- お役立ち記事
- Purchasing department risk management model to deal with material supply risks
Purchasing department risk management model to deal with material supply risks
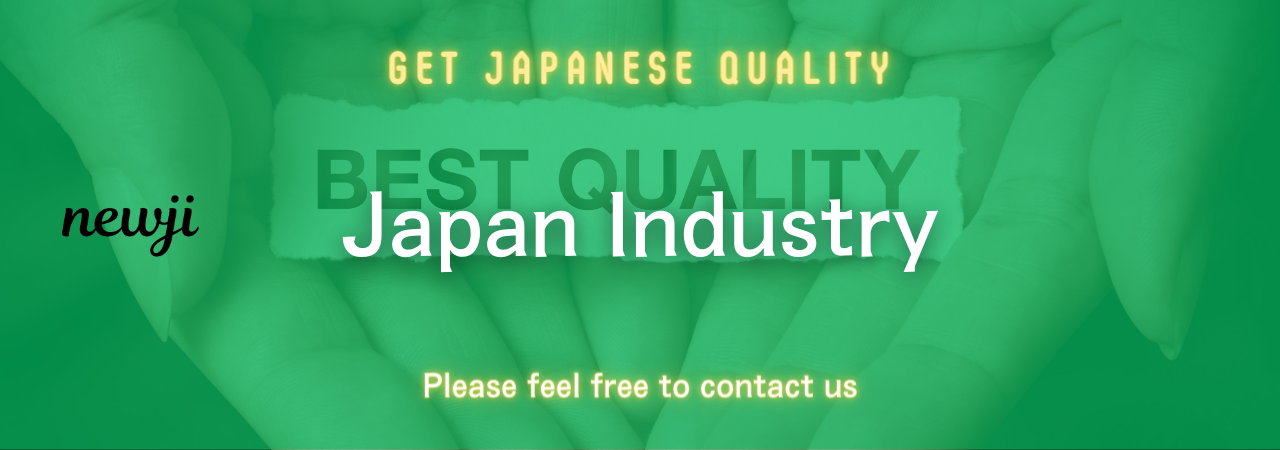
目次
Understanding Material Supply Risks
In today’s global market, managing risks related to material supply is crucial for the smooth operation of any purchasing department.
Material supply risks refer to potential disruptions or challenges in the supply chain that can affect the availability and quality of materials needed by an organization.
These risks can stem from various sources such as supplier reliability, geopolitical issues, natural disasters, and market fluctuations.
A robust risk management model can help organizations anticipate, address, and mitigate these risks, ensuring that the supply chain remains resilient and efficient.
Having a comprehensive understanding of material supply risks is the first step towards developing a risk management model.
Types of Material Supply Risks
There are several types of risks that purchasing departments need to be mindful of when dealing with material supply:
1. Supplier Risks: These arise from issues related to the capability and reliability of suppliers. A supplier may face financial instability, quality control problems, or logistical challenges, impacting their ability to deliver materials on time and as per required standards.
2. Geopolitical Risks: Political instability, trade restrictions, and regulatory changes in a supplier’s country can disrupt the supply of materials. These risks are beyond the control of organizations, making them particularly challenging to predict and manage.
3. Environmental Risks: Natural disasters such as earthquakes, floods, or hurricanes can severely impact the supply chain. These events can damage production facilities, disrupt transportation networks, and lead to significant delays in material availability.
4. Market Risks: Fluctuations in prices of raw materials, demand-supply imbalances, and changes in consumer preferences can lead to uncertainty in material availability. This risk often requires constant monitoring of market trends and conditions.
Building a Risk Management Model
Creating an effective risk management model involves several key steps, all designed to identify, assess, and mitigate potential supply chain risks.
Let’s explore these steps in detail.
Risk Identification
The first step in building a risk management model is to identify potential risks.
Organizations should conduct a comprehensive assessment of the entire supply chain to pinpoint vulnerabilities that could lead to supply disruptions.
This can be achieved through:
– **Supplier Audits:** Regular audits and evaluations of suppliers to assess their financial health, production capacity, and compliance with quality standards.
– **Industry Analysis:** Keeping track of industry trends and geopolitical developments that may affect material availability.
– **Environmental Scanning:** Monitoring weather patterns and natural disaster forecasts to anticipate disruptions.
Risk Assessment and Prioritization
Once the risks have been identified, the next step is to assess their potential impact and likelihood of occurrence.
This involves evaluating how each risk could affect the supply chain and prioritizing them based on their severity and urgency.
Tools such as risk matrices and SWOT analysis can be used to determine which risks need immediate attention and which can be managed over a longer time frame.
Risk Mitigation Strategies
After assessing the risks, developing mitigation strategies is critical to minimizing their impact.
Here are some strategies that organizations can employ:
– **Diversification:** Working with multiple suppliers from different geographical locations to reduce dependency on a single source.
– **Contracts and Agreements:** Implementing robust contracts with suppliers that include clauses for penalties, delivery timelines, and quality standards.
– **Inventory Management:** Maintaining optimal inventory levels to cushion against supply chain disruptions.
– **Technology Integration:** Utilizing technology for supply chain visibility, real-time monitoring, and predictive analytics to anticipate potential risks.
Continuous Monitoring and Review
Risk management is an ongoing process that requires continuous monitoring and review.
Organizations should regularly revisit their risk management model to ensure it remains effective and relevant in the face of changing circumstances.
This involves:
– **Regular Reviews:** Conducting periodic reviews of risk assessments and mitigation strategies to ensure they are up to date.
– **Feedback Loops:** Encouraging feedback from suppliers and stakeholders to identify areas that need improvement.
– **Dynamic Adaptation:** Being flexible and ready to adapt strategies as new risks emerge or existing risks evolve.
The Role of Communication
Effective communication is key to successful risk management.
Purchasing departments should establish clear communication channels with suppliers, stakeholders, and internal teams to ensure information is shared efficiently and promptly.
This helps in building strong relationships, fostering collaboration, and ensuring swift response to potential risks.
Conclusion
Managing material supply risks is an essential function of purchasing departments in today’s interconnected world.
By understanding the different types of risks, assessing their impact, and implementing robust risk management strategies, organizations can safeguard their supply chains against potential disruptions.
Continuous monitoring, flexible adaptation, and effective communication are critical components of a successful risk management model.
By adhering to these principles, purchasing departments can navigate the complexities of material supply risks with confidence and resilience.
資料ダウンロード
QCD調達購買管理クラウド「newji」は、調達購買部門で必要なQCD管理全てを備えた、現場特化型兼クラウド型の今世紀最高の購買管理システムとなります。
ユーザー登録
調達購買業務の効率化だけでなく、システムを導入することで、コスト削減や製品・資材のステータス可視化のほか、属人化していた購買情報の共有化による内部不正防止や統制にも役立ちます。
NEWJI DX
製造業に特化したデジタルトランスフォーメーション(DX)の実現を目指す請負開発型のコンサルティングサービスです。AI、iPaaS、および先端の技術を駆使して、製造プロセスの効率化、業務効率化、チームワーク強化、コスト削減、品質向上を実現します。このサービスは、製造業の課題を深く理解し、それに対する最適なデジタルソリューションを提供することで、企業が持続的な成長とイノベーションを達成できるようサポートします。
オンライン講座
製造業、主に購買・調達部門にお勤めの方々に向けた情報を配信しております。
新任の方やベテランの方、管理職を対象とした幅広いコンテンツをご用意しております。
お問い合わせ
コストダウンが利益に直結する術だと理解していても、なかなか前に進めることができない状況。そんな時は、newjiのコストダウン自動化機能で大きく利益貢献しよう!
(Β版非公開)