- お役立ち記事
- A guide to conducting supplier performance evaluations led by purchasing departments
A guide to conducting supplier performance evaluations led by purchasing departments
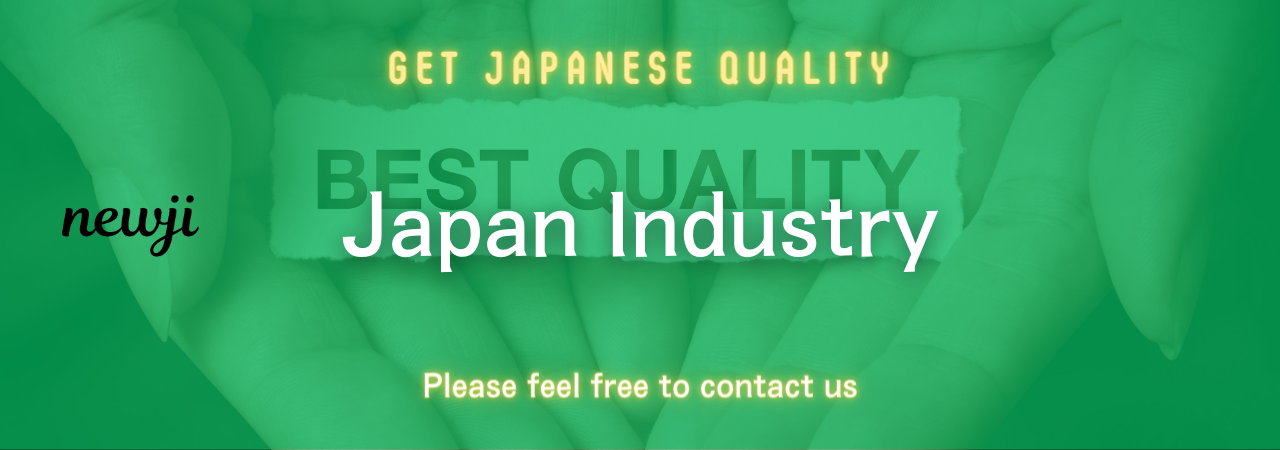
目次
Understanding Supplier Performance Evaluations
Conducting supplier performance evaluations is a critical activity for purchasing departments.
These evaluations help ensure that suppliers are meeting the company’s needs in terms of quality, consistency, and cost-effectiveness.
By regularly assessing suppliers, businesses can mitigate risks, enhance supply chain operations, and foster stronger relationships.
In this guide, we will explore the steps and considerations involved in conducting effective supplier performance evaluations.
Why Are Supplier Performance Evaluations Important?
Supplier performance evaluations allow purchasing departments to identify and address any issues with suppliers.
Evaluations enable companies to ensure that suppliers are aligned with their long-term goals and expectations.
Regular assessments can also drive improvements in supplier performance, which can lead to better product quality, reduced costs, and enhanced customer satisfaction.
Improving Supplier Relationships
One major benefit of supplier performance evaluations is the potential improvement in supplier relationships.
By setting clear expectations and providing feedback, companies can promote transparency and open communication.
This leads to a sustainable partnership where both parties work together to meet mutual goals.
Risk Management
Evaluating suppliers helps companies identify potential risks in their supply chain.
By addressing issues early, businesses can avoid disruptions, delays, and financial losses.
Supplier performance evaluations are an essential component of a comprehensive risk management strategy.
Key Metrics for Supplier Performance Evaluations
When conducting supplier performance evaluations, it is important to define clear metrics.
These metrics should be aligned with the company’s objectives and provide a comprehensive view of a supplier’s performance.
Here are some crucial metrics to consider:
Quality
Evaluate the quality of products or services provided by the supplier.
You can track defect rates, returns, and adherence to specifications to generate a clear picture of quality performance.
Improving product quality can lead to increased customer satisfaction and reduced waste.
Delivery Performance
Timeliness is another crucial metric in supplier assessments.
This includes evaluating whether the supplier meets deadlines, provides accurate shipment quantities, and delivers within agreed timeframes.
Maintaining excellent delivery performance ensures a smooth supply chain.
Cost Management
Assess how well a supplier manages costs.
This can involve analyzing price competitiveness, cost-saving initiatives, and financial stability.
Cost management is an important factor in maintaining profitability and market competitiveness.
Compliance and Sustainability
Evaluate whether the supplier complies with industry regulations and sustainability practices.
This includes environmental policies, labor laws, and ethical sourcing practices.
Adhering to compliance and sustainability standards is increasingly important for protecting brand reputation.
Steps for Conducting Supplier Performance Evaluations
Implementing a structured evaluation process is essential for obtaining the best results.
Here are the steps to conduct a comprehensive supplier performance evaluation:
Define Evaluation Criteria
Identify the key metrics and criteria that are important for your business.
Consider involving cross-functional teams to gather diverse input and ensure the criteria are comprehensive.
Collect and Analyze Data
Gather data on each of the defined metrics.
This could include internal audits, customer feedback, and industry benchmarks. Analyze the data to identify trends and areas for improvement.
Provide Feedback
Share the evaluation results with the supplier in a constructive manner.
Highlight areas of success while also providing actionable recommendations for improvement. Maintain open communication to promote a collaborative relationship.
Develop Action Plans
Work with suppliers to create clear action plans.
These should include timelines, responsibilities, and specific objectives for performance improvement. Continually monitor progress to ensure the action plans are effective.
Review and Adjust Regularly
Supplier performance evaluations should not be a one-time activity.
Regularly review and adjust the evaluation process to ensure it remains relevant. Stay up-to-date with market trends and internal requirements to adjust criteria as needed.
Challenges and Best Practices
There are challenges to keep in mind when conducting supplier performance evaluations.
Being aware of these challenges can help you develop strategies to overcome them.
Data Accuracy
Ensure that the data used for evaluations is accurate and reliable.
Inaccurate data can lead to incorrect assessments and poor decision-making. Implementing robust data collection and verification processes can help maintain data integrity.
Supplier Buy-in
Gaining the cooperation of suppliers is crucial for successful evaluations.
Be transparent about the purpose of evaluations and involve suppliers in the process. This helps establish trust and encourages willingness to improve.
Balancing Objectivity with Subjectivity
While quantitative metrics are important, qualitative assessments should not be overlooked.
Consider feedback from relevant stakeholders to balance objective data with subjective insights.
By following these steps and best practices, purchasing departments can conduct thorough and effective supplier performance evaluations.
This not only ensures that suppliers align with business goals but also drives continuous improvement and strengthens the supply chain.
As a result, companies can achieve greater efficiency, reduce risks, and enhance relationships with their suppliers.
資料ダウンロード
QCD調達購買管理クラウド「newji」は、調達購買部門で必要なQCD管理全てを備えた、現場特化型兼クラウド型の今世紀最高の購買管理システムとなります。
ユーザー登録
調達購買業務の効率化だけでなく、システムを導入することで、コスト削減や製品・資材のステータス可視化のほか、属人化していた購買情報の共有化による内部不正防止や統制にも役立ちます。
NEWJI DX
製造業に特化したデジタルトランスフォーメーション(DX)の実現を目指す請負開発型のコンサルティングサービスです。AI、iPaaS、および先端の技術を駆使して、製造プロセスの効率化、業務効率化、チームワーク強化、コスト削減、品質向上を実現します。このサービスは、製造業の課題を深く理解し、それに対する最適なデジタルソリューションを提供することで、企業が持続的な成長とイノベーションを達成できるようサポートします。
オンライン講座
製造業、主に購買・調達部門にお勤めの方々に向けた情報を配信しております。
新任の方やベテランの方、管理職を対象とした幅広いコンテンツをご用意しております。
お問い合わせ
コストダウンが利益に直結する術だと理解していても、なかなか前に進めることができない状況。そんな時は、newjiのコストダウン自動化機能で大きく利益貢献しよう!
(Β版非公開)