- お役立ち記事
- Contract management methods for purchasing departments to achieve material supply sustainability
Contract management methods for purchasing departments to achieve material supply sustainability
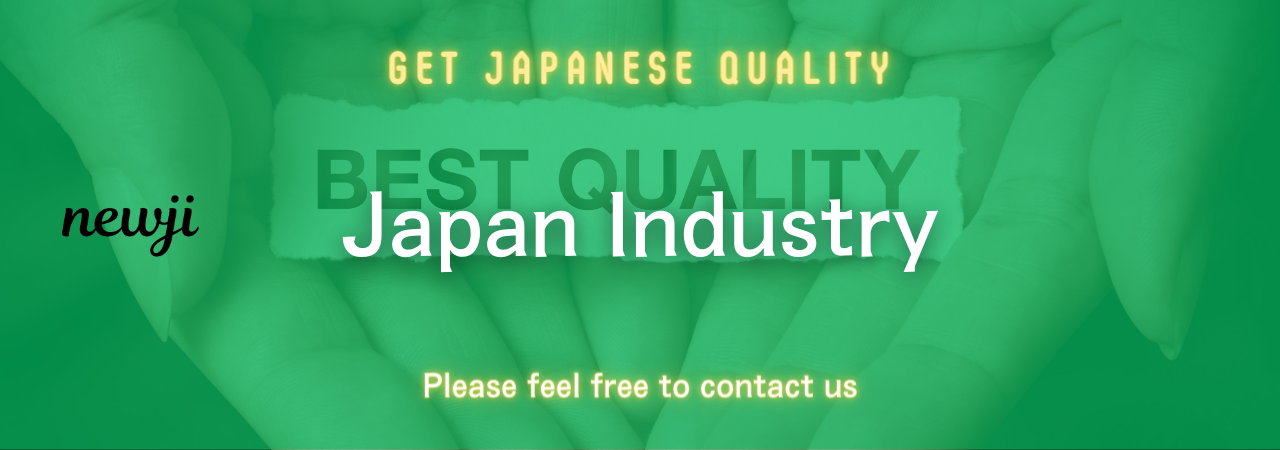
目次
Understanding Contract Management in Purchasing Departments
Contract management plays a pivotal role in the purchasing departments of any organization.
It involves overseeing the creation, execution, and analysis of contracts to maximize operational and financial performance.
With effective contract management, the purchasing department ensures the organization receives the right materials at the right time, helping to sustain material supply efficiently.
In today’s competitive business environment, purchasing departments need robust contract management methods to secure their supply chains and achieve sustainability.
A well-managed contract not only reduces risks but also supports long-term partnerships with suppliers.
Let’s explore some key strategies and methods that purchasing departments can use to ensure sustainable material supply.
Establishing Clear Objectives and Requirements
A vital step in contract management is to establish clear objectives and requirements for each contract.
The purchasing department should outline specific goals concerning material quality, delivery timelines, pricing, and ethical sourcing.
By defining these objectives early, the department can negotiate contracts that align with the organization’s sustainability goals.
Moreover, understanding the organization’s supply chain needs helps the department to anticipate market changes and ensure the availability of necessary materials.
Clear objectives also pave the way for effective communication with suppliers, ensuring that both parties have a mutual understanding of expectations and deliverables.
Implementing Supplier Evaluation and Selection
Choosing the right suppliers is crucial for sustainable contract management.
The purchasing department needs a robust evaluation and selection process to identify suppliers who can meet the organization’s standards for quality, reliability, and sustainability.
A comprehensive supplier evaluation might include criteria such as financial stability, manufacturing capabilities, and commitment to sustainable practices.
By assessing potential suppliers against these criteria, the purchasing department ensures that only the most suitable partners are chosen, enhancing the supply chain’s resilience and sustainability.
Regularly reviewing supplier performance is also important.
Through performance metrics and feedback mechanisms, the department can maintain high standards and address any issues that arise quickly.
Leveraging Technology for Efficient Contract Management
Technological advancements have significantly impacted contract management.
Using modern contract management software, purchasing departments can streamline their processes, enhance transparency, and improve collaboration.
Contract management tools offer features like automated reminders for contract renewals, centralized storage for easy access, and analytics tools for performance assessment.
These features enable organizations to manage contracts more proactively, reducing the risk of disruptions in the material supply chain.
Moreover, technology can help departments keep track of contract audits and compliance requirements, ensuring adherence to legal standards and organizational policies.
This not only helps avoid potential legal issues but also aligns the department’s operations with the broader sustainability goals of the organization.
Fostering Collaborative Supplier Relationships
Beyond formal agreements, fostering strong, collaborative relationships with suppliers is essential for sustainable material supply.
This involves going beyond transactional interactions and working toward long-term partnerships based on trust and mutual benefit.
The purchasing department should engage in open dialogues with suppliers to address challenges and explore opportunities for innovation and improvement.
By demonstrating a commitment to mutual growth and sustainability, organizations can foster loyalty and ensure consistent material supply even in volatile market conditions.
Regular meetings, joint goal-setting sessions, and feedback loops can help maintain the relationship and ensure that both parties remain aligned with the contract’s objectives.
It also provides a platform for discussing adjustments in response to market trends or organizational changes.
Adapting to Market and Environmental Changes
The market landscape is constantly changing, influenced by factors such as technological advancements, regulatory changes, and environmental concerns.
Purchasing departments must stay agile and adaptive to maintain sustainable material supply.
Regular market research and trend analysis are essential to anticipate these changes and adjust contract strategies accordingly.
For instance, if a new regulation impacts a supplier’s ability to deliver materials, the purchasing department needs to adapt the contract terms or explore alternative suppliers promptly.
Additionally, an increasing focus on environmental sustainability requires purchasing departments to consider the carbon footprint of their supply chains.
Adapting contracts to include environmentally friendly practices can enhance sustainability and ensure compliance with industry standards.
Building Risk Management into Contracts
Risk management is a crucial component of contract management.
Contracts should include risk management clauses that address potential supply chain disruptions, financial stability of suppliers, and quality assurance.
By identifying risks early and incorporating them into contracts, purchasing departments can develop strategies for mitigation, such as securing multiple suppliers for critical materials or including penalties for non-compliance with quality standards.
Effective risk management ensures that the organization can quickly respond to any unforeseen disruptions and maintain continuity in material supply, thus securing the supply chain against future uncertainties.
Conclusion
Achieving material supply sustainability through effective contract management requires a strategic approach from purchasing departments.
By establishing clear objectives, selecting the right suppliers, leveraging technology, fostering supplier relationships, adapting to changes, and managing risks, organizations can secure their supply chains efficiently.
As the market continues to evolve, purchasing departments must remain proactive in their contract management practices, ensuring that they are equipped to meet the demands of sustainability and operational success.
Emphasizing collaboration and innovation, organizations can not only meet their material supply needs but also advance their sustainability objectives, ultimately contributing to a more resilient and responsible supply chain.
資料ダウンロード
QCD調達購買管理クラウド「newji」は、調達購買部門で必要なQCD管理全てを備えた、現場特化型兼クラウド型の今世紀最高の購買管理システムとなります。
ユーザー登録
調達購買業務の効率化だけでなく、システムを導入することで、コスト削減や製品・資材のステータス可視化のほか、属人化していた購買情報の共有化による内部不正防止や統制にも役立ちます。
NEWJI DX
製造業に特化したデジタルトランスフォーメーション(DX)の実現を目指す請負開発型のコンサルティングサービスです。AI、iPaaS、および先端の技術を駆使して、製造プロセスの効率化、業務効率化、チームワーク強化、コスト削減、品質向上を実現します。このサービスは、製造業の課題を深く理解し、それに対する最適なデジタルソリューションを提供することで、企業が持続的な成長とイノベーションを達成できるようサポートします。
オンライン講座
製造業、主に購買・調達部門にお勤めの方々に向けた情報を配信しております。
新任の方やベテランの方、管理職を対象とした幅広いコンテンツをご用意しております。
お問い合わせ
コストダウンが利益に直結する術だと理解していても、なかなか前に進めることができない状況。そんな時は、newjiのコストダウン自動化機能で大きく利益貢献しよう!
(Β版非公開)