- お役立ち記事
- Specific measures to help purchasing departments improve traceability throughout the supply chain
Specific measures to help purchasing departments improve traceability throughout the supply chain
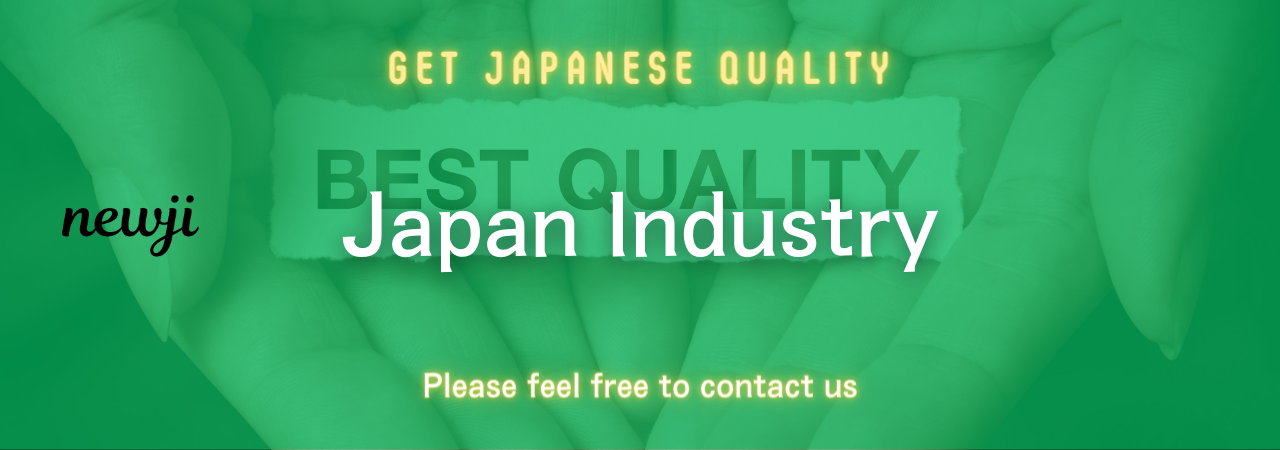
目次
Understanding the Importance of Traceability in Supply Chains
Traceability in supply chains has become a strategic priority for businesses in today’s interconnected world.
It refers to the ability to track and trace production processes from raw material to finished goods.
This capability is crucial for ensuring product quality, compliance with regulations, and meeting consumer expectations for transparency.
The purchasing department plays a critical role in improving traceability, as their efforts directly impact the management of suppliers and the integrity of the entire supply chain.
The Role of Purchasing Departments in Enhancing Traceability
In any organization, the purchasing department is responsible for acquiring the necessary resources and services required for production.
Their activities are not limited to just buying; they are pivotal for establishing clear communication and dependable relationships with suppliers.
Purchasing departments lay the foundation for enhanced traceability by implementing strategies that ensure suppliers adhere to agreed standards and practices.
To effectively improve traceability, purchasing departments need to incorporate certain measures that help in tracking the flow of materials.
These measures include choosing the right technologies and adhering to standardized procedures.
Implementing Effective Measures for Improved Traceability
Select the Right Suppliers
Choosing reliable suppliers is fundamental to maintaining traceability.
Purchasing departments should prioritize establishing partnerships with suppliers who demonstrate transparency in their operations.
Evaluating suppliers based on their record-keeping practices, compliance with industry standards, and willingness to share information is vital.
Conducting audits and requiring certifications can also ensure suppliers maintain traceability standards.
Integrate Advanced Technology Solutions
Technology plays a significant role in securing traceability within the supply chain.
Purchasing departments should explore integrating advanced solutions such as barcoding, RFID systems, and blockchain technology.
These tools facilitate the real-time tracking of materials, provide accurate data, and automate documentation processes.
Implementing cloud-based software solutions can also streamline data sharing across the supply chain.
Cloud platforms support centralized databases, enabling easy access to information for all stakeholders involved.
Standardize Record-Keeping Practices
Consistency in record-keeping is essential for effective traceability.
Purchasing departments should work towards standardizing documentation practices across the supply chain.
This includes maintaining accurate records of purchase orders, delivery receipts, inventory logs, and supplier certifications.
Documenting each transaction meticulously ensures that there is a clear chain of custody, reducing the risk of errors or information loss.
These records should be easily accessible and auditable for verification purposes.
Fostering Collaboration Across the Supply Chain
Encourage Supplier Collaboration
Collaboration across the supply chain strengthens partnerships and enhances traceability.
Purchasing departments should engage suppliers as active participants in traceability initiatives.
Regular meetings, training sessions, and workshops can help align suppliers with company goals.
Encouraging open communication and collaboration helps suppliers understand traceability requirements and actively contribute to achieving them.
Building long-term relationships with suppliers fosters trust and reliability, which are fundamental for traceability success.
Establish Clear Traceability Protocols
Establishing clear traceability protocols ensures that every stakeholder in the supply chain knows their role and responsibilities.
Purchasing departments should collaborate with other teams to develop protocols that outline standards for tracking, documentation, and reporting.
These protocols should include clear guidelines on how to handle discrepancies, manage product recalls, and improve product traceability from end to end.
Establishing key performance indicators (KPIs) to measure traceability success can also provide valuable insights for continuous improvement.
Enhancing Consumer Confidence Through Improved Traceability
Communicate Transparency to Consumers
Consumers today are more conscious of product origins and production processes.
By promoting traceability, companies can enhance consumer confidence and differentiate themselves in the market.
Purchasing departments play a role in effectively communicating transparency to consumers through accurate labeling and detailed product information.
Providing consumers with access to information about sourcing, production, and distribution reassures them about product safety and quality.
Address Regulatory Compliance Requirements
Compliance with industry regulations is a critical aspect of maintaining traceability.
Purchasing departments should ensure that suppliers comply with relevant regulations and standards.
Staying updated with regulatory changes and proactively addressing compliance requirements reduces risks associated with non-compliance.
Compliance is not only a legal obligation but also adds value to consumer trust and brand reputation.
Conclusion
Improving traceability throughout the supply chain is essential for modern businesses aiming to maintain quality, transparency, and consumer trust.
By selecting reliable suppliers, integrating technology solutions, and fostering collaboration, purchasing departments can significantly enhance traceability.
Embracing transparency, standardizing practices, and adhering to regulations further strengthen an organization’s competitive edge.
Traceability is not just a beneficial practice; it is a strategic asset that empowers businesses to meet the demands of today’s informed consumers while ensuring sustainability and efficiency.
資料ダウンロード
QCD調達購買管理クラウド「newji」は、調達購買部門で必要なQCD管理全てを備えた、現場特化型兼クラウド型の今世紀最高の購買管理システムとなります。
ユーザー登録
調達購買業務の効率化だけでなく、システムを導入することで、コスト削減や製品・資材のステータス可視化のほか、属人化していた購買情報の共有化による内部不正防止や統制にも役立ちます。
NEWJI DX
製造業に特化したデジタルトランスフォーメーション(DX)の実現を目指す請負開発型のコンサルティングサービスです。AI、iPaaS、および先端の技術を駆使して、製造プロセスの効率化、業務効率化、チームワーク強化、コスト削減、品質向上を実現します。このサービスは、製造業の課題を深く理解し、それに対する最適なデジタルソリューションを提供することで、企業が持続的な成長とイノベーションを達成できるようサポートします。
オンライン講座
製造業、主に購買・調達部門にお勤めの方々に向けた情報を配信しております。
新任の方やベテランの方、管理職を対象とした幅広いコンテンツをご用意しております。
お問い合わせ
コストダウンが利益に直結する術だと理解していても、なかなか前に進めることができない状況。そんな時は、newjiのコストダウン自動化機能で大きく利益貢献しよう!
(Β版非公開)