- お役立ち記事
- Best practices for purchasing departments to promote efficiency in material procurement
Best practices for purchasing departments to promote efficiency in material procurement
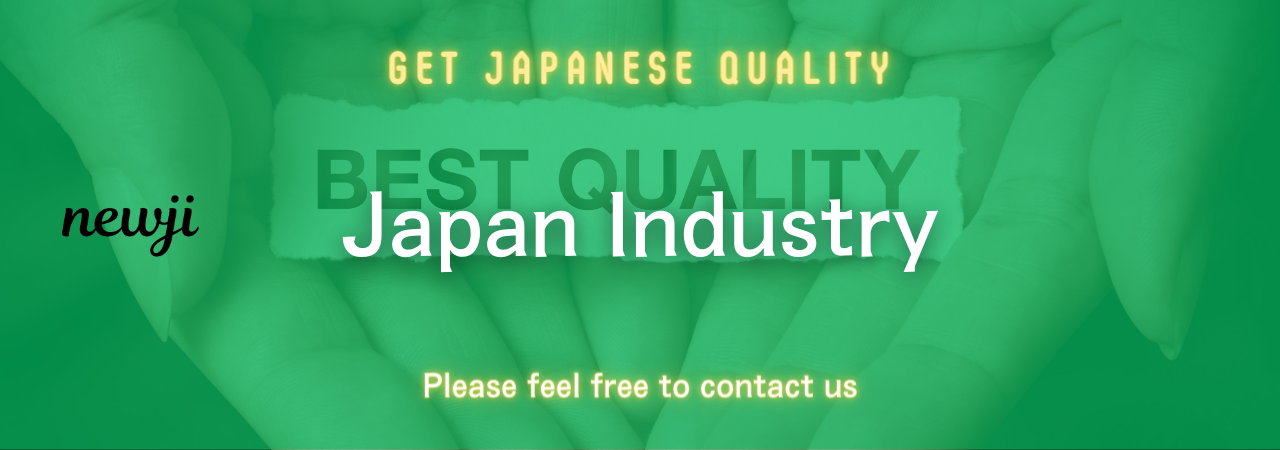
目次
Understanding the Role of a Purchasing Department
The purchasing department plays a crucial role in any organization, as it is responsible for acquiring the materials and services necessary for the company’s operations.
This department ensures that the procurement process is efficient, cost-effective, and timely, thereby playing a significant part in maintaining the company’s competitiveness and profitability.
To promote efficiency, the purchasing department must focus on strategic procurement practices that streamline processes and enhance productivity.
Setting Clear Procurement Objectives
One of the best practices for purchasing departments is to establish clear procurement objectives.
These objectives should align with the organization’s overall mission and goals.
Specific objectives may include cost reduction, quality improvement, timely delivery, supplier relationship management, and risk mitigation.
By setting clear objectives, the department can focus its efforts on those areas that will have the most significant impact on the organization.
Regularly reviewing and updating these objectives is also essential to accommodate changing market dynamics and organizational needs.
Leveraging Technology for Better Procurement
In today’s digital age, technology offers a plethora of tools that can significantly enhance procurement efficiency.
Purchasing departments should leverage procurement software solutions for tasks such as order processing, supplier management, contract management, and inventory control.
These software solutions help automate routine tasks, reduce errors, and provide valuable data insights to make informed decisions.
Moreover, adopting e-procurement platforms allows for a more streamlined procurement process, with improved transparency and communication between suppliers and buyers.
By utilizing technology, purchasing departments can save time, cut costs, and ultimately improve their overall efficiency.
Building Strong Supplier Relationships
Effective supplier relationship management is another vital practice for promoting efficiency in material procurement.
Purchasing departments should aim to build strong, collaborative relationships with their suppliers.
This involves regular communication, understanding their suppliers’ capabilities and limitations, and working together towards mutually beneficial goals.
Maintaining positive supplier relationships can lead to better terms, improved reliability, and access to innovations.
In addition, by developing strategic partnerships with key suppliers, the purchasing department can create a more resilient supply chain, better equipped to handle disruptions.
Emphasizing Training and Development
A skilled workforce is essential for the efficient functioning of the purchasing department.
Investing in training and development programs ensures that procurement professionals are well-equipped with the latest industry knowledge, best practices, and technological tools.
Continual learning can lead to improved negotiation skills, better supplier management, and more effective cost-control strategies.
Encouraging professional certifications and attending industry conferences can also help keep the team updated with the latest trends and developments in procurement.
This commitment to training not only ensures a higher level of performance but also contributes to the overall growth and success of the organization.
Implementing a Centralized Procurement Strategy
A centralized procurement strategy can greatly improve the efficiency of the purchasing department.
By consolidating purchasing activities across the organization, the department can achieve economies of scale, reduce redundancies, and standardize processes.
A centralized approach allows for better coordination among different business units and provides a cohesive strategy for negotiating with suppliers.
It also enhances visibility into the procurement process, making it easier to identify and address any inefficiencies.
However, it is crucial to maintain flexibility within this centralized system to accommodate the unique needs of different departments.
Focusing on Total Cost of Ownership
When assessing procurement efficiency, it is important to consider the total cost of ownership (TCO) rather than just the purchase price.
TCO encompasses all costs associated with acquiring, maintaining, and disposing of a product or service over its life cycle.
By focusing on TCO, the purchasing department can make more informed decisions that lead to long-term savings.
This approach encourages procurement professionals to consider factors such as quality, durability, vendor support, and potential hidden costs that may arise after purchase.
Evaluating TCO allows the department to make strategic choices that contribute to the overall efficiency and financial health of the organization.
Enhancing Supplier Performance Monitoring
To ensure that suppliers are consistently meeting performance expectations, purchasing departments should establish a robust supplier performance monitoring system.
This involves setting key performance indicators (KPIs) to evaluate supplier delivery, quality, cost, and service.
Regular assessments can help identify areas of improvement and promote continuous enhancement of supplier performance.
Sharing performance data with suppliers can foster transparency and encourage them to meet or exceed expectations.
By enhancing supplier performance monitoring, purchasing departments can minimize disruptions, reduce costs, and improve the efficiency of their supply chain operations.
Encouraging Cross-Functional Collaboration
Cross-functional collaboration is vital for improving the efficiency of material procurement.
Purchasing departments should work closely with other departments, such as finance, operations, and quality control, to ensure alignment of goals and objectives.
By fostering collaboration, the department can gain insights into the specific needs of other departments, which can lead to a more tailored and efficient procurement process.
Collaboration also enables the sharing of information and resources, which can result in better decision-making and a stronger, more unified organization.
Conclusion
In conclusion, purchasing departments play a critical role in promoting efficiency in material procurement.
By implementing best practices such as setting clear objectives, leveraging technology, building strong supplier relationships, and focusing on total cost of ownership, the department can create a more efficient and cost-effective procurement process.
Through continuous training and development, centralized strategies, performance monitoring, and cross-functional collaboration, purchasing professionals can drive improvement and innovation within the organization.
Adopting these best practices ensures that the purchasing department remains a vital contributor to the overall success and competitiveness of the business.
資料ダウンロード
QCD調達購買管理クラウド「newji」は、調達購買部門で必要なQCD管理全てを備えた、現場特化型兼クラウド型の今世紀最高の購買管理システムとなります。
ユーザー登録
調達購買業務の効率化だけでなく、システムを導入することで、コスト削減や製品・資材のステータス可視化のほか、属人化していた購買情報の共有化による内部不正防止や統制にも役立ちます。
NEWJI DX
製造業に特化したデジタルトランスフォーメーション(DX)の実現を目指す請負開発型のコンサルティングサービスです。AI、iPaaS、および先端の技術を駆使して、製造プロセスの効率化、業務効率化、チームワーク強化、コスト削減、品質向上を実現します。このサービスは、製造業の課題を深く理解し、それに対する最適なデジタルソリューションを提供することで、企業が持続的な成長とイノベーションを達成できるようサポートします。
オンライン講座
製造業、主に購買・調達部門にお勤めの方々に向けた情報を配信しております。
新任の方やベテランの方、管理職を対象とした幅広いコンテンツをご用意しております。
お問い合わせ
コストダウンが利益に直結する術だと理解していても、なかなか前に進めることができない状況。そんな時は、newjiのコストダウン自動化機能で大きく利益貢献しよう!
(Β版非公開)