- お役立ち記事
- How to check overseas suppliers’ compliance with quality standards Steps to be taken by the purchasing department
How to check overseas suppliers’ compliance with quality standards Steps to be taken by the purchasing department
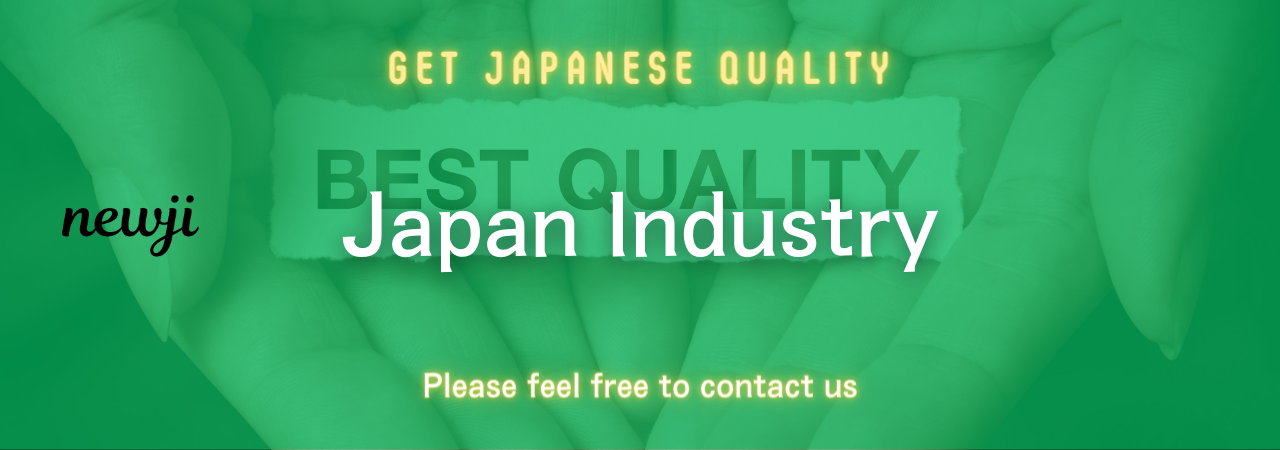
目次
Understanding the Importance of Quality Compliance
In today’s globalized market, businesses increasingly rely on overseas suppliers to provide goods and materials.
While this opens up opportunities for cost savings and access to diverse products, it also introduces challenges in ensuring that these suppliers comply with quality standards.
Maintaining these standards is crucial for maintaining customer satisfaction and protecting a company’s reputation.
Quality compliance means that suppliers adhere to specific requirements, including product safety, performance, and reliability.
These requirements can be dictated by international standards, such as ISO, or by regulations specific to a region or industry.
Failure to comply can result in a range of negative outcomes, from returns and recalls to severe financial and legal repercussions.
Steps for Purchasing Departments to Ensure Supplier Compliance
Ensuring that overseas suppliers meet quality standards involves a series of well-structured steps.
The purchasing department plays a pivotal role in this process.
Here’s a detailed guide on how they can carry out this responsibility effectively.
1. Define Clear Quality Standards
The first step is to establish clear quality standards that suppliers must meet.
These standards should be in line with the company’s requirements and any relevant industry regulations.
Clearly define what constitutes acceptable quality and ensure that this information is communicated to all potential suppliers from the outset.
2. Conduct a Comprehensive Supplier Assessment
Before entering into a contract, conduct a thorough assessment of potential suppliers.
This involves evaluating their ability to meet your quality standards and understanding their operational processes.
Look into their track record for quality management and any certifications they may hold.
This assessment can be done through questionnaires, site visits, and reference checks from other clients.
3. Implement Quality Audits
Quality audits are a critical tool for verifying compliance.
Schedule regular audits of your suppliers’ facilities and processes.
These audits can be conducted in person or virtually, depending on circumstances and resources.
During these audits, review how suppliers maintain quality standards and how they address issues when they arise.
4. Develop a Quality Control Plan
Create a detailed quality control plan that outlines how quality will be monitored throughout the supply chain process.
This plan should specify the inspections, tests, and checkpoints necessary to ensure compliance.
It also details the responsibilities of both the purchasing department and the supplier in maintaining quality.
5. Utilize Technology and Data Analytics
Leverage technology and data analytics to enhance monitoring and compliance efforts.
Use software solutions to track product quality data in real-time.
This allows for identifying potential issues early and addressing them before they escalate.
Data-driven insights can also aid in making more informed decisions about supplier relationships and improvements.
6. Set Up a Dispute Resolution Process
Even with proactive measures in place, not all issues can be anticipated.
Establish a clear process for resolving disputes that arise from quality problems.
This should involve clear guidelines for reporting issues, a timeline for responses, and a structured approach to reaching resolutions.
Both parties need to agree on this process from the start.
7. Foster Strong Communication and Relationships
Effective communication is key to ensuring compliance.
Maintain open lines of communication with your suppliers to promptly address issues and collaborate on solutions.
Building strong relationships with suppliers can facilitate better understanding and cooperation in meeting quality standards.
Monitoring and Continuous Improvement
Ensuring supplier compliance with quality standards is not a one-off task; it requires ongoing monitoring and a commitment to continuous improvement.
For this, the purchasing department needs to establish a robust system that allows for regular reviews and updates to compliance strategies.
1. Monitor Supplier Performance
Regularly monitor your supplier’s performance against the established quality standards.
This can be done through key performance indicators (KPIs) that measure various aspects of quality, such as defect rates and delivery times.
Consistent monitoring helps in identifying trends or recurring issues that need attention.
2. Foster a Culture of Continuous Improvement
Encourage suppliers to adopt a mindset of continuous improvement.
Work with them to identify opportunities for enhancing processes and quality.
Sharing best practices and facilitating training can help suppliers elevate their quality standards, benefiting both parties.
3. Stay Updated on Industry Standards
International standards and regulations are continually evolving.
Staying informed about these changes ensures that your quality compliance measures remain relevant and effective.
Participating in industry forums and reviewing updates from standardization bodies can provide valuable insights.
4. Align Supplier Incentives with Quality Goals
Align incentives with the achievement of quality goals.
Suppliers who consistently meet or exceed your quality expectations can be offered rewards or preferred status.
This encourages them to maintain high standards and fosters a competitive environment that benefits your business.
Conclusion
Managing supplier compliance with quality standards is an ongoing process that requires diligence, clear communication, and strategic planning.
By implementing structured procedures and leveraging technology, purchasing departments can mitigate risks and ensure that products meet the required quality thresholds.
Ultimately, these efforts contribute to the success and reputation of the business, fostering customer trust and loyalty in a competitive market.
資料ダウンロード
QCD調達購買管理クラウド「newji」は、調達購買部門で必要なQCD管理全てを備えた、現場特化型兼クラウド型の今世紀最高の購買管理システムとなります。
ユーザー登録
調達購買業務の効率化だけでなく、システムを導入することで、コスト削減や製品・資材のステータス可視化のほか、属人化していた購買情報の共有化による内部不正防止や統制にも役立ちます。
NEWJI DX
製造業に特化したデジタルトランスフォーメーション(DX)の実現を目指す請負開発型のコンサルティングサービスです。AI、iPaaS、および先端の技術を駆使して、製造プロセスの効率化、業務効率化、チームワーク強化、コスト削減、品質向上を実現します。このサービスは、製造業の課題を深く理解し、それに対する最適なデジタルソリューションを提供することで、企業が持続的な成長とイノベーションを達成できるようサポートします。
オンライン講座
製造業、主に購買・調達部門にお勤めの方々に向けた情報を配信しております。
新任の方やベテランの方、管理職を対象とした幅広いコンテンツをご用意しております。
お問い合わせ
コストダウンが利益に直結する術だと理解していても、なかなか前に進めることができない状況。そんな時は、newjiのコストダウン自動化機能で大きく利益貢献しよう!
(Β版非公開)