- お役立ち記事
- Key points for reviewing supplier contracts to help purchasing departments ensure stable material supply
Key points for reviewing supplier contracts to help purchasing departments ensure stable material supply
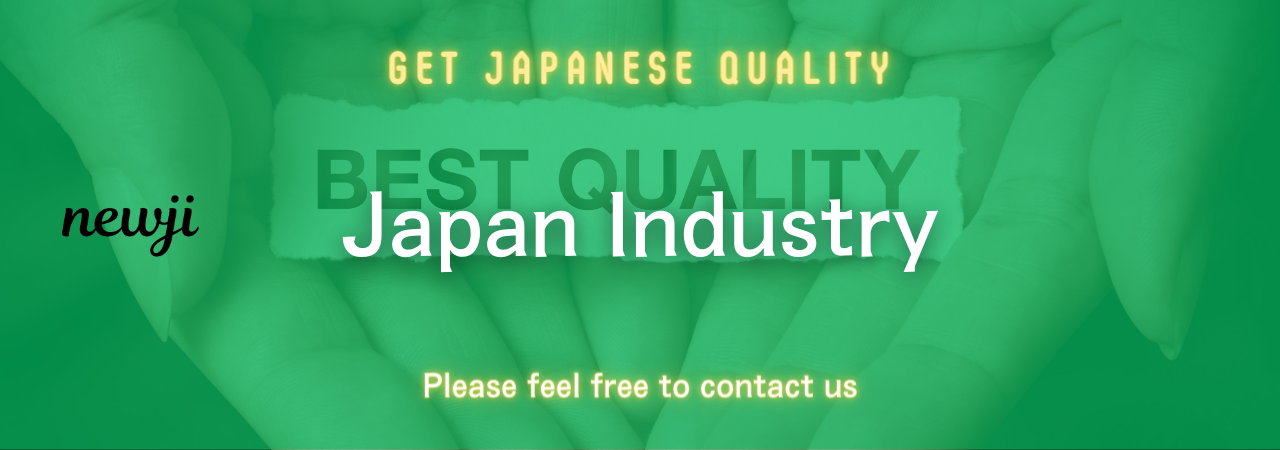
目次
Understanding the Importance of Supplier Contracts
In the world of procurement and supply chain management, supplier contracts are essential tools.
They establish the framework for the relationship between a company and its suppliers.
A well-structured contract not only ensures the delivery of quality materials but also helps maintain a stable supply chain.
For purchasing departments, reviewing supplier contracts is crucial for several reasons.
Contracts provide assurance that materials will be delivered on time and meet specified standards.
They outline the responsibilities and obligations of both parties, reducing the risk of disputes.
In the face of unforeseen disruptions, a solid contract can be a lifeline, offering solutions such as alternative supply options or financial safeguards.
Therefore, understanding and reviewing these contracts are key to achieving operational stability and success.
Key Elements to Look for in a Supplier Contract
When reviewing supplier contracts, purchasing departments should pay close attention to specific elements that can influence the reliability of material supply.
Clear Scope of Work
The contract should clearly define the scope of work, including detailed descriptions of the materials and services to be provided.
This helps to avoid misunderstandings about what is expected from the supplier.
Delivery Timelines
Timely delivery is critical.
The contract must specify delivery schedules and deadlines.
This ensures that all parties are aligned on when the materials will be delivered, thus avoiding potential disruptions in the supply chain.
Quality Standards and Specifications
Ensure that the contract includes detailed quality requirements and specifications for the materials.
This guarantees that the supplier knows exactly what is expected in terms of quality and performance.
Pricing and Payment Terms
Review the contract for clear pricing structures and payment terms.
This not only helps in budgeting but also avoids future disputes regarding costs.
Look for clauses that address price adjustments due to market changes or currency fluctuations.
Responsibilities and Liabilities
The contract should outline the responsibilities of both the supplier and the purchaser.
It should also cover liabilities in case of non-compliance or failure to deliver as agreed.
This provides a safety net for potential legal issues.
Strategies for Effective Contract Review
Purchasing departments can adopt several strategies to enhance the effectiveness of their contract review processes.
Engage Cross-Functional Teams
Involve teams from different departments, such as legal, quality assurance, and finance, in the contract review process.
Each department can provide insights and perspectives that contribute to a comprehensive review.
Use of Contract Management Software
Leverage modern technology by using contract management software.
These tools can help streamline the review process, organize documents, and ensure nothing is overlooked.
Regular Audits and Updates
Regularly audit and update supplier contracts to reflect any changes in business operations, supply chain dynamics, or regulatory requirements.
This ensures that contracts remain relevant and effective over time.
Mitigating Risks Through Contract Clauses
Supplier contracts are not just about addressing present needs; they are also tools for risk mitigation.
Including specific clauses can help protect the company from unforeseen events.
Force Majeure Clauses
These clauses address what happens in the event of unforeseen circumstances, such as natural disasters or political unrest, that prevent the supplier from fulfilling their obligations.
Alternative Supplier Provisions
Consider clauses that allow for alternative suppliers if the primary supplier faces challenges.
This flexibility can be crucial for maintaining a stable supply chain during disruptions.
Dispute Resolution Mechanisms
Incorporate mechanisms for resolving disputes, such as mediation or arbitration, to avoid lengthy and costly legal battles.
The Role of Communication in Contract Management
Effective communication between purchasing departments and suppliers is vital in the context of contract management.
Building Strong Relationships
Nurturing strong relationships with suppliers can lead to better cooperation and willingness to accommodate during challenging times.
Regular Performance Reviews
Schedule regular performance reviews with suppliers to discuss contract adherence, performance metrics, and any necessary adjustments.
This keeps both parties aligned and proactive.
Conclusion
For purchasing departments, the careful review of supplier contracts is indispensable for ensuring a stable supply of materials.
By focusing on key elements like delivery timelines, quality standards, and pricing, departments can significantly mitigate risks.
Employing strategies such as involving cross-functional teams and using technology enhances contract management efficacy.
Lastly, by maintaining open lines of communication and establishing strong supplier relationships, purchasing departments can better navigate the complexities of supply chain management.
A well-managed supplier contract is not just a document—it is a strategic asset that can make a critical difference in sustaining business operations.
資料ダウンロード
QCD調達購買管理クラウド「newji」は、調達購買部門で必要なQCD管理全てを備えた、現場特化型兼クラウド型の今世紀最高の購買管理システムとなります。
ユーザー登録
調達購買業務の効率化だけでなく、システムを導入することで、コスト削減や製品・資材のステータス可視化のほか、属人化していた購買情報の共有化による内部不正防止や統制にも役立ちます。
NEWJI DX
製造業に特化したデジタルトランスフォーメーション(DX)の実現を目指す請負開発型のコンサルティングサービスです。AI、iPaaS、および先端の技術を駆使して、製造プロセスの効率化、業務効率化、チームワーク強化、コスト削減、品質向上を実現します。このサービスは、製造業の課題を深く理解し、それに対する最適なデジタルソリューションを提供することで、企業が持続的な成長とイノベーションを達成できるようサポートします。
オンライン講座
製造業、主に購買・調達部門にお勤めの方々に向けた情報を配信しております。
新任の方やベテランの方、管理職を対象とした幅広いコンテンツをご用意しております。
お問い合わせ
コストダウンが利益に直結する術だと理解していても、なかなか前に進めることができない状況。そんな時は、newjiのコストダウン自動化機能で大きく利益貢献しよう!
(Β版非公開)