- お役立ち記事
- Challenges and solutions faced by purchasing departments when rebuilding material supply networks
Challenges and solutions faced by purchasing departments when rebuilding material supply networks
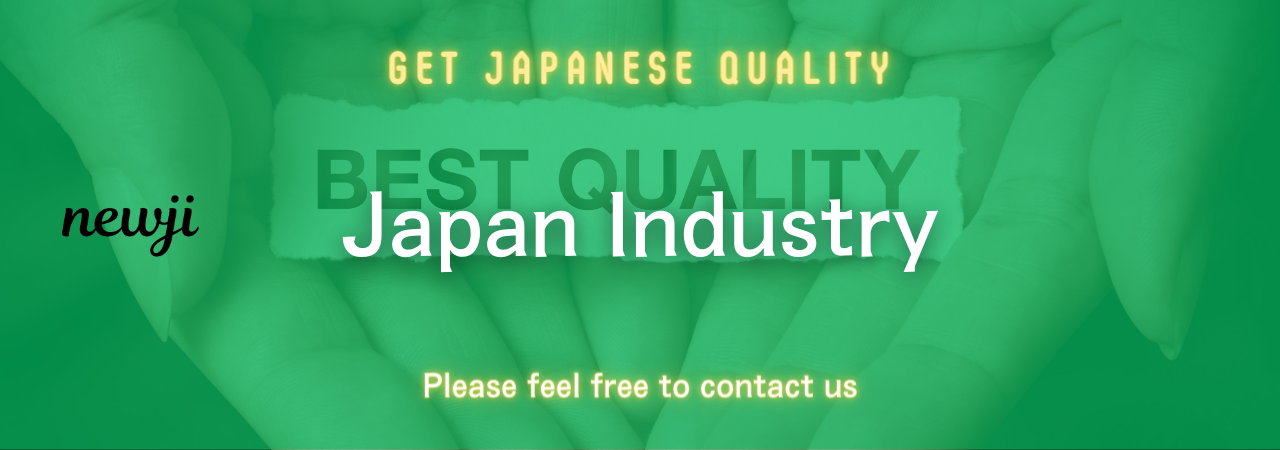
目次
Understanding the Challenges Faced by Purchasing Departments
Purchasing departments play a vital role in organizations, responsible for acquiring raw materials and goods necessary for production.
Over time, these departments encounter various challenges, especially when circumstances demand the rebuilding of material supply networks.
In this digital age, the dynamic nature of supply chains means that purchasing departments must continually adapt to new obstacles.
One significant challenge faced by purchasing departments is the disruption of existing supply chains.
This can occur due to economic fluctuations, geopolitical tensions, natural disasters, or changes in regulations.
Such disruptions may lead to delayed deliveries, increased costs, or even shortages in critical materials.
Another prevalent issue in rebuilding supply networks is managing supplier relationships.
When evaluating potential suppliers, purchasing departments must consider factors like cost, quality, reliability, and the geopolitical stability of the supplier’s location.
Technological advancements and globalization have also introduced complexities.
With the integration of technology, purchasing departments need to be agile, adopting new platforms for procurement and communication.
Additionally, globalization has expanded the supplier base but also brought challenges in managing longer supply chains with potentially more complications.
Effective Solutions for Rebuilding Supply Networks
To navigate these complex challenges, purchasing departments must employ effective strategies to reconstruct and optimize their supply networks.
One of the most valuable approaches is fostering strong supplier relationships.
Building long-term partnerships with reputable suppliers can help ensure a more reliable flow of materials.
Negotiating and maintaining transparent communication can lead to better collaboration and trust.
Moreover, diversification of supplier base is crucial.
Relying on a single or limited number of suppliers can be risky.
By having a diverse range of suppliers, purchasing departments can mitigate the risk of disruptions.
This ensures there are alternative suppliers available if one fails to deliver due to unforeseen circumstances.
Adopting modern technology is another effective solution.
Leveraging data analytics tools can provide insights into supplier performance, market trends, and potential risks.
Automation in procurement processes can also improve efficiency and reduce human error.
E-commerce platforms and digital procurement solutions can streamline the purchase process, making it quicker and more cost-effective.
Additionally, developing a comprehensive risk management plan is essential.
This involves identifying potential risks and establishing contingency plans to manage them.
By being proactive and prepared, purchasing departments can respond swiftly to disruptions, minimizing the impact on operations.
The Role of Sustainability in Supply Networks
In today’s world, sustainability has become a key consideration for purchasing departments.
The emphasis on environmentally-friendly practices in supply chains is not only beneficial for the planet but also helps organizations meet regulatory requirements and consumer expectations.
Implementing sustainable practices can improve the resilience of supply networks.
Sustainable sourcing involves assessing suppliers based on their environmental practices, ethical labor standards, and carbon footprint.
Choosing suppliers who adhere to these standards can enhance the sustainability of the entire supply chain.
Moreover, it can provide a competitive advantage, as consumers are increasingly aware of and interested in sustainability.
Implementing sustainable logistics also contributes significantly.
Transportation is a major source of emissions, and choosing eco-friendly shipping options can reduce a company’s overall carbon output.
Purchasing departments can work with supply chain partners to optimize routes and reduce waste in logistics.
The Importance of Collaboration and Communication
Collaboration and effective communication are indispensable for successful supply chain management.
Internally, purchasing departments must coordinate with other departments such as production, warehousing, and finance to align objectives and resources.
Externally, maintaining open lines of communication with suppliers is critical.
Regular meetings, feedback sessions, and updates can strengthen collaboration and ensure all parties are aligned.
Technology plays a pivotal role in facilitating communication.
Platforms that offer real-time updates and tracking can greatly enhance coordination between the purchasing team and suppliers.
Establishing a collaborative culture can lead to innovative solutions to shared challenges.
Partnerships with suppliers can result in joint problem-solving initiatives, helping both parties improve efficiency and reduce costs.
Conclusion
Rebuilding material supply networks is a complex task requiring careful strategy and execution.
Purchasing departments face a myriad of challenges, from supply disruptions to sustaining relationships with suppliers.
However, with effective solutions like fostering supplier relationships, diversifying suppliers, leveraging technology, and implementing sustainable practices, these departments can navigate challenges efficiently.
Moreover, the integration of collaboration and communication in supply chain management fosters stronger partnerships, leading to a more resilient and responsive supply network.
By being proactive and adaptive, purchasing departments can not only overcome obstacles but also create opportunities for growth and innovation.
資料ダウンロード
QCD調達購買管理クラウド「newji」は、調達購買部門で必要なQCD管理全てを備えた、現場特化型兼クラウド型の今世紀最高の購買管理システムとなります。
ユーザー登録
調達購買業務の効率化だけでなく、システムを導入することで、コスト削減や製品・資材のステータス可視化のほか、属人化していた購買情報の共有化による内部不正防止や統制にも役立ちます。
NEWJI DX
製造業に特化したデジタルトランスフォーメーション(DX)の実現を目指す請負開発型のコンサルティングサービスです。AI、iPaaS、および先端の技術を駆使して、製造プロセスの効率化、業務効率化、チームワーク強化、コスト削減、品質向上を実現します。このサービスは、製造業の課題を深く理解し、それに対する最適なデジタルソリューションを提供することで、企業が持続的な成長とイノベーションを達成できるようサポートします。
オンライン講座
製造業、主に購買・調達部門にお勤めの方々に向けた情報を配信しております。
新任の方やベテランの方、管理職を対象とした幅広いコンテンツをご用意しております。
お問い合わせ
コストダウンが利益に直結する術だと理解していても、なかなか前に進めることができない状況。そんな時は、newjiのコストダウン自動化機能で大きく利益貢献しよう!
(Β版非公開)