- お役立ち記事
- 「製造業DXを加速する非破壊検査技術の最新トレンドと革新」
「製造業DXを加速する非破壊検査技術の最新トレンドと革新」
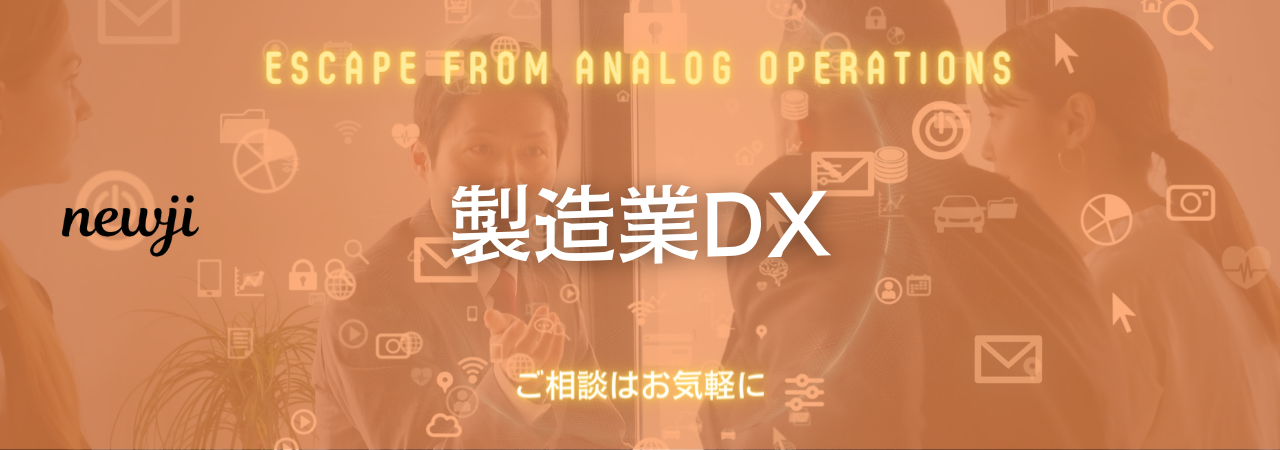
目次
非破壊検査技術とは
非破壊検査の基本概念
非破壊検査(Non-Destructive Testing, NDT)は、製品や材料の内部や表面に存在する欠陥や異常を、製品を損傷させることなく検出・評価する手法です。これにより、製品の品質を確保しながら、製造プロセスの効率化やコスト削減が可能となります。非破壊検査は航空宇宙、自動車、電子機器など多岐にわたる製造業で広く活用されています。
非破壊検査の主な手法
非破壊検査の手法は多岐にわたりますが、主に以下のような方法があります。
– 超音波検査: 高周波の音波を用いて材料内部の欠陥を検出します。
– X線・ガンマ線検査: 放射線を利用して材料の内部構造を可視化します。
– 磁粉検査: 磁性材料に適用し、表面や近表面の欠陥を検出します。
– 渦電流検査: 電磁誘導を利用して導電性材料の欠陥を検出します。
– 赤外線サーモグラフィー: 発熱や冷却のパターンから欠陥を特定します。
各手法は材料や検査対象に応じて選択され、最適な検査結果を得るために組み合わせて使用されることもあります。
製造業における非破壊検査の役割
品質管理と不良品の低減
非破壊検査は、製品の品質管理において欠かせない役割を果たします。製造過程や完成品に対して定期的に検査を行うことで、欠陥や不良品を早期に発見し、製品の信頼性を高めることができます。これにより、リコールや品質トラブルのリスクを低減し、顧客満足度の向上につながります。
生産効率の向上
非破壊検査を適切に導入することで、生産ラインの停止時間を最小限に抑えつつ、効率的な検査が可能となります。リアルタイムでの欠陥検出や自動化された検査プロセスにより、生産速度を維持しながら高精度な品質管理が実現します。結果として、生産効率全体の向上が期待できます。
コスト削減と持続可能性
不良品の削減や再加工の回避によって、製造コストの削減が可能です。また、無駄な材料の使用を避けることで、環境への負荷も軽減されます。持続可能な製造プロセスの実現に向けて、非破壊検査技術の導入は重要なステップとなります。
最新の非破壊検査技術のトレンド
超音波検査の進化
超音波検査技術は、最近では高精度化と高速化が進んでいます。特に、フェーズドアレイ超音波検査や時差超音波検査など、新しい方式が開発され、複雑な形状や厚みを持つ材料でも高精度な検査が可能となっています。また、デジタル信号処理技術の導入により、検査データの解析精度が向上し、欠陥の検出率が高まっています。
X線・ガンマ線検査の革新
X線やガンマ線を用いた検査技術も進化を遂げています。デジタルX線イメージングの普及により、従来のフィルムベースの検査よりも迅速かつ高精度な検査が可能となりました。また、コンピュータ断層撮影(CT)技術の導入により、材料内部の三次元的な欠陥解析が可能となり、複雑な構造物の詳細な検査が実現しています。
電気抵抗法・誘電率測定の活用
電気抵抗法や誘電率測定を活用した非破壊検査技術が注目されています。これらの技術は、材料の電気的特性の変化を検出することで、微細な欠陥や変質を早期に発見することが可能です。特に、半導体や電子機器の製造において、微細加工技術の向上に伴い、これらの手法の需要が高まっています。
赤外線サーモグラフィーの進展
赤外線サーモグラフィーは、材料の熱的特性を検査対象とする手法です。近年では、高感度なセンサーや高速データ処理技術の進展により、より高精度な温度分布の可視化が可能となっています。これにより、熱による応力や構造的な欠陥の検出が容易になり、エネルギー効率の向上や製品寿命の延長に寄与しています。
AIと機械学習の統合
人工知能(AI)や機械学習を非破壊検査技術に統合することで、検査プロセスの自動化と精度向上が実現されています。AIを活用した画像解析やパターン認識技術により、複雑な欠陥の検出や分類が自動的に行われ、高精度な検査結果が得られます。また、ビッグデータ解析を通じて、検査データの蓄積と分析が進み、予知保全や製造プロセスの最適化にも活用されています。
デジタル化がもたらす非破壊検査の変革
データ収集と解析の自動化
デジタル化により、非破壊検査のデータ収集と解析が自動化されています。センサーやIoTデバイスを活用することで、大量の検査データをリアルタイムで収集し、クラウド上でのデータ解析が可能となっています。これにより、検査効率が向上するとともに、人的エラーの低減が実現しています。
リアルタイムモニタリングとIoTの活用
IoT技術を活用したリアルタイムモニタリングにより、製造プロセス中の製品状態を常時監視することができます。センサーからのリアルタイムデータを基に、即時に問題を検出し、迅速な対応が可能となります。これにより、製造ラインのダウンタイムを最小限に抑えつつ、高品質な製品の安定的な供給が実現します。
クラウドベースの検査システム
クラウドベースの非破壊検査システムは、スケーラビリティと柔軟性を提供します。クラウド上に検査データを保存・管理することで、複数の拠点間でのデータ共有が容易となり、グローバルな製造プロセスの統合が可能です。また、クラウドベースのAIツールを利用することで、高度なデータ解析や予測分析が実現し、製造業全体の競争力向上につながります。
非破壊検査技術の導入事例
自動車業界における適用例
自動車業界では、非破壊検査技術が広範に活用されています。エンジン部品やフレームの欠陥検出、溶接部の品質確認など、多岐にわたる領域で非破壊検査が欠かせません。最近では、AIを活用した画像解析技術が導入され、不良品の検出精度が向上しています。また、リアルタイムモニタリングシステムにより、生産ラインの効率化が進められています。
航空宇宙産業での活用事例
航空宇宙産業では、安全性が最優先されるため、非破壊検査技術の導入が欠かせません。エンジンや機体構造部品の徹底的な検査により、微細な欠陥や損傷を早期に発見し、重大な事故を未然に防ぐ役割を果たしています。最近では、ドローン搭載型の検査装置や、3Dイメージング技術が導入され、より包括的な検査が可能となっています。
電子機器製造におけるケーススタディ
電子機器製造においても、非破壊検査技術は不可欠です。半導体チップの欠陥検出や、プリント基板の微細な亀裂の発見など、高度な検査が求められます。特に、微細化が進む電子部品に対しては、従来の検査手法では不十分な場合が多く、最新の非破壊検査技術の導入が進んでいます。例えば、X線CTを用いた3D検査や、赤外線サーモグラフィーを利用した内部構造の可視化が行われています。
非破壊検査技術のメリットとデメリット
メリット
非破壊検査技術には、以下のようなメリットがあります。
– 製品や材料を破壊せずに検査が可能であるため、製品寿命を延ばすことができる。
– 早期に欠陥を発見できるため、品質管理が向上し、不良品の削減につながる。
– 自動化やデジタル化により、検査効率が向上し、生産性が高まる。
– 環境負荷の低減やコスト削減に寄与する。
デメリット
一方で、非破壊検査技術には以下のようなデメリットも存在します。
– 高度な技術や専門知識が必要なため、熟練した技術者の確保が課題となる。
– 初期導入コストが高く、中小企業にとっては導入のハードルが高い場合がある。
– 一部の検査手法では、特定の材料や欠陥に対して適用が難しい場合がある。
– 検査結果の解釈において、誤判断が発生するリスクがある。
導入時の注意点
非破壊検査技術を導入する際には、以下の点に注意する必要があります。
– 適切な手法を選定し、検査対象や目的に合わせた技術を採用する。
– 技術者の教育・訓練を十分に行い、検査精度を維持する。
– 初期コストだけでなく、長期的な運用コストやメンテナンス費用も考慮に入れる。
– データ管理やセキュリティ対策を講じ、検査データの保護を徹底する。
今後の非破壊検査技術の展望
技術革新の方向性
非破壊検査技術は、今後も技術革新が続くと予想されます。高精度なセンサーの開発や、AIを活用した高度な解析手法の導入により、検査精度の向上が見込まれます。また、ポータブルな検査装置の開発や、より迅速な検査手法の確立により、製造現場での柔軟な活用が進むと考えられます。
製造業DXとのさらなる融合
製造業のDX(デジタルトランスフォーメーション)との融合が進む中で、非破壊検査技術もデジタル化が進展します。クラウドベースのシステムやIoTデバイスとの連携により、検査データのリアルタイム共有や遠隔監視が可能となり、グローバルな製造ネットワークの効率化が図られます。さらに、ビッグデータ解析を通じた製品改善や予知保全の実現も期待されます。
持続可能な製造プロセスへの貢献
環境への配慮が求められる現代において、非破壊検査技術は持続可能な製造プロセスの実現に寄与します。材料の無駄を減らし、リサイクルの効率を高めることで、資源の有効活用が促進されます。また、エネルギー効率の向上や廃棄物の削減にも繋がり、製造業全体の環境負荷を低減することが可能です。
Conclusion
非破壊検査技術の進化とデジタル化は、製造業のDXを加速させ、製品の品質向上や生産効率の向上、コスト削減に大きく寄与しています。最新の技術動向を把握し、適切に導入・活用することで、製造現場の競争力を高めることが可能です。今後も非破壊検査技術は進化を続け、持続可能な製造プロセスの実現に向けて重要な役割を果たすことでしょう。
資料ダウンロード
QCD調達購買管理クラウド「newji」は、調達購買部門で必要なQCD管理全てを備えた、現場特化型兼クラウド型の今世紀最高の購買管理システムとなります。
ユーザー登録
調達購買業務の効率化だけでなく、システムを導入することで、コスト削減や製品・資材のステータス可視化のほか、属人化していた購買情報の共有化による内部不正防止や統制にも役立ちます。
NEWJI DX
製造業に特化したデジタルトランスフォーメーション(DX)の実現を目指す請負開発型のコンサルティングサービスです。AI、iPaaS、および先端の技術を駆使して、製造プロセスの効率化、業務効率化、チームワーク強化、コスト削減、品質向上を実現します。このサービスは、製造業の課題を深く理解し、それに対する最適なデジタルソリューションを提供することで、企業が持続的な成長とイノベーションを達成できるようサポートします。
オンライン講座
製造業、主に購買・調達部門にお勤めの方々に向けた情報を配信しております。
新任の方やベテランの方、管理職を対象とした幅広いコンテンツをご用意しております。
お問い合わせ
コストダウンが利益に直結する術だと理解していても、なかなか前に進めることができない状況。そんな時は、newjiのコストダウン自動化機能で大きく利益貢献しよう!
(Β版非公開)