- お役立ち記事
- Measures to strengthen the traceability of purchasing departments in the material supply chain
Measures to strengthen the traceability of purchasing departments in the material supply chain
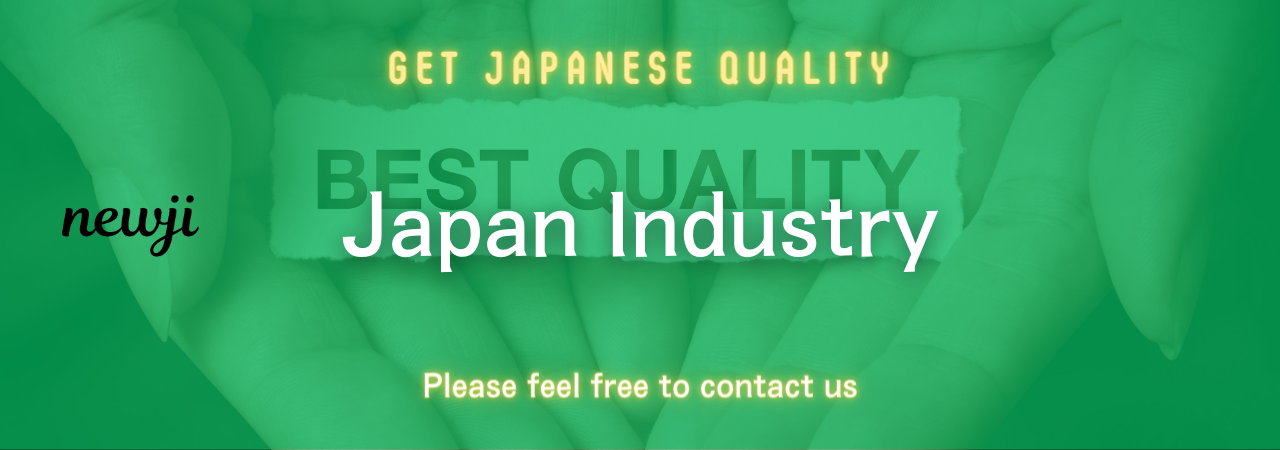
目次
Understanding Traceability in the Supply Chain
In today’s competitive business environment, traceability in the supply chain has become a critical factor for success.
Traceability refers to the ability to track the journey of materials, components, and products through various stages of production and distribution.
It ensures that each step of the process is documented and can be verified, offering transparency and accountability from raw material sourcing to the final consumer delivery.
The purchasing department, being a pivotal part of the supply chain, plays a crucial role in ensuring that traceability is maintained consistently and effectively.
The Importance of Strengthening Traceability
Strengthening traceability is important for several reasons.
First, it allows companies to guarantee the quality and authenticity of their products.
Consumers are becoming increasingly conscious of where their products come from and how they are made, compelling businesses to maintain stringent checks on their supply chains.
Second, traceability facilitates compliance with industry standards and regulatory requirements.
Many sectors, such as pharmaceuticals and food production, are subject to strict guidelines that mandate clear documentation of sourcing and production processes.
Failure to comply with these guidelines can result in penalties and damage to brand reputation.
Lastly, in the unfortunate event of a defect or recall, having a robust traceability system allows companies to quickly identify and address the problem.
This minimizes financial losses and reduces the impact on consumer confidence.
Therefore, enhancing traceability is not just about legal compliance but also about building a resilient and transparent supply chain.
Challenges in Implementing Strong Traceability
Despite its importance, implementing strong traceability in supply chains is not without challenges.
One of the primary hurdles is the complexity and scale of modern supply chains.
With products often traveling across multiple countries and involving numerous suppliers, maintaining accurate and detailed records becomes a daunting task.
Each partner in the supply chain must commit to rigorous documentation and transparency, which can be difficult to achieve in practice.
Furthermore, there is a need for advanced technology integration.
Traditional methods of record-keeping and tracking are inadequate in today’s fast-paced environment.
Adopting technologies such as RFID, blockchain, and IoT devices can significantly enhance the efficiency and accuracy of traceability systems.
However, the initial investment cost and the complexity of implementation can be barriers for many companies.
Data management is another significant challenge.
Collecting, storing, and analyzing large volumes of data requires robust IT infrastructure and skilled personnel.
Ensuring data accuracy and security is paramount, as inaccuracies can lead to incorrect decisions and potential breaches can compromise sensitive information.
Strategies for Enhancing Traceability in Purchasing Departments
To effectively address these challenges and strengthen traceability in their supply chains, purchasing departments should consider several strategies.
1. Invest in Technology
Incorporating advanced technology into the supply chain is one of the most effective ways to improve traceability.
Technologies like blockchain can provide immutable records of transactions, while the Internet of Things (IoT) devices can offer real-time data on the location and condition of goods.
These technologies can greatly enhance visibility throughout the supply chain, enabling purchasing departments to make data-driven decisions and respond quickly to any issues.
2. Foster Collaboration and Communication
Strong relationships with suppliers and other stakeholders are essential for improving traceability.
Purchasing departments should regularly communicate with their partners to ensure that everyone in the supply chain is on the same page regarding traceability requirements.
Building a culture of transparency and collaboration can encourage suppliers to adopt similar traceability practices, creating a more cohesive supply chain.
3. Standardize Processes and Documentation
Standardizing processes and documentation across the supply chain is crucial for maintaining traceability.
Creating clear guidelines and protocols for data collection can help ensure consistency and accuracy in records.
Purchasing departments should work closely with other stakeholders to develop and implement these standards, providing necessary training and support where needed.
4. Conduct Regular Audits and Reviews
Regular audits and reviews of the supply chain can help identify weaknesses in traceability and areas for improvement.
Purchasing departments should establish a routine schedule for evaluating their traceability systems and processes.
These evaluations can uncover inconsistencies or gaps in documentation that need to be addressed.
By continuously assessing their supply chains, companies can adapt to changes and stay ahead of potential issues.
Conclusion
Strengthening traceability within purchasing departments is pivotal for ensuring a transparent, efficient, and responsible supply chain.
With the growing emphasis on quality, compliance, and accountability, businesses must take proactive measures to enhance their traceability systems.
By investing in technology, fostering collaboration, standardizing processes, and conducting regular reviews, purchasing departments can create a robust traceability framework that supports their organization’s strategic objectives.
Ultimately, fortifying traceability not only meets consumer expectations but also leads to better risk management, increased credibility, and long-term success in the marketplace.
資料ダウンロード
QCD調達購買管理クラウド「newji」は、調達購買部門で必要なQCD管理全てを備えた、現場特化型兼クラウド型の今世紀最高の購買管理システムとなります。
ユーザー登録
調達購買業務の効率化だけでなく、システムを導入することで、コスト削減や製品・資材のステータス可視化のほか、属人化していた購買情報の共有化による内部不正防止や統制にも役立ちます。
NEWJI DX
製造業に特化したデジタルトランスフォーメーション(DX)の実現を目指す請負開発型のコンサルティングサービスです。AI、iPaaS、および先端の技術を駆使して、製造プロセスの効率化、業務効率化、チームワーク強化、コスト削減、品質向上を実現します。このサービスは、製造業の課題を深く理解し、それに対する最適なデジタルソリューションを提供することで、企業が持続的な成長とイノベーションを達成できるようサポートします。
オンライン講座
製造業、主に購買・調達部門にお勤めの方々に向けた情報を配信しております。
新任の方やベテランの方、管理職を対象とした幅広いコンテンツをご用意しております。
お問い合わせ
コストダウンが利益に直結する術だと理解していても、なかなか前に進めることができない状況。そんな時は、newjiのコストダウン自動化機能で大きく利益貢献しよう!
(Β版非公開)