- お役立ち記事
- Utilization of alternative materials and cost reduction recommended by purchasing department
Utilization of alternative materials and cost reduction recommended by purchasing department
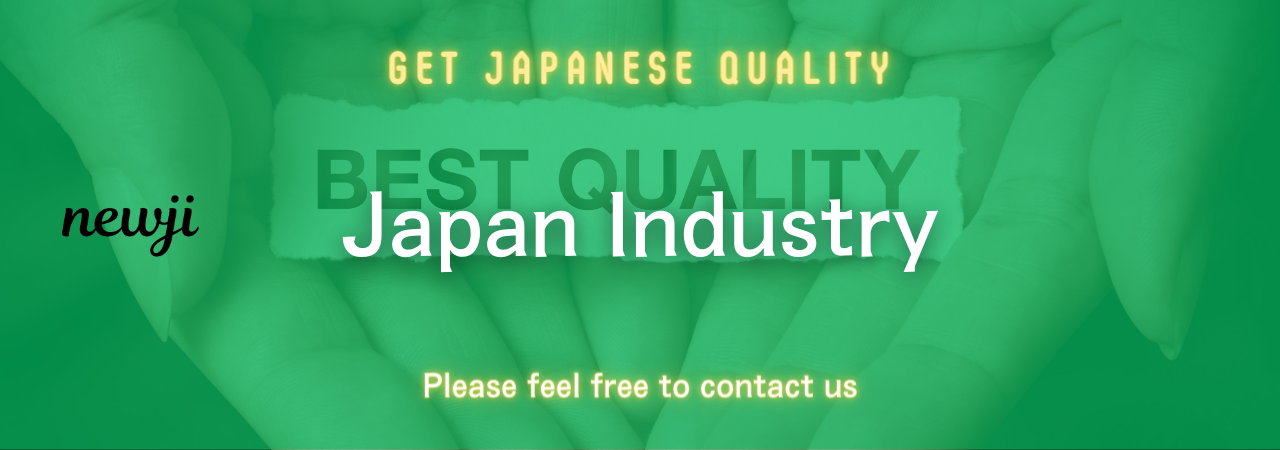
目次
Introduction to Alternative Materials
In today’s fast-paced business world, companies are continuously looking for ways to improve efficiency and reduce costs.
One significant strategy that procurement departments are increasingly exploring is the utilization of alternative materials.
By incorporating alternative materials, businesses can not only cut costs but also improve product sustainability and efficiency.
This approach has become essential in maintaining a competitive edge while addressing budget constraints.
The Role of the Purchasing Department
The purchasing department plays a pivotal role in sourcing and evaluating alternative materials.
They must assess the quality, cost, and availability of these materials to ensure they meet the company’s needs.
The department’s primary goal is to find materials that offer the same or better functionalities at a reduced cost.
Additionally, purchasing teams must consider the environmental impact and sustainability of materials, aligning with corporate social responsibility goals.
Through effective negotiation and strategic alliances with suppliers, purchasing departments can secure alternative materials that provide significant cost savings.
Identifying Cost-Effective Alternatives
The first step in utilizing alternative materials is identifying viable options.
The purchasing department can start this process by analyzing the current materials used and assessing areas where alternatives can be applied.
Research and development teams can be valuable partners in this exploration, providing insights into potential materials that may have previously been overlooked.
Once alternatives are identified, a thorough cost-benefit analysis should be conducted to determine the potential savings and any trade-offs regarding quality or performance.
Evaluating Quality and Performance
Quality is a major consideration when it comes to selecting alternative materials.
It’s essential that these materials match or exceed the quality of current options to maintain product standards and customer satisfaction.
The purchasing department should collaborate with the quality control team to run tests and evaluations of potential substitutes.
This process often involves testing the material under various conditions to ensure it performs satisfactorily throughout the product lifecycle.
Through these evaluations, companies can confidently transition to alternative materials without compromising quality.
Sustainability and Environmental Impact
Many companies are increasingly focused on environmental sustainability, and selecting eco-friendly materials is a crucial aspect of this trend.
The use of alternative materials can significantly reduce a company’s carbon footprint and contribute to a more sustainable supply chain.
Materials made from recycled components or that are biodegradable are often favored for their lower environmental impact.
The purchasing department should carefully assess the sustainability credentials of alternative materials, ensuring they align with the company’s overall sustainability objectives.
By doing so, businesses not only save costs but also contribute positively to the environment, which can enhance their brand reputation.
Supplier Collaboration and Innovation
Suppliers are essential partners in the transition to alternative materials.
Collaborating closely with suppliers can lead to innovative solutions that meet the company’s cost and performance criteria.
Suppliers often have specialized knowledge about the materials they offer and can provide valuable insights into ways alternative materials can be integrated into production processes.
Strong supplier relationships can also facilitate better terms and pricing, further enhancing cost savings.
By fostering a collaborative environment with suppliers, companies can leverage their expertise to identify the best alternative materials for their needs.
Challenges and Considerations
While the integration of alternative materials presents numerous benefits, it also comes with challenges.
Companies must be aware of potential supply chain disruptions as new materials are introduced.
Additionally, the upfront costs associated with testing and transitioning to new materials can be considerable.
It’s crucial to have a clear plan for managing these challenges, with contingency strategies in place should issues arise.
Communication across departments is vital to ensure everyone is aligned in the transition process.
Moreover, ongoing training for procurement teams on the latest material innovations will help keep them informed and proactive in identifying future opportunities.
Case Studies: Successful Cost Reduction
Several companies have successfully reduced costs through the implementation of alternative materials.
For example, a leading electronics manufacturer replaced their traditional metal casings with a high-strength, lightweight plastic alternative.
This change not only reduced material costs but also improved energy efficiency in product transportation due to the reduced weight.
In another instance, a fashion company switched to recycled synthetics for their garments, achieving significant material cost reductions while boosting their sustainability profile.
These examples highlight the potential of alternative materials to deliver tangible benefits across different industries.
Conclusion
The utilization of alternative materials offers a valuable strategy for cost reduction and enhanced sustainability.
The purchasing department plays a critical role in identifying, evaluating, and implementing these materials.
By working closely with suppliers and other internal departments, procurement teams can ensure that alternative materials meet quality standards while delivering the desired cost savings.
Embracing innovative materials not only helps businesses remain competitive but also positions them as leaders in sustainability.
As companies navigate the complexities of the modern market, the strategic selection of alternative materials will be an indispensable tool for driving success.
資料ダウンロード
QCD調達購買管理クラウド「newji」は、調達購買部門で必要なQCD管理全てを備えた、現場特化型兼クラウド型の今世紀最高の購買管理システムとなります。
ユーザー登録
調達購買業務の効率化だけでなく、システムを導入することで、コスト削減や製品・資材のステータス可視化のほか、属人化していた購買情報の共有化による内部不正防止や統制にも役立ちます。
NEWJI DX
製造業に特化したデジタルトランスフォーメーション(DX)の実現を目指す請負開発型のコンサルティングサービスです。AI、iPaaS、および先端の技術を駆使して、製造プロセスの効率化、業務効率化、チームワーク強化、コスト削減、品質向上を実現します。このサービスは、製造業の課題を深く理解し、それに対する最適なデジタルソリューションを提供することで、企業が持続的な成長とイノベーションを達成できるようサポートします。
オンライン講座
製造業、主に購買・調達部門にお勤めの方々に向けた情報を配信しております。
新任の方やベテランの方、管理職を対象とした幅広いコンテンツをご用意しております。
お問い合わせ
コストダウンが利益に直結する術だと理解していても、なかなか前に進めることができない状況。そんな時は、newjiのコストダウン自動化機能で大きく利益貢献しよう!
(Β版非公開)