- お役立ち記事
- Revolutionizing Japanese Manufacturing: The Impact of Non-Destructive Inspection Techniques
Revolutionizing Japanese Manufacturing: The Impact of Non-Destructive Inspection Techniques
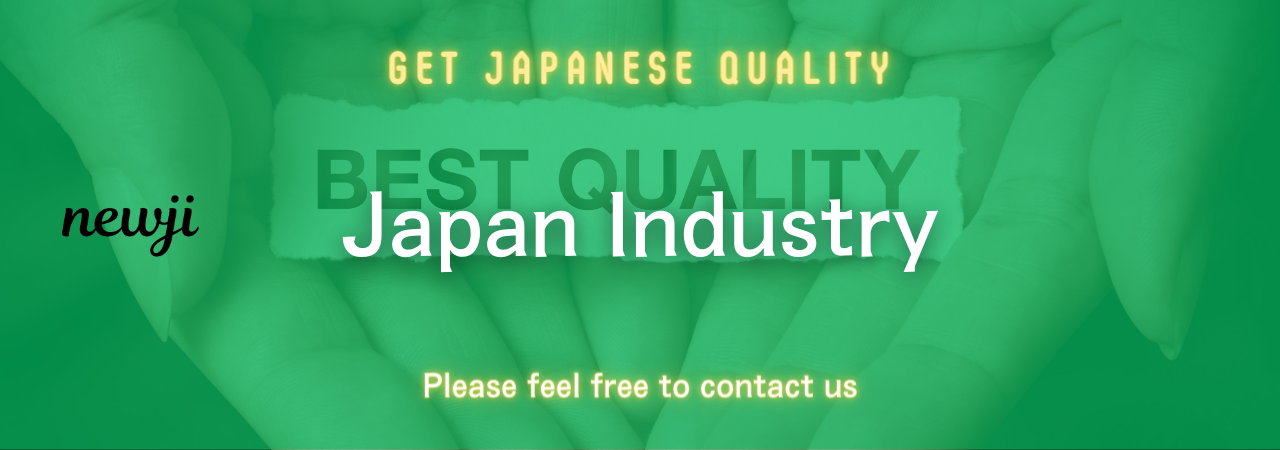
目次
Introduction to Non-Destructive Inspection Techniques in Japanese Manufacturing
Non-destructive inspection (NDI) techniques have revolutionized the landscape of Japanese manufacturing. These advanced methods allow for the evaluation of materials and components without causing any damage. In an industry renowned for its commitment to quality and precision, NDI plays a crucial role in ensuring products meet the highest standards. The integration of NDI has not only enhanced product reliability but also streamlined manufacturing processes, contributing to Japan’s reputation for excellence in manufacturing.
The Importance of NDI in Maintaining Quality Standards
Quality control is paramount in Japanese manufacturing. NDI techniques, such as ultrasonic testing, radiography, and magnetic particle inspection, provide manufacturers with the tools to detect defects that could compromise product integrity. By identifying issues early in the production process, companies can prevent the occurrence of faulty products reaching the market. This proactive approach to quality management minimizes waste, reduces costs associated with recalls, and maintains consumer trust in Japanese-made products.
Integration of NDI in Procurement and Purchasing Processes
Incorporating NDI into procurement and purchasing processes offers significant advantages. Procurement teams can specify NDI requirements when selecting suppliers, ensuring that all incoming materials meet predefined quality standards. This integration facilitates better supplier relationships, as manufacturers work collaboratively with suppliers to maintain consistent quality. Additionally, having robust NDI protocols in place allows for more accurate forecasting and inventory management, as the reliability of materials is assured.
Advantages of Non-Destructive Inspection Techniques
Non-destructive inspection techniques offer a multitude of benefits to the manufacturing sector. These advantages not only enhance product quality but also contribute to operational efficiency and cost savings.
Enhancing Product Quality
NDI ensures that every component meets strict quality criteria without compromising the material’s integrity. This thorough inspection process guarantees that products are free from hidden defects, leading to higher durability and performance. Enhanced product quality strengthens brand reputation and customer satisfaction, which are critical factors in competitive markets.
Reducing Production Costs
By identifying defects early, NDI helps in minimizing waste and reducing the costs associated with rework or scrap materials. Early detection of issues allows for timely corrective actions, preventing the escalation of minor problems into major defects. This cost-effective approach not only improves the bottom line but also enhances overall production efficiency.
Facilitating Compliance with Industry Standards
Adhering to industry standards is essential for manufacturers, especially when exporting products globally. NDI techniques ensure compliance with international quality standards, thereby facilitating smoother market entry and acceptance. This compliance is particularly important in sectors such as automotive, aerospace, and electronics, where stringent quality requirements are non-negotiable.
Disadvantages of Non-Destructive Inspection Techniques
While NDI offers significant benefits, there are also challenges and limitations associated with its implementation. Understanding these disadvantages is crucial for manufacturers to make informed decisions.
High Initial Investment
The adoption of NDI technologies often requires substantial upfront investment in specialized equipment and training. This financial barrier can be a hindrance for smaller manufacturers or those looking to adopt advanced inspection methods for the first time.
Technical Expertise Required
Effective utilization of NDI techniques demands a high level of technical expertise. Manufacturers must invest in training personnel or hiring skilled professionals to operate and interpret the results of NDI equipment accurately. This requirement can add to the operational complexity and cost.
Limitations in Detecting Certain Defects
While NDI is highly effective in identifying many types of defects, it may not be suitable for all materials or defect types. Certain subtle or internal flaws might escape detection, necessitating the use of complementary inspection methods to ensure comprehensive quality assurance.
Supplier Negotiation Techniques for Incorporating NDI
Negotiating with suppliers to incorporate NDI into their processes requires strategic approaches. Effective negotiation ensures that suppliers understand and comply with quality expectations while maintaining mutually beneficial relationships.
Evaluating Supplier Capabilities
Before entering negotiations, it is essential to assess a supplier’s existing NDI capabilities. This evaluation includes reviewing their inspection processes, equipment used, and the expertise of their personnel. Understanding a supplier’s strengths and weaknesses allows for more focused and productive negotiations.
Negotiating Terms and Conditions
During negotiations, clearly outline the specific NDI requirements and standards that suppliers must adhere to. This includes defining acceptable defect levels, inspection frequency, and reporting protocols. Establishing these terms ensures that suppliers are aware of expectations and committed to maintaining quality standards.
Fostering Collaborative Relationships
Building a collaborative relationship with suppliers can lead to better compliance with NDI requirements. Encourage open communication and provide support for suppliers to upgrade their NDI capabilities if necessary. This collaborative approach fosters trust and long-term partnerships focused on continuous quality improvement.
Market Conditions and Trends in NDI for Japanese Manufacturing
The market for NDI is evolving rapidly, influenced by technological advancements and changing industry demands. Understanding current market conditions and trends is essential for manufacturers to stay competitive.
Technological Advancements
Recent advancements in NDI technologies, such as digital imaging and automated inspection systems, have enhanced the accuracy and efficiency of non-destructive inspections. These innovations enable faster detection of defects and reduce the reliance on manual inspection processes, leading to improved productivity.
Increased Demand for Quality Assurance
As consumer expectations for high-quality products continue to rise, manufacturers are placing greater emphasis on quality assurance. This trend drives the adoption of sophisticated NDI techniques to ensure that products meet or exceed quality standards, particularly in sectors where safety and reliability are critical.
Globalization and Supply Chain Complexity
Global supply chains have become more complex, with materials and components sourced from diverse geographical locations. This complexity necessitates robust NDI processes to manage the quality of materials coming from various suppliers, ensuring consistency and reliability across the entire supply chain.
Best Practices for Implementing NDI in Procurement
To maximize the benefits of NDI, manufacturers should adopt best practices that integrate inspection techniques seamlessly into procurement processes. These practices ensure that quality is maintained without disrupting operational efficiency.
Establish Clear NDI Standards
Define and document clear NDI standards that suppliers must meet. These standards should align with industry benchmarks and be communicated effectively to all suppliers. Clear standards provide a foundation for consistent quality and facilitate easier evaluation of supplier compliance.
Invest in Training and Development
Provide comprehensive training for procurement and quality assurance teams on NDI techniques and their importance. Skilled personnel are better equipped to assess supplier capabilities, interpret inspection results, and collaborate with suppliers to address quality issues.
Implement Regular Audits and Assessments
Conduct regular audits of suppliers to ensure ongoing compliance with NDI standards. These assessments help identify potential issues early and provide opportunities for continuous improvement. Regular audits also reinforce the importance of quality and encourage suppliers to maintain high inspection standards.
Leverage Technology for Monitoring and Reporting
Utilize advanced software and digital tools to monitor and report on NDI processes. Technology can streamline data collection, enhance accuracy in reporting, and provide real-time insights into quality metrics. Effective use of technology facilitates better decision-making and fosters a culture of transparency and accountability.
Conclusion
Non-destructive inspection techniques have significantly impacted Japanese manufacturing by enhancing quality control, reducing costs, and ensuring compliance with stringent industry standards. Integrating NDI into procurement and purchasing processes equips manufacturers with the tools to maintain high-quality standards while fostering strong supplier relationships. Despite the challenges of initial investments and the need for specialized expertise, the advantages of NDI make it an indispensable component of modern manufacturing practices. By adopting best practices and staying abreast of market trends, Japanese manufacturers can continue to lead in quality and innovation, securing their position in the global marketplace.
資料ダウンロード
QCD調達購買管理クラウド「newji」は、調達購買部門で必要なQCD管理全てを備えた、現場特化型兼クラウド型の今世紀最高の購買管理システムとなります。
ユーザー登録
調達購買業務の効率化だけでなく、システムを導入することで、コスト削減や製品・資材のステータス可視化のほか、属人化していた購買情報の共有化による内部不正防止や統制にも役立ちます。
NEWJI DX
製造業に特化したデジタルトランスフォーメーション(DX)の実現を目指す請負開発型のコンサルティングサービスです。AI、iPaaS、および先端の技術を駆使して、製造プロセスの効率化、業務効率化、チームワーク強化、コスト削減、品質向上を実現します。このサービスは、製造業の課題を深く理解し、それに対する最適なデジタルソリューションを提供することで、企業が持続的な成長とイノベーションを達成できるようサポートします。
オンライン講座
製造業、主に購買・調達部門にお勤めの方々に向けた情報を配信しております。
新任の方やベテランの方、管理職を対象とした幅広いコンテンツをご用意しております。
お問い合わせ
コストダウンが利益に直結する術だと理解していても、なかなか前に進めることができない状況。そんな時は、newjiのコストダウン自動化機能で大きく利益貢献しよう!
(Β版非公開)