- お役立ち記事
- Practical guide to risk management for purchasing departments aiming to stabilize material supply
Practical guide to risk management for purchasing departments aiming to stabilize material supply
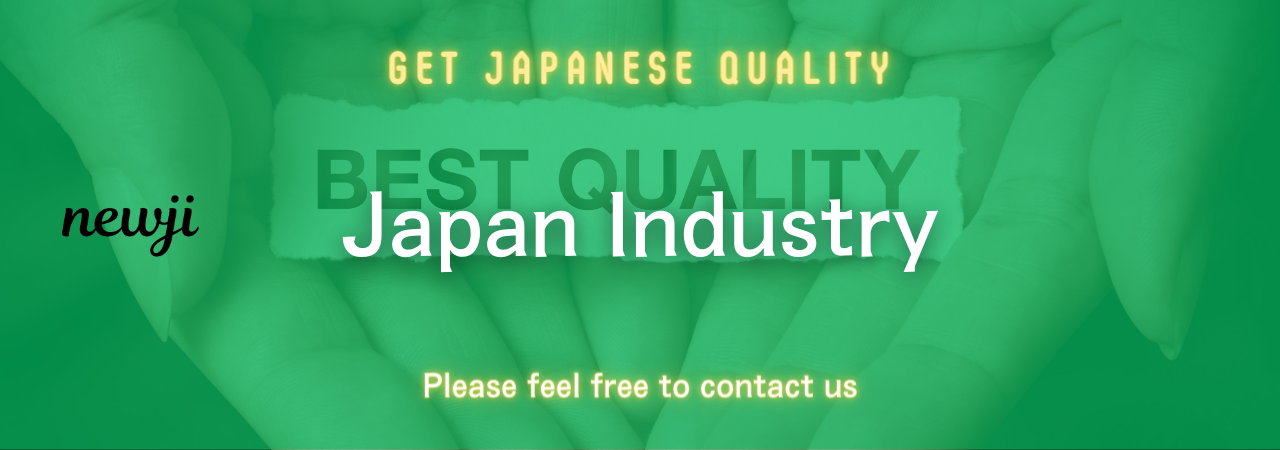
目次
Understanding Risk Management in Purchasing
In today’s fast-paced business environment, ensuring a stable supply of materials is crucial for the smooth operation of any company.
The purchasing department plays a vital role in managing risks associated with sourcing and supply chain disruptions.
By employing effective risk management strategies, purchasing departments can minimize potential threats and maintain the continuous flow of materials.
But what does risk management entail for purchasing departments, and how can they effectively stabilize material supply?
The Importance of Risk Management
Risk management is the identification, assessment, and prioritization of risks followed by coordinated efforts to minimize, monitor, and control the probability of unfortunate events.
For purchasing departments, risk management is essential to withstand various uncertainties that affect supply chains, including market fluctuations, geopolitical tensions, natural disasters, and supplier insolvency.
By focusing on these strategies, companies can safeguard against potential losses, reduce downtime, and ensure that production schedules remain uninterrupted.
Identifying and Assessing Risks
Before implementing any risk management strategy, it is vital for purchasing departments to identify and assess potential risks.
Thorough evaluation of the supply chain can reveal vulnerabilities that might impact material supply.
Supplier Evaluation
One of the most important steps in risk management is assessing the reliability and stability of suppliers.
Purchasing departments should conduct regular evaluations to ensure that suppliers comply with quality standards, financial stability, and delivery capabilities.
Diversifying the supplier base can also mitigate risks, as reliance on a single source can make a company more susceptible to supply disruptions.
Market Analysis
Understanding market trends and fluctuations is crucial for purchasing departments.
Keeping a pulse on market dynamics allows companies to anticipate price changes and potential shortages.
Regular market analysis enables purchasing teams to make informed decisions and develop strategies to address market-related risks.
Supply Chain Mapping
Mapping the supply chain helps identify critical points that might pose risks to material supply.
By having a clear understanding of the entire supply chain, from raw material suppliers to end consumers, companies can pinpoint areas that require closer monitoring and contingency plans.
Developing Risk Mitigation Strategies
Once risks are identified and assessed, purchasing departments should develop strategies to mitigate these risks.
Implementation of comprehensive risk mitigation strategies ensures that any disruptions have minimal impact on material supply.
Building Strong Supplier Relationships
Establishing strong, long-term relationships with suppliers is fundamental to risk management.
Open communication and collaboration with suppliers can lead to better problem-solving and faster response times to unforeseen disruptions.
Consider developing contracts that outline specific risks and the responsibilities of both parties in mitigating them.
Inventory Management
Effective inventory management can prevent production delays and buffer against supply chain disruptions.
Maintaining strategic stock reserves or using just-in-time inventory systems can help ensure there is always a backup of essential materials.
By carefully planning and managing inventory levels, companies can avoid overstocking or running out of critical supplies.
Flexibility and Contingency Planning
Flexibility in sourcing and having contingency plans in place enable companies to respond promptly to disruptions.
Consider identifying alternative suppliers and logistics solutions that can be activated when necessary.
Developing a contingency plan allows the purchasing department to maintain operations in the face of unexpected events.
Embracing Technology for Risk Management
Incorporating technology into risk management processes can enhance the effectiveness and efficiency of a purchasing department’s risk mitigation strategies.
Data Analytics and Forecasting Tools
Utilizing data analytics and forecasting tools can help identify trends and predict potential risks before they have a significant impact.
These tools enable purchasing departments to make data-driven decisions and plan more effectively.
Analyzing historical and real-time data provides insights into risk patterns and enables proactive management.
Supply Chain Management Software
Implementing supply chain management software can streamline processes across the supply chain.
These solutions provide visibility into every aspect of the supply chain, improving the ability to identify risks and respond swiftly.
Automation tools can also reduce human error and increase overall efficiency in managing the supply chain.
Blockchain Technology
Blockchain technology offers transparent and secure tracking of transactions and goods throughout the supply chain.
Its ability to provide a tamper-proof, real-time record of movements can enhance trust and coordination between purchasers and suppliers.
Continuous Improvement and Monitoring
Risk management in purchasing is an ongoing process that requires continuous monitoring and improvement.
Regularly revisiting risk management strategies allows companies to adapt to changes in the supply chain landscape and improve upon existing practices.
Regular Risk Assessments
Conducting periodic risk assessments ensures that any emerging risks are promptly identified and addressed.
As the business environment and supply chain dynamics evolve, continuous evaluation of risks will help keep mitigation strategies relevant and effective.
Learning from Past Disruptions
Analyzing past supply chain disruptions can provide valuable insights and lessons.
By understanding what worked well and what didn’t, purchasing departments can refine their strategies and avoid repeating mistakes.
Staff Training and Development
Investing in staff training and development ensures that purchasing teams are equipped with the necessary skills and knowledge to manage risks effectively.
Regular training on new tools, technologies, and strategies helps maintain a competent and agile purchasing department capable of tackling new challenges.
Effective risk management in purchasing departments is fundamental to stabilizing material supply and ensuring the smooth operation of a business.
By identifying and assessing risks, developing comprehensive strategies, and embracing technology, companies can effectively mitigate potential threats to their supply chains.
Continuous improvement and vigilance are key to maintaining a robust risk management framework that supports long-term business success.
資料ダウンロード
QCD調達購買管理クラウド「newji」は、調達購買部門で必要なQCD管理全てを備えた、現場特化型兼クラウド型の今世紀最高の購買管理システムとなります。
ユーザー登録
調達購買業務の効率化だけでなく、システムを導入することで、コスト削減や製品・資材のステータス可視化のほか、属人化していた購買情報の共有化による内部不正防止や統制にも役立ちます。
NEWJI DX
製造業に特化したデジタルトランスフォーメーション(DX)の実現を目指す請負開発型のコンサルティングサービスです。AI、iPaaS、および先端の技術を駆使して、製造プロセスの効率化、業務効率化、チームワーク強化、コスト削減、品質向上を実現します。このサービスは、製造業の課題を深く理解し、それに対する最適なデジタルソリューションを提供することで、企業が持続的な成長とイノベーションを達成できるようサポートします。
オンライン講座
製造業、主に購買・調達部門にお勤めの方々に向けた情報を配信しております。
新任の方やベテランの方、管理職を対象とした幅広いコンテンツをご用意しております。
お問い合わせ
コストダウンが利益に直結する術だと理解していても、なかなか前に進めることができない状況。そんな時は、newjiのコストダウン自動化機能で大きく利益貢献しよう!
(Β版非公開)