- お役立ち記事
- Risks faced by purchasing departments when procuring new materials and their countermeasures
Risks faced by purchasing departments when procuring new materials and their countermeasures
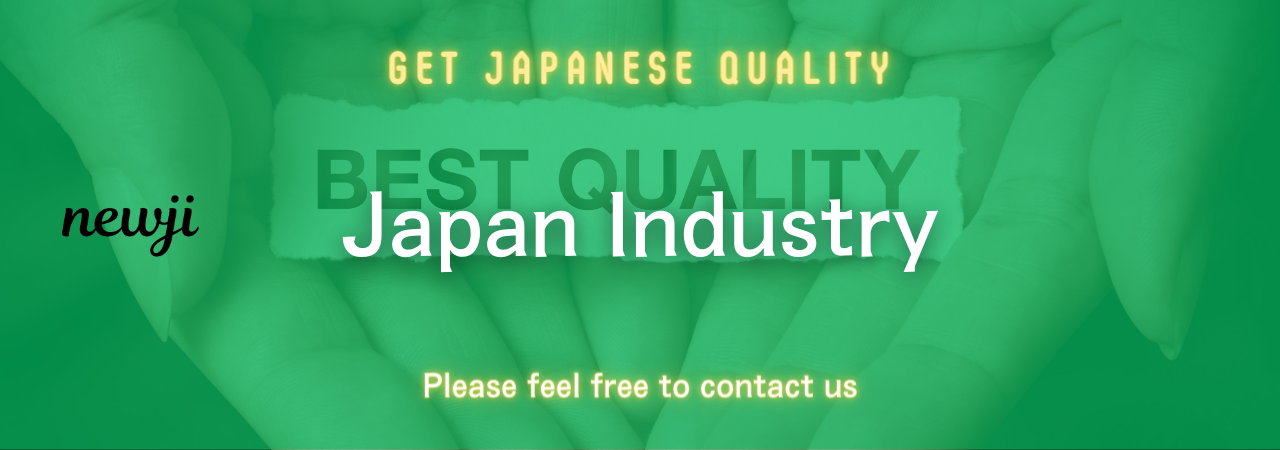
目次
Understanding the Challenges in Material Procurement
Purchasing departments play a crucial role in any organization, ensuring that the necessary materials are acquired efficiently and cost-effectively.
When it comes to procuring new materials, these departments encounter various risks that can impact the overall success of their operations.
Understanding these risks and deploying effective countermeasures is essential for maintaining smooth procurement processes.
Procurement of new materials can present unique challenges compared to established sourcing routines.
It involves dealing with unfamiliar suppliers, quality uncertainties, and potential supply chain disruptions.
Therefore, a well-defined strategy is vital to mitigate these risks and ensure the organization’s goals are met without unforeseen hindrances.
Main Risks in Procuring New Materials
Supplier Reliability
One of the primary risks in procuring new materials is supplier reliability.
When dealing with new vendors, there is often limited information available about their credibility, capability, and track record.
This lack of knowledge can lead to difficulties in quality assurance, delivery times, and consistency, ultimately affecting the production schedule.
Quality and Compliance Issues
Ensuring that new materials meet the required quality standards and comply with industry regulations is critical.
When introducing new materials, purchasing departments may face challenges in assessing the quality without prior experience with the supplier’s product.
Non-compliance and poor quality can lead to production delays, increased costs, and potential core company issues.
Cost Fluctuation
Commodity prices can be volatile, and new suppliers may not offer long-term pricing agreements immediately.
This uncertainty can lead to unexpected cost fluctuations, which could impact the organization’s budget and financial planning.
Purchasing departments must be vigilant and prepared for such situations to prevent budget overruns.
Supply Chain Disruption
Introducing new materials into the supply chain often comes with the risk of unexpected disruptions.
Transportation issues, geopolitical tensions, or global health crises can hinder material supply.
Without established contingency plans or alternative suppliers, the organization may face production downtime or increased lead times.
Intellectual Property Concerns
With new materials, there is often the consideration of intellectual property (IP) protection, especially concerning innovative products.
Suppliers could potentially infringe on patents or misuse proprietary information.
Purchasing departments must ensure that proper legal measures are in place to safeguard against such issues.
Effective Countermeasures to Mitigate Risks
Thorough Supplier Evaluation
Before engaging with a new supplier, conducting a comprehensive evaluation is essential.
This includes assessing their financial stability, previous client reviews, and capacity for meeting delivery schedules.
Requesting samples or conducting site visits can provide additional insights into their operations and product quality.
Implementing Quality Assurance Protocols
Setting up strict quality assurance protocols is vital when procuring new materials.
Purchasing departments should specify clear quality standards and perform regular audits and inspections.
Establishing a robust quality control system can help in detecting any deviations early and addressing them promptly.
Negotiating Flexible Terms
To manage cost fluctuations, negotiating flexible pricing terms with suppliers is beneficial.
Engaging in discussions about price adjustment mechanisms tied to market indices or securing fixed-rate contracts can provide more predictability in budgeting.
Developing Contingency Plans
Having a contingency plan is crucial to addressing potential supply chain disruptions.
This involves identifying alternative suppliers and transportation routes in advance.
Regularly updating these plans ensures that the purchasing department can swiftly respond to any unforeseen challenges.
Establishing Legal Safeguards
Protecting intellectual property from the outset is essential when acquiring new materials.
Clearly defined contracts specifying IP rights, confidentiality agreements, and non-disclosure terms should be in place.
Working closely with the legal team will ensure compliance and protection for both parties involved.
The Importance of Effective Communication and Collaboration
Open communication and collaboration with internal stakeholders and suppliers are vital in addressing procurement risks.
Regular meetings and feedback loops will keep all parties aligned on objectives, challenges, and progress.
Fostering strong relationships encourages transparency and trust, making it easier to resolve issues as they arise.
Additionally, educating employees involved in procurement about these risks and countermeasures can enhance overall awareness and readiness.
Training sessions, workshops, and access to updated market information can equip them with the knowledge to make informed decisions.
Conclusion
Risk management in procuring new materials is a multifaceted task that requires a proactive approach.
By understanding the potential challenges and implementing effective countermeasures, purchasing departments can mitigate risks and enhance the procurement process.
Fostering strong collaborations, detailed evaluations, and strategic planning will ensure organizations remain resilient in the face of procurement uncertainties.
This approach not only supports seamless operations but also contributes to sustained business growth and success.
資料ダウンロード
QCD調達購買管理クラウド「newji」は、調達購買部門で必要なQCD管理全てを備えた、現場特化型兼クラウド型の今世紀最高の購買管理システムとなります。
ユーザー登録
調達購買業務の効率化だけでなく、システムを導入することで、コスト削減や製品・資材のステータス可視化のほか、属人化していた購買情報の共有化による内部不正防止や統制にも役立ちます。
NEWJI DX
製造業に特化したデジタルトランスフォーメーション(DX)の実現を目指す請負開発型のコンサルティングサービスです。AI、iPaaS、および先端の技術を駆使して、製造プロセスの効率化、業務効率化、チームワーク強化、コスト削減、品質向上を実現します。このサービスは、製造業の課題を深く理解し、それに対する最適なデジタルソリューションを提供することで、企業が持続的な成長とイノベーションを達成できるようサポートします。
オンライン講座
製造業、主に購買・調達部門にお勤めの方々に向けた情報を配信しております。
新任の方やベテランの方、管理職を対象とした幅広いコンテンツをご用意しております。
お問い合わせ
コストダウンが利益に直結する術だと理解していても、なかなか前に進めることができない状況。そんな時は、newjiのコストダウン自動化機能で大きく利益貢献しよう!
(Β版非公開)