- お役立ち記事
- Cultural challenges faced by purchasing departments in global sourcing quality management and how to overcome them
Cultural challenges faced by purchasing departments in global sourcing quality management and how to overcome them
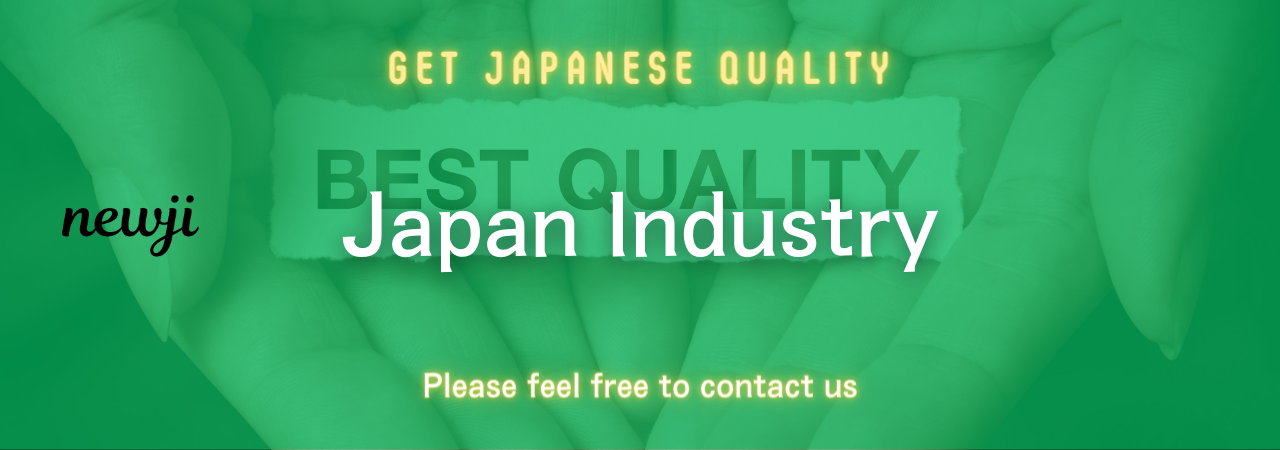
目次
Understanding Global Sourcing Quality Management
Global sourcing is a strategy employed by businesses to procure goods and services from international markets to take advantage of cost efficiencies, specialized expertise, or advanced technologies available in other regions.
While this approach presents numerous benefits, it also poses significant challenges, especially concerning quality management.
Cultural differences between the purchasing department and suppliers can impact communication, quality expectations, adherence to standards, and overall satisfaction.
To succeed in global sourcing, it is crucial for purchasing departments to understand these cultural challenges and develop strategies to overcome them.
The Cultural Challenges in Global Sourcing
Communication Barriers
One of the primary cultural challenges in global sourcing is communication barriers.
These barriers can arise from differences in language, communication styles, and even non-verbal behaviors.
Misunderstandings might occur when instructions, expectations, or feedback are not conveyed clearly between the purchasing department and the supplier.
Such communication issues can lead to errors, delays, and compromised quality of the sourced goods.
Varied Quality Standards
Different countries often have diverse standards and regulations when it comes to producing goods.
What is considered a high-quality product in one country may not meet the standards of another.
This disparity can lead to disagreements over product specifications and compliances, potentially resulting in quality issues.
Purchasing departments must be aware of these differences and find ways to align quality expectations with supplier capabilities.
Differences in Business Practices
Every country has its own set of business practices, which can include negotiation strategies, decision-making processes, and attitudes towards contracts.
Misalignments between the purchasing department’s practices and those of the suppliers can lead to inefficiencies and misinterpretations of contract terms.
To ensure smooth transactions, purchasing teams need to be flexible and adaptive.
Time Zone and Geographical Differences
Dealing with suppliers across different time zones can create logistical challenges.
For example, if a quality issue arises, there might be delays in getting responses or resolutions simply due to the time difference.
Geographical separation also complicates on-site inspections and direct quality control, adding layers of difficulty to governance and management.
Strategies to Overcome Cultural Challenges
Enhancing Communication
To bridge communication gaps, purchasing departments should prioritize the selection of bilingual staff or use reliable translation services.
Regular training programs focusing on intercultural communication can help build awareness and sensitivity towards different communication styles and non-verbal cues.
Having a standardized protocol for exchanging information, such as the use of visuals and written instructions, can also mitigate misunderstandings.
Setting Clear Quality Standards
It is essential for purchasing departments to establish and communicate clear quality expectations from the outset.
This can be achieved by setting explicit quality control metrics and relying on internationally recognized standards.
Conducting joint product testing with suppliers before finalizing production can also help align expectations and ensure that the required quality standards are met.
Fostering Relationship Building
Building strong relationships with suppliers is vital for overcoming cultural differences.
Investing time in face-to-face meetings, attending cultural training programs, and understanding the value systems of suppliers can help build trust and mutual respect.
Long-term partnerships tend to lead to better cooperation, making it easier to manage quality together.
Utilizing Technology
Advances in technology offer new ways of bridging geographical and time zone divides.
Collaborative platforms and cloud-based software enable real-time communication and coordination, helping purchasing departments stay in touch and manage quality issues more promptly.
Additionally, technologies such as video conferencing can facilitate regular meetings across the globe, minimizing the impact of geographical distances.
Understanding and Adapting to Local Practices
Purchasing departments should study and understand the local business and cultural practices of their suppliers.
This can involve learning about negotiation styles, respect for hierarchies, and decision-making processes.
Being flexible and adaptable in approach can lead to smoother interactions and more successful collaborations.
The Role of Training and Development
Ongoing training and development play a crucial role in overcoming cultural challenges in global sourcing.
By equipping team members with knowledge about cultural nuances and effective quality management practices, businesses can foster an environment that supports collaboration and innovation.
Workshops, cultural immersion programs, and mentorship schemes can allow staff to learn from global best practices and stay abreast of evolving trends and regulations.
Conclusion
The challenges faced by purchasing departments in global sourcing quality management due to cultural differences are significant but not insurmountable.
By understanding these challenges and implementing proactive strategies, such as enhancing communication, setting clear quality standards, building relationships, leveraging technology, and fostering continuous learning, businesses can achieve high-quality outcomes in global sourcing endeavors.
Ultimately, successful management of these cultural challenges leads to stronger supplier relationships, improved product quality, and a competitive edge in the global marketplace.
資料ダウンロード
QCD調達購買管理クラウド「newji」は、調達購買部門で必要なQCD管理全てを備えた、現場特化型兼クラウド型の今世紀最高の購買管理システムとなります。
ユーザー登録
調達購買業務の効率化だけでなく、システムを導入することで、コスト削減や製品・資材のステータス可視化のほか、属人化していた購買情報の共有化による内部不正防止や統制にも役立ちます。
NEWJI DX
製造業に特化したデジタルトランスフォーメーション(DX)の実現を目指す請負開発型のコンサルティングサービスです。AI、iPaaS、および先端の技術を駆使して、製造プロセスの効率化、業務効率化、チームワーク強化、コスト削減、品質向上を実現します。このサービスは、製造業の課題を深く理解し、それに対する最適なデジタルソリューションを提供することで、企業が持続的な成長とイノベーションを達成できるようサポートします。
オンライン講座
製造業、主に購買・調達部門にお勤めの方々に向けた情報を配信しております。
新任の方やベテランの方、管理職を対象とした幅広いコンテンツをご用意しております。
お問い合わせ
コストダウンが利益に直結する術だと理解していても、なかなか前に進めることができない状況。そんな時は、newjiのコストダウン自動化機能で大きく利益貢献しよう!
(Β版非公開)