- お役立ち記事
- Challenges faced by purchasing departments in shortening the material procurement process and how to deal with them
Challenges faced by purchasing departments in shortening the material procurement process and how to deal with them
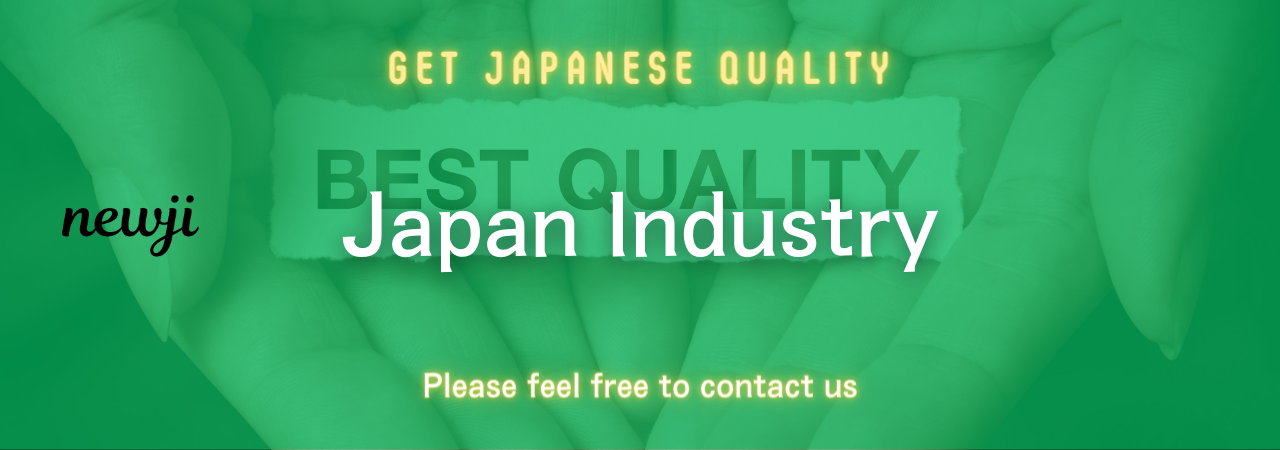
目次
Understanding the Procurement Process
The procurement process is a series of vital steps that purchasing departments undertake to acquire goods and services needed for a company’s operations.
It involves identifying needs, selecting suppliers, negotiating contracts, and ensuring timely delivery.
Each step is crucial for maintaining efficiency and cost-effectiveness.
However, the process can be lengthy and fraught with challenges, especially when it comes to shortening procurement timelines without compromising quality or cost.
Key Challenges in Material Procurement
1. Supplier Reliability and Lead Times
One of the primary challenges purchasing departments face is ensuring supplier reliability.
Unreliable suppliers can lead to delays, impacting the entire production schedule.
Long lead times also pose a significant barrier in shortening the procurement process.
Manufacturers often have complex supply chains requiring coordination among multiple suppliers, which can complicate efforts to compress timelines.
2. Balancing Cost and Quality
Another challenge is maintaining a balance between cost and quality.
In attempts to shorten procurement times, companies might be tempted to compromise on quality, which could result in subpar products.
However, decreasing quality can lead to customer dissatisfaction and potential financial losses in the long term.
3. Inefficient Internal Processes
Inefficiencies within a company’s own processes can also stall procurement efforts.
Bureaucratic hurdles, such as extensive approval procedures and outdated systems, can slow down the procurement cycle significantly.
Streamlining internal processes is crucial for speeding up procurement without sacrificing accuracy or efficacy.
4. Demand Forecasting and Inventory Management
Accurate demand forecasting and effective inventory management are essential for a smooth procurement process.
Errors in forecasting can lead to overstocking or understocking, both of which are costly.
These mistakes compound when they delay the procurement cycle, making it difficult to be responsive to market changes.
5. Compliance and Regulatory Issues
Adhering to compliance and regulatory requirements is vital, yet often slows down procurement.
The need to ensure all materials meet legal standards can introduce additional steps in the procurement process, adding time and complexity.
Strategies to Shorten Procurement Timelines
1. Supplier Relationship Management
Building strong relationships with reliable suppliers is a critical strategy for overcoming procurement challenges.
Developing partnerships with suppliers can help ensure timely delivery, improve communication, and foster collaboration for problem-solving.
Regular reviews and audits of supplier performance can also preempt potential delays.
2. Implementing Technology and Automation
Leveraging technology is essential for streamlining procurement processes.
Automated systems can manage repetitive tasks, handle data more efficiently, and reduce human error.
Using software solutions for tasks like order tracking, inventory management, and supplier evaluation can significantly cut down on processing times.
3. Streamlining Internal Procedures
Evaluating and adjusting internal processes is crucial for efficiency.
Implementing lean management techniques can eliminate redundant steps and reduce approval layers.
Establishing clear communication channels and providing procurement teams with clear guidelines can also aid in speeding up the process.
4. Enhancing Forecasting and Inventory Systems
Improving demand forecasting accuracy can shorten procurement times by aligning inventories with actual needs.
Using advanced data analytics and forecasting tools can provide better insights into market demands and help maintain optimal inventory levels.
Regularly reviewing and updating inventory management strategies ensures alignment with current business goals.
5. Proactive Compliance Management
Staying informed about regulatory changes and incorporating compliance checks early in the procurement process can prevent delays.
A proactive approach ensures that procurement practices are always aligned with current laws, minimizing disruptions.
Conclusion
Shortening the material procurement process is a challenging task that involves navigating through various hurdles, from supplier reliability to compliance issues.
However, by employing strategic measures such as building strong supplier relationships, utilizing technology, optimizing internal processes, improving forecasting, and staying compliant with regulations, purchasing departments can effectively reduce procurement timelines.
These strategies not only streamline operations but also contribute to achieving competitive advantages in the marketplace by ensuring products are delivered efficiently and cost-effectively.
資料ダウンロード
QCD調達購買管理クラウド「newji」は、調達購買部門で必要なQCD管理全てを備えた、現場特化型兼クラウド型の今世紀最高の購買管理システムとなります。
ユーザー登録
調達購買業務の効率化だけでなく、システムを導入することで、コスト削減や製品・資材のステータス可視化のほか、属人化していた購買情報の共有化による内部不正防止や統制にも役立ちます。
NEWJI DX
製造業に特化したデジタルトランスフォーメーション(DX)の実現を目指す請負開発型のコンサルティングサービスです。AI、iPaaS、および先端の技術を駆使して、製造プロセスの効率化、業務効率化、チームワーク強化、コスト削減、品質向上を実現します。このサービスは、製造業の課題を深く理解し、それに対する最適なデジタルソリューションを提供することで、企業が持続的な成長とイノベーションを達成できるようサポートします。
オンライン講座
製造業、主に購買・調達部門にお勤めの方々に向けた情報を配信しております。
新任の方やベテランの方、管理職を対象とした幅広いコンテンツをご用意しております。
お問い合わせ
コストダウンが利益に直結する術だと理解していても、なかなか前に進めることができない状況。そんな時は、newjiのコストダウン自動化機能で大きく利益貢献しよう!
(Β版非公開)