- お役立ち記事
- Purchasing department vendor management techniques to improve material supply reliability
Purchasing department vendor management techniques to improve material supply reliability
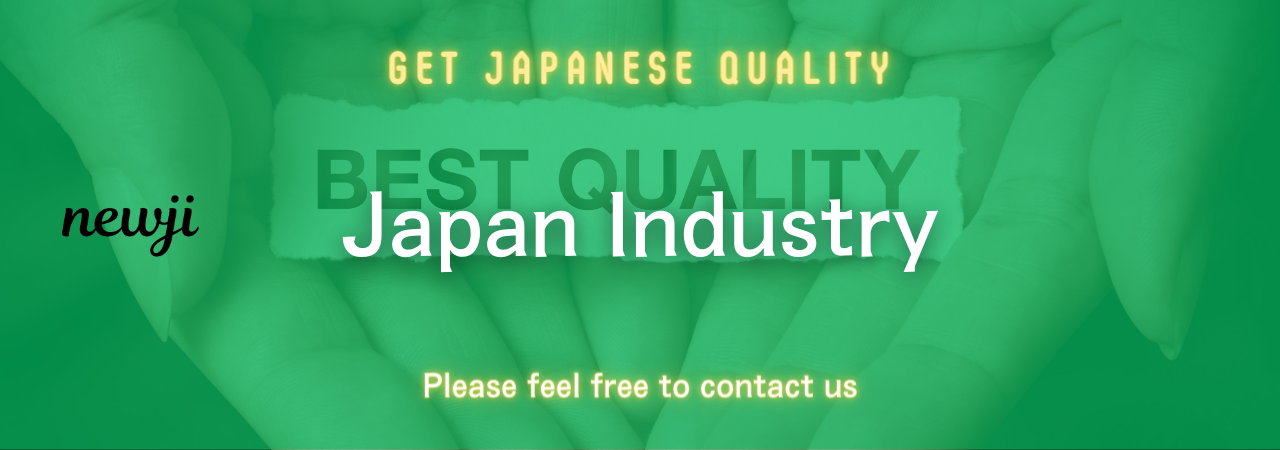
目次
Understanding Vendor Management in the Purchasing Department
Vendor management is a critical component of any purchasing department’s operations.
It involves the systematic approach to managing suppliers and ensuring the reliability of material supply.
Without effective vendor management, businesses may face disruptions, leading to project delays, increased costs, and compromised quality.
For purchasing departments, the primary objective of vendor management is to enhance supply chain reliability.
This involves choosing the right vendors, negotiating favorable terms, and maintaining strong, productive relationships.
By honing vendor management techniques, businesses can secure dependable material supplies vital for continued success.
Assessing Vendor Performance
The first step in improving material supply reliability is to assess and evaluate vendor performance regularly.
This involves setting clear performance indicators and metrics to gauge how well vendors are meeting contractual obligations.
Performance indicators often include delivery times, quality of materials, flexibility, and cost-effectiveness.
Regular vendor performance evaluations help identify bottlenecks or inefficiencies in the supply chain.
By addressing these issues early, the purchasing department can work with vendors to implement corrective actions.
This proactive approach ensures that potential supply disruptions are mitigated before they impact business operations.
Building Strong Vendor Partnerships
Establishing strong partnerships with vendors is essential for reliable material supply.
Engaging in open and transparent communication with vendors builds trust and mutual understanding.
This relationship should be nurtured over time through consistent interaction and collaboration.
One effective technique is to treat vendors as strategic partners rather than just suppliers.
By involving them in goal-setting and product development processes, businesses can create a more collaborative environment.
When vendors feel valued, they are more likely to prioritize and allocate resources to fulfill contractual obligations efficiently.
Implementing Vendor Selection Criteria
A crucial technique for improving supply reliability is establishing robust vendor selection criteria.
This involves evaluating potential suppliers based on factors such as financial stability, industry reputation, technical capabilities, and compliance with industry standards.
The purchasing department should conduct thorough due diligence before onboarding a new vendor.
This might include site visits, financial assessments, and reference checks.
A comprehensive selection process ensures that the chosen vendors can consistently meet the organization’s supply needs.
Nurturing a Diverse Vendor Base
Relying heavily on a single vendor can pose significant risks to material supply reliability.
To mitigate these risks, purchasing departments should develop a diverse vendor base.
Having multiple suppliers for critical materials provides a buffer against potential supply chain disruptions.
Diversification should not compromise quality or cost-efficiency, however.
Businesses must carefully balance the benefits of having multiple vendors with maintaining standards across all suppliers.
An optimal vendor base ensures a reliable flow of materials, even in adverse conditions.
Leveraging Technology for Vendor Management
Technology plays a pivotal role in enhancing vendor management techniques.
By using digital platforms, purchasing departments can automate processes, track vendor performance, and streamline communication.
Vendor management software offers various features, such as procurement analytics, automated reporting, and real-time performance monitoring.
These tools provide valuable insights into supply chain dynamics and enable data-driven decision-making.
Additionally, leveraging technologies like blockchain can offer transparency and traceability in material sourcing, further improving supply chain reliability.
Negotiating Favorable Contract Terms
Effective negotiation of contract terms is a cornerstone of successful vendor management.
Purchasing departments must focus on negotiating terms that align with the organization’s strategic objectives and supply chain needs.
Contracts should clearly define delivery schedules, quality standards, and responsibilities of both parties.
Inclusion of predefined penalties for non-compliance ensures accountability from vendors.
Favorable contract terms provide a safeguard against supply disruptions and help maintain consistent quality standards.
Ensuring Risk Management and Compliance
Risk management is integral to vendor management as it helps identify and mitigate potential disruptions in the supply chain.
Implementing risk assessment frameworks allows purchasing departments to anticipate and plan for various contingencies.
Vendor compliance with industry regulations and standards is another critical factor.
By ensuring that all vendors meet necessary legal and ethical requirements, businesses can protect themselves from liabilities and reputational damage.
Regular compliance audits and updating vendor risk assessments help maintain a secure and reliable material supply chain.
Conclusion
Vendor management techniques play a vital role in enhancing the reliability of material supply for purchasing departments.
Through evaluating vendor performance, building strong partnerships, and implementing strategic selection criteria, businesses can secure a reliable and efficient supply chain.
Leveraging technology, effectively negotiating contracts, and fostering vendor diversity are essential strategies for minimizing supply chain disruptions.
Risk management and compliance ensure that organizations are prepared for unforeseen challenges and adhere to industry standards.
By applying these vendor management techniques, purchasing departments can significantly improve material supply reliability, ultimately contributing to the organization’s success and sustainability.
資料ダウンロード
QCD調達購買管理クラウド「newji」は、調達購買部門で必要なQCD管理全てを備えた、現場特化型兼クラウド型の今世紀最高の購買管理システムとなります。
ユーザー登録
調達購買業務の効率化だけでなく、システムを導入することで、コスト削減や製品・資材のステータス可視化のほか、属人化していた購買情報の共有化による内部不正防止や統制にも役立ちます。
NEWJI DX
製造業に特化したデジタルトランスフォーメーション(DX)の実現を目指す請負開発型のコンサルティングサービスです。AI、iPaaS、および先端の技術を駆使して、製造プロセスの効率化、業務効率化、チームワーク強化、コスト削減、品質向上を実現します。このサービスは、製造業の課題を深く理解し、それに対する最適なデジタルソリューションを提供することで、企業が持続的な成長とイノベーションを達成できるようサポートします。
オンライン講座
製造業、主に購買・調達部門にお勤めの方々に向けた情報を配信しております。
新任の方やベテランの方、管理職を対象とした幅広いコンテンツをご用意しております。
お問い合わせ
コストダウンが利益に直結する術だと理解していても、なかなか前に進めることができない状況。そんな時は、newjiのコストダウン自動化機能で大きく利益貢献しよう!
(Β版非公開)