- お役立ち記事
- The importance of quality assurance and traceability management that purchasing departments should perform
The importance of quality assurance and traceability management that purchasing departments should perform
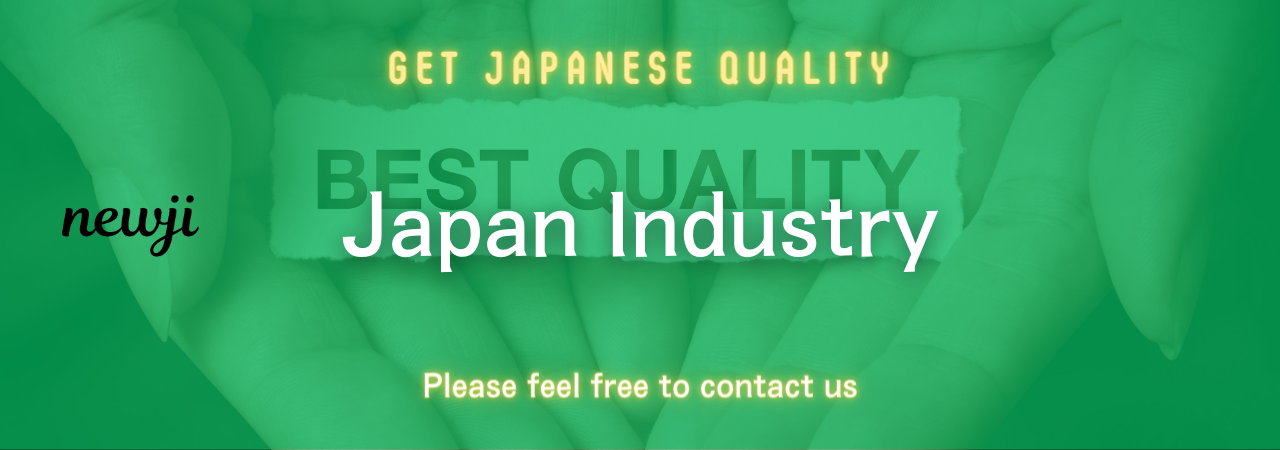
目次
Understanding Quality Assurance
Quality assurance is a critical aspect of any manufacturing or service-oriented business.
It involves various processes and activities that ensure products or services meet specific standards and customer expectations.
For purchasing departments, quality assurance serves as a vital checkpoint to verify that materials and products sourced from suppliers are up to the required standards.
One of the primary objectives of quality assurance is to prevent defects in the products procured.
This involves meticulous planning, execution, and monitoring of processes to identify potential areas of improvement.
By doing so, companies can deliver safer and more reliable products to their customers, thereby enhancing their reputation and fostering customer loyalty.
Moreover, quality assurance helps in reducing costs associated with defects, such as returns and repairs.
Investing in quality assurance upfront can lead to significant cost savings down the line.
For purchasing departments, this means fewer financial surprises and a better-managed budget.
The Role of Traceability Management
Traceability management is the ability to track the history, application, and location of an item or product.
In purchasing departments, traceability ensures that all components and materials can be traced back to their origin.
This is crucial for maintaining quality and compliance with regulations.
Traceability management provides transparency across the supply chain, allowing for quick identification of problematic batches.
When a defect is detected, traceability helps to isolate the issue quickly and efficiently.
This rapid response capability minimizes the impact on production and reduces the risk of defective products reaching customers.
Additionally, traceability management is essential for compliance with industry standards and legal requirements.
It enables companies to demonstrate due diligence in the case of audits or inspections.
For purchasing departments, maintaining robust traceability records can mitigate risks associated with liability claims.
Benefits of Quality Assurance and Traceability
Implementing quality assurance and traceability management systems offers numerous benefits to purchasing departments.
These measures ensure that only high-quality, compliant products are acquired, boosting the company’s overall product integrity.
Quality assurance instills confidence in suppliers.
When suppliers understand that their products will be scrutinized, they are more likely to maintain high production standards.
This creates a reliable supplier base, reducing the likelihood of disruptions in the supply chain.
Traceability, on the other hand, provides a safety net in the event of quality issues.
It allows companies to act swiftly and decisively, preventing small issues from escalating into larger problems.
Moreover, strong traceability frameworks reassure stakeholders, including customers, regulators, and investors, that the company operates transparently and responsibly.
Combining Quality Assurance and Traceability for Optimal Results
When quality assurance and traceability are integrated effectively, organizations can achieve significant operational improvements.
This combination allows for better inventory management, enhanced supplier collaborations, and improved customer satisfaction.
Purchasing departments can leverage data from traceability systems to assess supplier performance over time.
By analyzing patterns and discrepancies, organizations can make informed decisions about future procurements.
This can result in choosing more reliable suppliers and building long-term partnerships that benefit both parties.
Furthermore, quality assurance protocols need to be agile enough to adapt to the evolving needs of the business.
This adaptability ensures that products meet both current and future consumer expectations, providing a competitive edge in the market.
Challenges and Solutions
While implementing quality assurance and traceability systems is beneficial, it comes with its own set of challenges.
One major challenge is the integration of these systems with existing processes and technologies.
For many organizations, transitioning from traditional methods to advanced tracking systems requires substantial investment in both time and resources.
To overcome these challenges, companies can start by conducting a thorough assessment of their current processes.
Identifying gaps and areas that require improvement helps in tailoring solutions that address specific needs.
Moreover, leveraging technology, such as blockchain and the Internet of Things (IoT), can enhance traceability and quality assurance efforts.
Another challenge is maintaining employee engagement and compliance with quality protocols.
To address this, companies should focus on creating a culture of quality within the organization.
Regular training, clear communication, and incentivization of quality improvements can significantly boost employee involvement and adherence to quality standards.
Conclusion
In today’s competitive market, purchasing departments play a pivotal role in ensuring the quality of the final product.
Both quality assurance and traceability management are essential components in fulfilling this responsibility.
These processes not only enhance product reliability and safety but also protect the organization from financial, legal, and reputational risks.
Incorporating a robust quality assurance and traceability framework can lead to cost savings, improve supply chain efficiency, and ensure customer satisfaction.
As technology continues to evolve, it’s critical for purchasing departments to remain vigilant and adaptable, embracing new methodologies and tools that can further enhance product quality and traceability.
By prioritizing quality assurance and traceability, companies can forge stronger supplier relationships, stay compliant, and maintain a competitive advantage in the marketplace.
資料ダウンロード
QCD調達購買管理クラウド「newji」は、調達購買部門で必要なQCD管理全てを備えた、現場特化型兼クラウド型の今世紀最高の購買管理システムとなります。
ユーザー登録
調達購買業務の効率化だけでなく、システムを導入することで、コスト削減や製品・資材のステータス可視化のほか、属人化していた購買情報の共有化による内部不正防止や統制にも役立ちます。
NEWJI DX
製造業に特化したデジタルトランスフォーメーション(DX)の実現を目指す請負開発型のコンサルティングサービスです。AI、iPaaS、および先端の技術を駆使して、製造プロセスの効率化、業務効率化、チームワーク強化、コスト削減、品質向上を実現します。このサービスは、製造業の課題を深く理解し、それに対する最適なデジタルソリューションを提供することで、企業が持続的な成長とイノベーションを達成できるようサポートします。
オンライン講座
製造業、主に購買・調達部門にお勤めの方々に向けた情報を配信しております。
新任の方やベテランの方、管理職を対象とした幅広いコンテンツをご用意しております。
お問い合わせ
コストダウンが利益に直結する術だと理解していても、なかなか前に進めることができない状況。そんな時は、newjiのコストダウン自動化機能で大きく利益貢献しよう!
(Β版非公開)