- お役立ち記事
- Selection of multiple suppliers and contract negotiations that combine risk diversification and quality assurance
Selection of multiple suppliers and contract negotiations that combine risk diversification and quality assurance
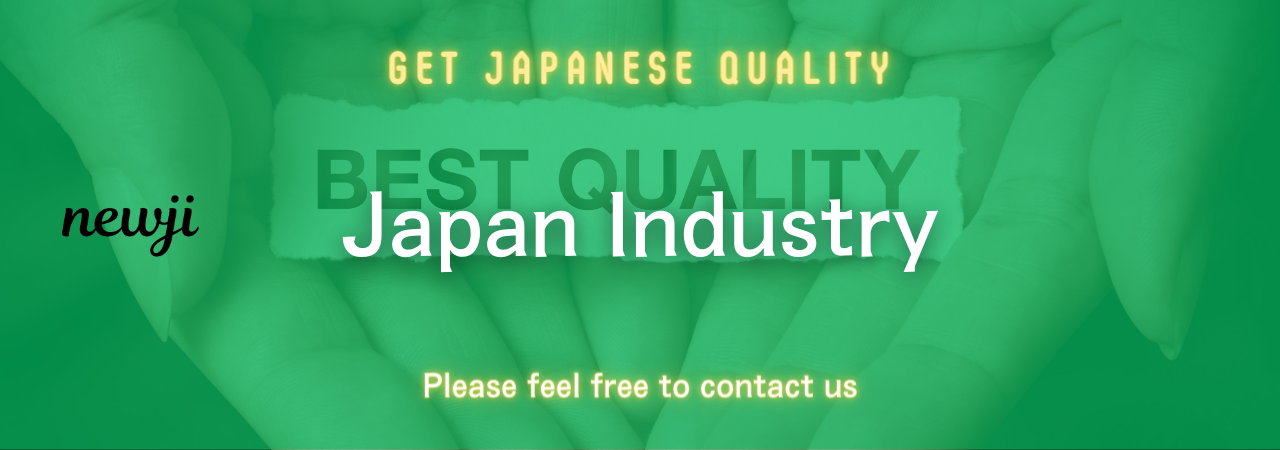
目次
Understanding the Importance of Supplier Selection
In today’s competitive business landscape, selecting the right suppliers is a crucial step for any organization striving for success.
The process involves not just evaluating cost but also ensuring that suppliers can deliver on quality, reliability, and performance.
The ultimate goal is to balance risk and quality, which necessitates careful planning and negotiation.
Selecting multiple suppliers can be an effective strategy for diversifying risks associated with dependency on a single supplier.
This approach helps companies to mitigate supply chain disruptions and enhances their ability to adapt to market changes.
However, managing multiple suppliers requires effective contract negotiations and clear communication.
Why Diversify Supplier Base
Relying on a single supplier can expose a business to various risks including product shortages, quality issues, or price increases.
These risks can be mitigated by spreading orders across multiple suppliers.
Diversifying your supplier base not only reduces the impact of any single supplier failing to meet expectations but also increases leverage in negotiations, as it reduces dependency.
Having multiple suppliers also encourages competition, which can lead to better pricing and improved service levels.
This competitive environment forces suppliers to continuously enhance their offerings to maintain your business.
Additionally, diversifying suppliers allows for greater flexibility and innovation, as you have access to a wider pool of potential solutions and ideas.
Criteria for Selecting Suppliers
When choosing suppliers, several criteria need to be evaluated to ensure a balanced selection that aligns with organizational goals.
Quality and Reliability
The most fundamental criterion for supplier selection is the quality of their products or services.
Conduct thorough evaluations to ensure that suppliers meet your company’s quality standards.
Reliable delivery schedules and the ability to adapt to changing demands are equally important to ensure consistent supply.
Cost Effectiveness
While cost should not be the sole determining factor, it is undoubtedly significant.
Negotiate to achieve competitive pricing without compromising on quality or reliability.
Assess the total cost of ownership, which includes factors such as shipping and handling, to accurately compare options.
Financial Stability
The financial health of a supplier is critical since it impacts their ability to fulfill orders over the long term.
Request financial statements or conduct credit checks to ensure that your suppliers have the necessary financial stability to support their operations.
Technical Capability and Capacity
Verify that suppliers have the technical capability to deliver the required products and services.
Ensure that they have sufficient production capacity and technological know-how to meet your future demand projections.
Alignment with Corporate Values
Consider whether the supplier shares your corporate values and commitment to ethical practices.
This includes evaluating labor practices, environmental sustainability, and regulatory compliance.
Contract Negotiations: Balancing Risk and Quality
Entering into contract negotiations with suppliers demands strategic planning to balance risk against quality assurance.
Contracts should be detailed and clearly outline the expectations and responsibilities of both parties.
Negotiating Terms and Conditions
Start by defining the scope of work, delivery schedules, quality standards, and payment terms.
Incorporate clauses that address potential risks, such as delivery delays or product defects, and specify the penalties for non-compliance.
Discuss warranties and liabilities to protect your organization from unforeseen issues.
Ensure that the contract provides provisions for monitoring and auditing supplier performance regularly.
Building Long-term Relationships
The goal of contract negotiations should extend beyond immediate transactions to fostering long-term partnerships.
Building strong relationships with suppliers enhances collaboration and innovation.
Engage suppliers in regular communication and feedback mechanisms to cultivate mutual trust and understanding.
Utilizing Performance Metrics
Incorporate performance metrics into contracts to measure success objectively.
This includes quality ratings, delivery timelines, and cost targets.
Use these metrics to identify areas that require improvement and work collaboratively with suppliers to enhance performance.
Managing Multiple Supplier Relationships
Once contracts are in place, managing relationships with multiple suppliers becomes critical to sustaining operational efficiency.
Clear Communication Channels
Establish clear communication channels to facilitate timely and effective interaction with all suppliers.
Deploy technology solutions such as supplier management platforms to streamline communications and data sharing.
Regular Evaluation and Feedback
Regularly assess supplier performance against defined metrics and provide constructive feedback.
This allows you to address issues proactively and ensure continuous improvements.
In the event of underperformance, work with suppliers to develop corrective action plans.
Risk Management
Continuously monitor the supply chain for potential risks and disruptions.
Develop contingency plans to safeguard operations if a supplier can no longer deliver on commitments.
Diversify sources further if necessary to minimize risks.
Conclusion
Selection of multiple suppliers and strategic contract negotiations are paramount in achieving a balance between risk diversification and quality assurance.
By carefully evaluating supplier criteria and engaging in strategic contract negotiations, organizations can build responsive and resilient supply chains.
These efforts pave the way for long-lasting relationships with suppliers, fostering innovation and competitiveness in an ever-evolving market.
資料ダウンロード
QCD調達購買管理クラウド「newji」は、調達購買部門で必要なQCD管理全てを備えた、現場特化型兼クラウド型の今世紀最高の購買管理システムとなります。
ユーザー登録
調達購買業務の効率化だけでなく、システムを導入することで、コスト削減や製品・資材のステータス可視化のほか、属人化していた購買情報の共有化による内部不正防止や統制にも役立ちます。
NEWJI DX
製造業に特化したデジタルトランスフォーメーション(DX)の実現を目指す請負開発型のコンサルティングサービスです。AI、iPaaS、および先端の技術を駆使して、製造プロセスの効率化、業務効率化、チームワーク強化、コスト削減、品質向上を実現します。このサービスは、製造業の課題を深く理解し、それに対する最適なデジタルソリューションを提供することで、企業が持続的な成長とイノベーションを達成できるようサポートします。
オンライン講座
製造業、主に購買・調達部門にお勤めの方々に向けた情報を配信しております。
新任の方やベテランの方、管理職を対象とした幅広いコンテンツをご用意しております。
お問い合わせ
コストダウンが利益に直結する術だと理解していても、なかなか前に進めることができない状況。そんな時は、newjiのコストダウン自動化機能で大きく利益貢献しよう!
(Β版非公開)