- お役立ち記事
- Purchasing risk management to strengthen the entire supply chain
Purchasing risk management to strengthen the entire supply chain
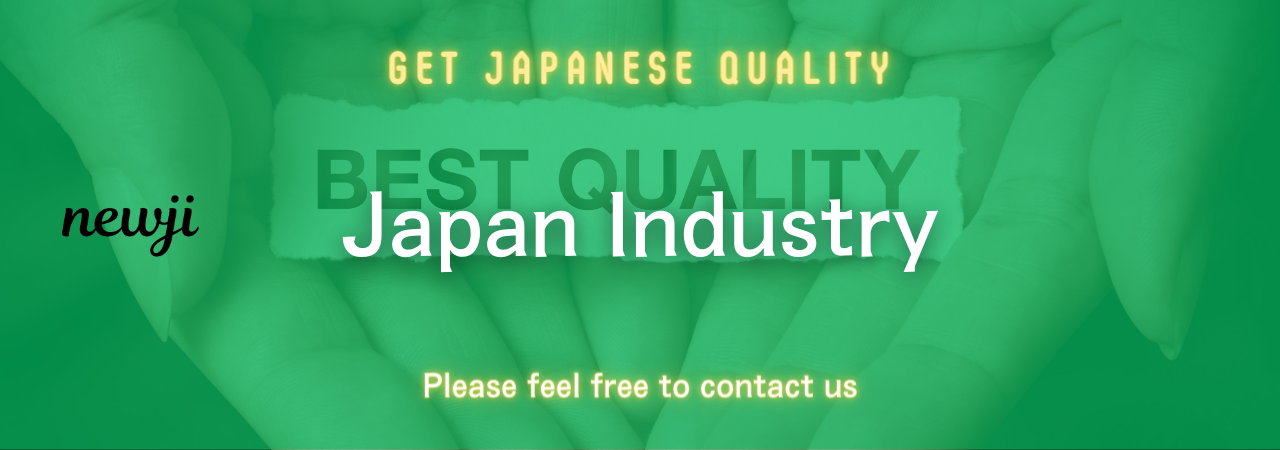
目次
Understanding Purchasing Risk Management
Purchasing risk management is a strategic approach that focuses on identifying, assessing, and mitigating risks throughout a company’s procurement process.
These risks can range from supplier failures, cost fluctuations, to global disruptions like natural disasters or political changes.
When effectively implemented, purchasing risk management strengthens the entire supply chain by ensuring that materials and services are delivered on time, within budget, and at the required level of quality.
For businesses today, understanding and managing these risks is not just beneficial – it’s essential for maintaining competitive advantage.
Why Purchasing Risk Management Matters
Purchasing risks can have significant impacts on a business’s operations and profitability.
For example, supplier bankruptcy might lead to production delays, while sudden price hikes can drastically reduce margins.
Moreover, in today’s interconnected global market, disturbances in one part of the world can have ripple effects across the entire supply chain.
By proactively managing these risks, businesses can avoid unexpected disruptions and losses.
This not only protects the bottom line but also enhances supplier relationships and improves overall supply chain resilience.
Key Risks in the Procurement Process
To effectively manage purchasing risks, it’s important to first identify the major risks involved in the procurement process.
Supplier Risk
Supplier risk involves the possibility of a supplier failing to deliver the expected goods or services.
This can be due to financial instability, poor performance, or even fraud.
Assessing the financial health and reliability of suppliers is critical in mitigating this risk.
Market Risk
Market risk refers to the potential changes in market conditions that can affect procurement activities.
This includes price volatility, changes in demand and supply, and currency fluctuations.
Keeping a close watch on market trends can help in forecasting and planning accordingly.
Operational Risk
Operational risk pertains to the disruptions within an organization’s internal processes.
These can be due to system failures, human errors, or logistical challenges.
Streamlining operations and maintaining efficient systems are crucial to reduce this kind of risk.
External Risk
External risks, such as natural disasters, political instability, and pandemics, can have drastic impacts on supply chains.
While these are often unpredictable, having contingency plans in place can minimize their effects.
Strategies for Effective Purchasing Risk Management
Developing and implementing a comprehensive purchasing risk management strategy involves several key steps.
Risk Assessment and Analysis
The first step is to conduct a thorough risk assessment.
This involves identifying possible risks, analyzing their potential impact, and prioritizing them based on their likelihood and severity.
Tools such as SWOT analysis (strengths, weaknesses, opportunities, threats) or risk matrices can be used for this assessment.
Supplier Evaluation and Diversification
Regular evaluation of suppliers is vital.
This includes assessing their financial stability, performance history, and ability to meet contract requirements.
Having a diversified supplier base can also reduce dependency on a single source, thereby mitigating risks.
Contract Management
Effective contract management involves ensuring that all agreements protect against major risks.
This might include clauses for price escalation, penalties for non-performance, and detailed terms regarding delivery timelines and quality standards.
Technology and Data Utilization
Leveraging technology can enhance purchasing risk management.
Data analytics tools provide insights into market trends and supplier performance, enabling more informed decision-making.
Additionally, digital platforms can streamline procurement processes and improve communication with suppliers.
Building Collaborative Relationships
Fostering strong relationships with suppliers can lead to improved trust and communication, which is crucial during times of uncertainty.
Collaboration can result in better problem-solving and innovation, enhancing the overall robustness of the supply chain.
The Role of Risk Management in Strengthening Supply Chains
Effective purchasing risk management doesn’t just protect a company from immediate threats; it also contributes to long-term supply chain strength.
By anticipating and addressing potential disruptions, companies can maintain operational continuity, ensuring that customer needs are met without interruption.
Furthermore, a resilient supply chain is better positioned to adapt to market changes.
This agility can be a significant competitive advantage in a rapidly changing business environment.
Continual Improvement and Adaptation
Risk management is not a one-time task but an ongoing process.
As markets and technologies evolve, so too should a company’s risk management strategies.
Continuous monitoring, review, and adaptation are necessary to stay ahead of new risks and opportunities.
Regular training for procurement teams on the latest risk management practices can also help keep everyone aligned and prepared.
Conclusion
Purchasing risk management is an integral part of supply chain strategy that cannot be overlooked.
By effectively identifying, assessing, and mitigating risks, businesses can enhance their resilience, ensure operational efficiency, and maintain competitive edge.
Fostering strong supplier relationships, leveraging technology, and staying adaptable are all crucial elements of a robust purchasing risk management approach.
In the complex and ever-evolving landscape of modern business, taking proactive steps to manage procurement risks is essential for sustaining success and growth.
資料ダウンロード
QCD調達購買管理クラウド「newji」は、調達購買部門で必要なQCD管理全てを備えた、現場特化型兼クラウド型の今世紀最高の購買管理システムとなります。
ユーザー登録
調達購買業務の効率化だけでなく、システムを導入することで、コスト削減や製品・資材のステータス可視化のほか、属人化していた購買情報の共有化による内部不正防止や統制にも役立ちます。
NEWJI DX
製造業に特化したデジタルトランスフォーメーション(DX)の実現を目指す請負開発型のコンサルティングサービスです。AI、iPaaS、および先端の技術を駆使して、製造プロセスの効率化、業務効率化、チームワーク強化、コスト削減、品質向上を実現します。このサービスは、製造業の課題を深く理解し、それに対する最適なデジタルソリューションを提供することで、企業が持続的な成長とイノベーションを達成できるようサポートします。
オンライン講座
製造業、主に購買・調達部門にお勤めの方々に向けた情報を配信しております。
新任の方やベテランの方、管理職を対象とした幅広いコンテンツをご用意しております。
お問い合わせ
コストダウンが利益に直結する術だと理解していても、なかなか前に進めることができない状況。そんな時は、newjiのコストダウン自動化機能で大きく利益貢献しよう!
(Β版非公開)