- お役立ち記事
- “Mastering Japanese Manufacturing: The Essential Guide to ‘Solder Baths'”
“Mastering Japanese Manufacturing: The Essential Guide to ‘Solder Baths'”
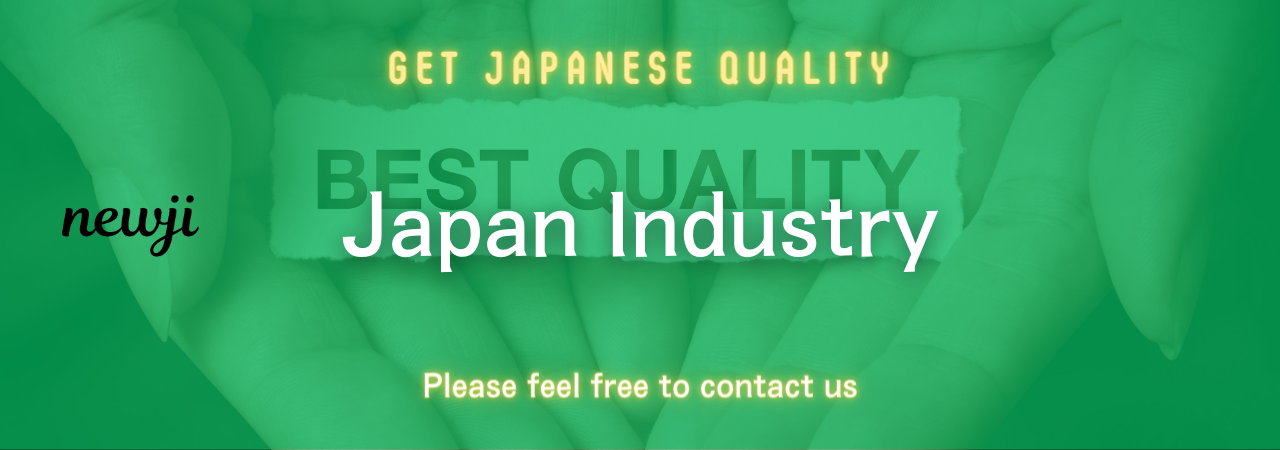
目次
Understanding Solder Baths in Japanese Manufacturing
Solder baths play a critical role in various manufacturing processes, particularly in the electronics industry. In Japanese manufacturing, the precision and efficiency of solder baths are paramount to maintaining the high standards synonymous with Japanese products. This guide delves into the essentials of solder baths, offering insights into procurement and purchasing, supplier negotiation techniques, market conditions, and best practices from a procurement and purchasing perspective.
The Role of Solder Baths in Manufacturing
Solder baths are liquid solutions composed of solder alloy used to join electronic components to circuit boards. The process involves immersing components into the molten solder, creating reliable electrical and mechanical connections. This method is favored for its consistency and ability to produce high-quality joints, which are essential for the longevity and performance of electronic devices.
Importance in Japanese Manufacturing
Japanese manufacturing is renowned for its attention to detail and commitment to quality. Solder baths align with these principles by ensuring precise and uniform soldering. The use of solder baths minimizes defects, enhances product reliability, and supports the production of complex electronic assemblies typical in industries such as automotive, consumer electronics, and telecommunications.
Advantages of Utilizing Solder Baths
Employing solder baths in manufacturing offers several advantages that contribute to improved product quality and operational efficiency.
Consistent Quality
Solder baths provide a controlled environment where temperature and solder composition can be precisely managed. This consistency results in uniform solder joints, reducing the likelihood of defects and enhancing the overall quality of the product.
Efficiency in Production
Automating the soldering process with solder baths increases production speed and throughput. This efficiency is particularly beneficial in high-volume manufacturing settings, where time and precision are critical.
Cost-Effectiveness
While the initial investment in solder bath equipment may be significant, the long-term benefits include lower labor costs and reduced waste. The ability to recycle solder and maintain consistent quality also contributes to cost savings.
Scalability
Solder baths are adaptable to various production scales, making them suitable for both small and large manufacturing operations. This scalability ensures that businesses can expand their production without compromising on quality.
Disadvantages of Solder Baths
Despite their benefits, solder baths come with certain drawbacks that manufacturers must consider.
Initial Investment
The cost of acquiring and installing solder bath equipment can be high. This investment may be a barrier for smaller manufacturers or those with limited capital.
Maintenance Requirements
Solder baths require regular maintenance to ensure optimal performance. This includes monitoring temperature, cleaning the bath, and replacing worn components, which can lead to increased operational costs.
Environmental and Safety Concerns
Handling molten solder involves risks related to high temperatures and hazardous materials. Proper safety measures and environmental controls are necessary to mitigate these risks, adding to the complexity of the manufacturing process.
Skill Requirements
Operating solder baths effectively requires skilled personnel who are trained in handling the equipment and managing the soldering process. Recruiting and retaining such talent can be challenging.
Procurement and Purchasing of Solder Bath Equipment
The procurement process for solder bath equipment involves several critical steps to ensure that manufacturers acquire the right tools to meet their production needs.
Identifying Requirements
Manufacturers must assess their specific needs, including production volume, product specifications, and quality standards. This assessment helps in selecting equipment that aligns with operational goals.
Supplier Selection
Choosing the right supplier is crucial. Factors to consider include the supplier’s reputation, quality of equipment, after-sales support, and ability to meet delivery timelines. Japanese suppliers are often preferred for their reliability and adherence to high-quality standards.
Evaluating Quality and Compliance
Ensuring that the solder bath equipment meets industry standards and certifications is essential. Compliance with safety regulations and environmental guidelines is also a key consideration.
Cost Analysis
A thorough cost analysis should be conducted, considering not only the purchase price but also installation, maintenance, and operational costs. Comparing quotes from multiple suppliers can aid in making an informed decision.
Supplier Negotiation Techniques
Effective negotiation with suppliers can lead to favorable terms and cost savings. Here are some strategies tailored for dealing with Japanese suppliers.
Building Long-Term Relationships
Japanese business culture emphasizes long-term relationships and mutual trust. Investing time in building a strong rapport with suppliers can lead to better terms and collaborative problem-solving.
Understanding Cultural Nuances
Awareness of Japanese business etiquette, such as respect, politeness, and attention to detail, can enhance negotiation outcomes. Demonstrating cultural sensitivity fosters a positive negotiation environment.
Leveraging Volume and Commitment
Committing to larger orders or long-term contracts can provide leverage in negotiations. Suppliers are more likely to offer discounts or favorable terms to customers who contribute significantly to their business.
Flexibility and Compromise
Being open to compromise on certain aspects, such as delivery schedules or payment terms, can facilitate smoother negotiations. Flexibility shows a willingness to work together towards mutually beneficial solutions.
Utilizing Local Representatives
Engaging local agents or representatives who understand the Japanese market and language can bridge communication gaps and aid in more effective negotiations.
Market Conditions for Solder Baths in Japan
Understanding the current market landscape for solder baths in Japan is vital for strategic procurement and purchasing decisions.
Demand and Supply Dynamics
Japan’s strong electronics and automotive sectors drive the demand for high-quality solder baths. The supply is characterized by advanced manufacturers who offer technologically sophisticated equipment.
Technological Advancements
Japanese manufacturers are at the forefront of innovation in solder bath technology. Trends include the development of lead-free solder baths and automation integration to enhance efficiency and environmental sustainability.
Competitive Landscape
The market features both established players and emerging companies. Competition among suppliers fosters continuous improvement and competitive pricing, benefiting manufacturers seeking solder bath solutions.
Economic Factors
Economic stability in Japan supports steady investment in manufacturing infrastructure. However, global economic fluctuations and trade policies can impact pricing and availability of solder bath equipment.
Regulatory Environment
Japan enforces strict environmental and safety regulations for manufacturing equipment. Compliance with these standards is mandatory, influencing the design and functionality of solder bath systems.
Best Practices in Managing Solder Bath Processes
Adhering to best practices ensures that solder bath operations are efficient, cost-effective, and produce high-quality results.
Regular Maintenance and Calibration
Routine maintenance and calibration of solder bath equipment are essential to maintain optimal performance. This includes cleaning the bath, checking temperature controls, and inspecting components for wear and tear.
Training and Development
Investing in the training and development of personnel ensures that operators are skilled in managing solder bath processes. Continuous education on the latest techniques and safety protocols enhances operational efficiency.
Implementing Quality Control Measures
Establishing stringent quality control measures helps in monitoring solder joints and identifying defects early. Techniques such as visual inspections, automated optical inspection (AOI), and electrical testing are commonly used.
Optimizing Solder Composition
Selecting the appropriate solder alloy composition based on application requirements is crucial. Factors such as melting point, wetting characteristics, and mechanical strength must be considered to achieve reliable joints.
Environmental Sustainability
Adopting environmentally friendly practices, such as using lead-free solder and recycling solder materials, aligns with global sustainability trends. This not only complies with regulations but also enhances the company’s reputation.
Automation and Integration
Integrating automation into solder bath processes improves consistency and reduces human error. Automated systems can manage temperature controls, immersion timings, and solder composition adjustments with precision.
Data Monitoring and Analysis
Utilizing data monitoring systems allows for real-time tracking of solder bath parameters. Analyzing this data helps in identifying trends, predicting maintenance needs, and optimizing the soldering process.
Choosing the Right Solder Bath Supplier in Japan
Selecting a reliable supplier is critical to ensuring the success of solder bath implementation in manufacturing operations.
Assessing Supplier Capabilities
Evaluate the supplier’s technical expertise, production capacity, and ability to customize solutions based on specific needs. A supplier with robust R&D capabilities is better positioned to offer innovative and efficient solder bath systems.
Checking References and Reviews
Reviewing testimonials, case studies, and obtaining references from existing customers can provide insights into the supplier’s performance and reliability.
Evaluating After-Sales Support
Post-purchase support, including installation, training, and maintenance services, is essential for the smooth operation of solder bath equipment. Ensure that the supplier offers comprehensive after-sales services.
Comparing Technological Features
Compare the technological features of different suppliers’ solder bath systems. Look for advancements such as temperature precision, automation capabilities, and user-friendly controls that align with your manufacturing needs.
Negotiating Warranty and Service Terms
Secure favorable warranty terms and service agreements to protect the investment in solder bath equipment. Clear terms regarding coverage, response times, and service procedures are important considerations.
Integration of Solder Baths into Manufacturing Processes
Successfully integrating solder baths into existing manufacturing workflows requires careful planning and coordination.
Designing the Production Line
Plan the layout of the production line to accommodate the solder bath system efficiently. Consider factors such as space, workflow, and the placement of complementary equipment.
Ensuring Compatibility
Ensure that the solder bath equipment is compatible with other components of the production process, including conveyor systems, inspection stations, and material handling equipment.
Implementing Standard Operating Procedures (SOPs)
Develop and implement SOPs for operating and maintaining solder baths. Clear procedures help in maintaining consistency, ensuring safety, and facilitating training of new personnel.
Testing and Validation
Conduct thorough testing and validation of the solder bath system before full-scale production. This includes verifying solder joint quality, equipment performance, and process stability.
Continuous Improvement
Adopt a continuous improvement approach to refine the solder bath process. Regularly review performance metrics, gather feedback, and implement changes to enhance efficiency and quality.
Case Studies: Successful Implementation of Solder Baths in Japanese Manufacturing
Examining real-world examples provides valuable insights into the practical application of solder baths in Japanese manufacturing contexts.
Case Study 1: Automotive Electronics Manufacturer
A leading Japanese automotive electronics manufacturer integrated advanced solder bath systems into their production line. By automating the soldering process, they achieved a 20% increase in production efficiency and a significant reduction in soldering defects. The collaboration with a local supplier ensured tailored solutions and responsive after-sales support, contributing to the project’s success.
Case Study 2: Consumer Electronics Company
A Japanese consumer electronics company adopted solder baths to enhance the reliability of their mobile devices. Implementing lead-free solder baths aligned with environmental regulations and improved product sustainability. The strategic partnership with the supplier facilitated knowledge transfer and technical support, enabling seamless integration and quality improvements.
Case Study 3: Telecommunications Equipment Manufacturer
A telecommunications equipment manufacturer utilized solder baths to maintain high-quality standards in their circuit board assemblies. By leveraging data monitoring systems, they optimized solder bath parameters, resulting in consistent solder joint performance and reduced maintenance downtime. The supplier’s expertise in solder bath technology played a crucial role in achieving these outcomes.
Trends and Innovations in Solder Bath Technology
Staying abreast of the latest trends and innovations helps manufacturers maintain a competitive edge in solder bath applications.
Lead-Free Soldering
The shift towards lead-free soldering is driven by environmental regulations and consumer demand for eco-friendly products. Innovations in lead-free solder alloys offer improved performance while meeting regulatory standards.
Automation and Smart Manufacturing
Integration of automation and smart technologies enhances the precision and efficiency of solder bath processes. Features such as automated temperature control, data analytics, and remote monitoring are becoming standard in modern solder bath systems.
Additive Manufacturing Integration
The combination of solder baths with additive manufacturing techniques allows for the creation of complex electronic assemblies with minimal manual intervention, enhancing both flexibility and scalability.
Advanced Materials
Development of advanced solder materials with superior thermal and mechanical properties contributes to more reliable solder joints, particularly in high-performance applications.
Environmental Sustainability Initiatives
Manufacturers are increasingly adopting sustainable practices in solder bath operations, including recycling solder materials, reducing energy consumption, and minimizing waste generation.
Challenges in Adopting Solder Baths
Despite the benefits, manufacturers may encounter several challenges when adopting solder bath technology.
High Initial Costs
The upfront investment required for solder bath equipment can be substantial, posing a financial challenge for some manufacturers, especially smaller enterprises.
Technical Complexity
Solder bath systems are complex and require specialized knowledge for operation and maintenance. This complexity can lead to operational difficulties if not managed properly.
Regulatory Compliance
Navigating the regulatory landscape related to environmental and safety standards requires diligent effort and can complicate the procurement and implementation process.
Supply Chain Disruptions
Global supply chain uncertainties, such as those caused by geopolitical tensions or pandemics, can impact the availability and cost of solder bath equipment and materials.
Resistance to Change
Organizational resistance to adopting new technologies and processes can hinder the successful implementation of solder bath systems.
Strategies to Overcome Challenges
Implementing effective strategies can help manufacturers navigate the challenges associated with solder baths.
Cost-Benefit Analysis
Conducting a thorough cost-benefit analysis helps in justifying the investment in solder bath systems by highlighting long-term savings and quality improvements.
Training and Skill Development
Investing in comprehensive training programs ensures that personnel are equipped with the necessary skills to operate and maintain solder bath equipment effectively.
Regulatory Expertise
Engaging with regulatory experts or consultants can aid in understanding and complying with relevant standards, mitigating compliance-related challenges.
Diversifying Suppliers
Establishing relationships with multiple suppliers reduces the risk of supply chain disruptions and ensures a steady supply of necessary equipment and materials.
Change Management
Implementing structured change management practices facilitates the smooth adoption of solder bath technology by addressing organizational resistance and fostering a culture of innovation.
Future Outlook for Solder Baths in Japanese Manufacturing
The future of solder baths in Japanese manufacturing is poised for growth and innovation, driven by technological advancements and evolving industry needs.
Integration with Industry 4.0
The convergence of solder bath technology with Industry 4.0 principles, such as the Internet of Things (IoT) and artificial intelligence (AI), will enhance process automation, data analytics, and overall manufacturing intelligence.
Sustainability and Environmental Focus
Increased emphasis on sustainability will drive the development of eco-friendly solder bath solutions, including the adoption of green solder materials and energy-efficient equipment.
Customization and Flexibility
Manufacturers will seek more customizable and flexible solder bath systems that can adapt to diverse production requirements and support rapid product innovation cycles.
Collaborative Partnerships
Collaborative partnerships between manufacturers and suppliers will become more prevalent, fostering innovation, knowledge sharing, and mutual growth in solder bath technology.
Advanced Quality Control
Advancements in quality control technologies, including real-time monitoring and predictive maintenance, will further enhance the reliability and performance of solder bath processes.
Conclusion
Mastering solder baths is essential for Japanese manufacturers striving to maintain high-quality standards and operational efficiency. By understanding the advantages and disadvantages, adopting effective procurement and purchasing strategies, leveraging supplier negotiation techniques, and staying informed about market conditions and best practices, manufacturers can optimize their solder bath operations. Embracing innovations and overcoming challenges will ensure that solder baths continue to play a pivotal role in the success and competitiveness of Japanese manufacturing in the global market.
資料ダウンロード
QCD調達購買管理クラウド「newji」は、調達購買部門で必要なQCD管理全てを備えた、現場特化型兼クラウド型の今世紀最高の購買管理システムとなります。
ユーザー登録
調達購買業務の効率化だけでなく、システムを導入することで、コスト削減や製品・資材のステータス可視化のほか、属人化していた購買情報の共有化による内部不正防止や統制にも役立ちます。
NEWJI DX
製造業に特化したデジタルトランスフォーメーション(DX)の実現を目指す請負開発型のコンサルティングサービスです。AI、iPaaS、および先端の技術を駆使して、製造プロセスの効率化、業務効率化、チームワーク強化、コスト削減、品質向上を実現します。このサービスは、製造業の課題を深く理解し、それに対する最適なデジタルソリューションを提供することで、企業が持続的な成長とイノベーションを達成できるようサポートします。
オンライン講座
製造業、主に購買・調達部門にお勤めの方々に向けた情報を配信しております。
新任の方やベテランの方、管理職を対象とした幅広いコンテンツをご用意しております。
お問い合わせ
コストダウンが利益に直結する術だと理解していても、なかなか前に進めることができない状況。そんな時は、newjiのコストダウン自動化機能で大きく利益貢献しよう!
(Β版非公開)