- お役立ち記事
- Practical example of purchasing department backup strategy to minimize material supply risk
Practical example of purchasing department backup strategy to minimize material supply risk
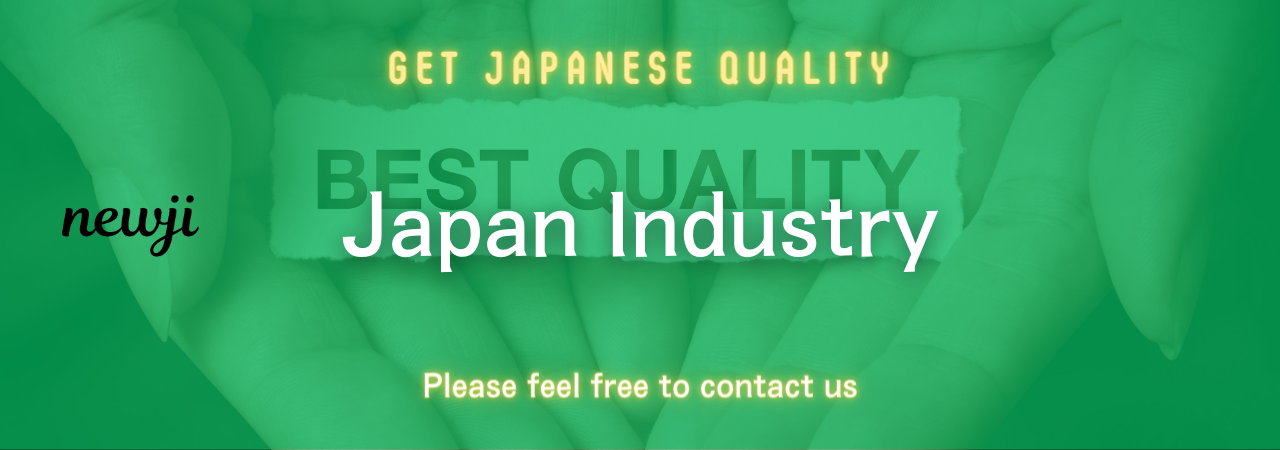
目次
Understanding the Importance of a Backup Strategy in the Purchasing Department
In today’s business environment, risks in the supply chain are a common concern for many companies.
One of the most critical parts of a smooth-sailing supply chain is the purchasing department.
When material supply is disrupted, the entire production line can grind to a halt.
To combat this, having a robust backup strategy is essential to minimize material supply risk.
This article will delve into practical examples of backup strategies that purchasing departments can implement to ensure seamless operations.
The Role of the Purchasing Department in Supply Chain Management
The purchasing department is pivotal in managing relationships with suppliers, negotiating terms, and ensuring materials are delivered on time.
They are at the forefront of addressing supply chain disruptions, which can arise due to political unrest, natural disasters, financial instability, or even pandemics.
Mitigating Risks through a Diversified Supply Base
One practical backup strategy is diversifying the supply base.
Relying on a single supplier can be risky if they face any unforeseen issues.
By having multiple suppliers for key materials, companies can mitigate the impact of a disruption with one supplier.
Diversity in suppliers not only spreads risk but also enhances negotiation power and ensures competitive pricing.
Implementing a Dual-Sourcing Strategy
Dual-sourcing involves engaging with two suppliers for the same material requirement.
This strategy ensures that if one supplier experiences delays or stock issues, the other supplier can fulfill the demand.
This approach is particularly beneficial for high-value or critical components that can stall production.
Vendor Collaboration and Communication
Building strong relationships with suppliers is crucial.
Purchasing departments should engage in regular communication with vendors and maintain transparency about their expectations.
Collaborating closely allows both parties to anticipate potential disruptions and develop contingency plans effectively.
Regular meetings, joint forecasting, and long-term partnerships facilitate better coordination and trust.
Leveraging Technology for Better Supplier Management
Using technology to automate and improve processes in the purchasing department is another effective backup strategy.
Supplier Relationship Management (SRM) tools enable companies to monitor supplier performance, assess risks, and track real-time data.
These tools offer insights that help in making informed decisions, allowing purchasing departments to react swiftly to disruptions.
Contractual Safeguards with Suppliers
Drafting contracts with suppliers that include specific clauses related to delivery timelines, quality standards, and penalty conditions is essential.
Such contractual safeguards protect companies against risks by legally binding the suppliers to certain obligations.
Moreover, including clauses for alternative sourcing or emergency supply can further strengthen the resilience against supply interruptions.
Stock Buffering Strategy
Having safety stock or buffer inventory is a precautionary measure to minimize supply risk.
It acts as a cushion that allows businesses to continue operations during short-term disruptions.
However, this must be balanced carefully, as excessive inventory can increase holding costs and lead to waste if not managed properly.
Supplier Financial Health Check
Understanding the financial stability of suppliers is a proactive measure to reduce risk.
Purchasing departments should conduct regular assessments of their suppliers’ financial health.
Particularly for key raw materials or components, knowing a supplier’s ability to weather economic fluctuations protects against sudden collapses or bankruptcies.
Scenario Planning and Risk Assessment
Conducting scenario planning and risk assessments prepares purchasing departments to handle various potential disruptions.
By evaluating the likelihood and impact of different risks, companies can develop contingency plans tailored to specific scenarios.
This planning process enables businesses to act swiftly and effectively when issues arise.
Developing an Agile Procurement Process
An agile procurement process allows companies to adapt quickly to changes in the supply chain environment.
It involves streamlining processes, training staff to handle unforeseen circumstances, and being open to innovation.
An agile approach is also proactive, using data analytics and forecasting to anticipate and respond to market trends.
Training and Development for Procurement Staff
Investing in the skills and knowledge of procurement staff is vital for an effective backup strategy.
Training programs that focus on risk management, negotiation skills, and supply chain best practices empower staff to handle supply risks adeptly.
Well-trained teams are better equipped to develop and execute strategic plans that minimize material supply risks.
Conclusion
Minimizing material supply risks in the purchasing department requires a multifaceted approach.
By diversifying suppliers, leveraging technology, and maintaining strong vendor relationships, companies can build a resilient supply chain.
Additionally, incorporating contractual safeguards, stock buffering, and agile procurement processes contribute to reducing dependency and vulnerability.
Ultimately, investing in staff training and conducting regular risk assessments help in creating a robust backup strategy that safeguards against potential supply disruptions.
資料ダウンロード
QCD調達購買管理クラウド「newji」は、調達購買部門で必要なQCD管理全てを備えた、現場特化型兼クラウド型の今世紀最高の購買管理システムとなります。
ユーザー登録
調達購買業務の効率化だけでなく、システムを導入することで、コスト削減や製品・資材のステータス可視化のほか、属人化していた購買情報の共有化による内部不正防止や統制にも役立ちます。
NEWJI DX
製造業に特化したデジタルトランスフォーメーション(DX)の実現を目指す請負開発型のコンサルティングサービスです。AI、iPaaS、および先端の技術を駆使して、製造プロセスの効率化、業務効率化、チームワーク強化、コスト削減、品質向上を実現します。このサービスは、製造業の課題を深く理解し、それに対する最適なデジタルソリューションを提供することで、企業が持続的な成長とイノベーションを達成できるようサポートします。
オンライン講座
製造業、主に購買・調達部門にお勤めの方々に向けた情報を配信しております。
新任の方やベテランの方、管理職を対象とした幅広いコンテンツをご用意しております。
お問い合わせ
コストダウンが利益に直結する術だと理解していても、なかなか前に進めることができない状況。そんな時は、newjiのコストダウン自動化機能で大きく利益貢献しよう!
(Β版非公開)