly.
Benefits of Effective Multi-location Inventory Management
1. Stable Supply Chain Operations
By managing inventory efficiently across multiple locations, businesses can avoid disruptions that lead to supply chain instability.
This ensures that products are available when and where needed, leading to higher customer satisfaction.
2. Cost Savings
Proper inventory management minimizes excess inventory and reduces storage costs.
It also accounts for efficient use of transportation resources, which can significantly cut down logistics expenses.
3. Enhanced Customer Satisfaction
Customers expect timely delivery of their purchases.
Effective inventory management ensures that customer orders are fulfilled quickly and accurately, leading to a better buying experience and increased loyalty.
4. Increased Competitive Advantage
Businesses that manage their inventory effectively are better positioned to react to market changes.
They can respond quickly to demand fluctuations, launch new products successfully, and enter new markets with confidence.
Conclusion
Effective inventory management across multiple locations is essential for maintaining a smooth and stable supply chain.
By leveraging technology, accurate forecasting, centralization of data, and efficient distribution systems, businesses can overcome the challenges associated with multi-location operations.
These strategies not only prevent inefficiencies and high costs but also enhance customer satisfaction and market competitiveness.
In the ever-evolving landscape of business, effective inventory management not only supports operational stability but also paves the way for growth and success.
資料ダウンロード
QCD調達購買管理クラウド「newji」は、調達購買部門で必要なQCD管理全てを備えた、現場特化型兼クラウド型の今世紀最高の購買管理システムとなります。
ユーザー登録
調達購買業務の効率化だけでなく、システムを導入することで、コスト削減や製品・資材のステータス可視化のほか、属人化していた購買情報の共有化による内部不正防止や統制にも役立ちます。
NEWJI DX
製造業に特化したデジタルトランスフォーメーション(DX)の実現を目指す請負開発型のコンサルティングサービスです。AI、iPaaS、および先端の技術を駆使して、製造プロセスの効率化、業務効率化、チームワーク強化、コスト削減、品質向上を実現します。このサービスは、製造業の課題を深く理解し、それに対する最適なデジタルソリューションを提供することで、企業が持続的な成長とイノベーションを達成できるようサポートします。
オンライン講座
製造業、主に購買・調達部門にお勤めの方々に向けた情報を配信しております。
新任の方やベテランの方、管理職を対象とした幅広いコンテンツをご用意しております。
お問い合わせ
コストダウンが利益に直結する術だと理解していても、なかなか前に進めることができない状況。そんな時は、newjiのコストダウン自動化機能で大きく利益貢献しよう!
(Β版非公開)