- お役立ち記事
- Appropriate inventory management and supply chain construction by purchasing department to reduce costs
Appropriate inventory management and supply chain construction by purchasing department to reduce costs
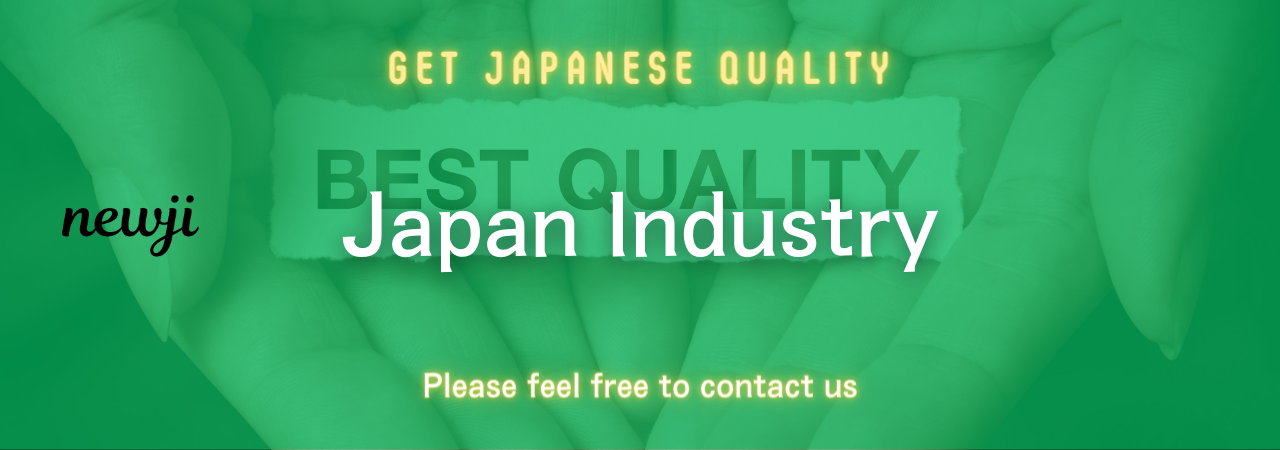
目次
Understanding Inventory Management
Inventory management is the cornerstone of a strong purchasing department.
It involves overseeing and controlling the ordering, storage, and use of components that a company needs for manufacturing its products.
For many businesses, effective inventory management can considerably reduce costs.
By optimizing the inventory, companies can minimize the amount of money tied up in stock while ensuring that goods or materials are available as needed.
This balance helps avoid both overstocking and stockouts, which can be costly.
Benefits of Efficient Inventory Management
One of the main advantages of effective inventory management is cost reduction.
When a purchasing department meticulously plans and controls inventory, it limits the capital that’s unnecessarily tied up in surplus stock.
This process involves accurate demand forecasting and strategic stock replenishment.
Furthermore, it streamlines operations as there are fewer last-minute orders, reducing potential disruptions.
By maintaining an ideal inventory level, businesses can also reduce warehouse costs, which contribute significantly to overhead expenses.
Approaches to Inventory Optimization
There are several strategies that a purchasing department can employ to achieve optimal inventory management.
1. Demand Forecasting
Demand forecasting involves using historical data, market trends, and predictive analytics to anticipate future customer demand.
With precise forecasting, the purchasing department can order the right quantities of stock, reducing excess inventory and the issues arising from understocking.
2. Just-In-Time (JIT) Inventory
The JIT inventory strategy aims to increase efficiency and reduce wastage by receiving goods only as they are needed in the production process.
This approach minimizes inventory costs and helps in maintaining low inventory levels.
3. ABC Analysis
ABC analysis is a method that categorizes inventory into three classes: A, B, and C.
‘A’ items are high-value products with a low-frequency sales rate, ‘B’ items are moderate in value and frequency, and ‘C’ items are low-value products with high-frequency sales.
This analysis helps businesses to prioritize inventory management efforts according to the monetary value of the goods.
Building an Efficient Supply Chain
In addition to inventory management, an efficient supply chain is crucial for reducing costs.
A well-constructed supply chain enables a seamless flow of materials and goods from suppliers to the end consumer.
Key Elements of a Successful Supply Chain
An efficient supply chain relies on several key elements, which are necessary for added value and cost reduction.
1. Supplier Relationships
Maintaining strong relationships with suppliers is critical for any purchasing department.
A reliable supplier can provide better rates and more flexible terms, contributing to reduced costs.
Additionally, having open lines of communication ensures that potential issues are resolved swiftly, maintaining the smooth operation of the supply chain.
2. Technology Integration
Leveraging technology can vastly improve supply chain efficiency.
With an integrated supply chain management system, companies can track orders, manage inventory, and coordinate logistics in real-time.
This technological adoption leads to informed decision-making and reduces the chance of errors.
3. Transportation Management
Transportation is a significant part of the supply chain that can impact costs.
Optimizing transportation by selecting the best routes, utilizing suitable modes of transport, and consolidating shipments can lead to substantial savings.
Effective transportation management not only lowers costs but also reduces delivery times, enhancing customer satisfaction.
Collaboration Between Purchasing and Other Departments
The purchasing department does not work in isolation when optimizing inventory and supply chains.
Collaboration with other departments, such as sales, production, and finance, is essential for holistic cost reduction in a company.
Integrating Sales Forecasting
Aligning inventory management with sales forecasts can ensure that stock levels match the anticipated demand.
This collaboration minimizes overstocking or understocking scenarios, which can result in additional costs and decreased customer satisfaction.
Synergy with Production Planning
Working closely with the production team ensures that the purchasing department aligns procurement with production schedules.
Timely material availability prevents production delays, reducing associated costs and maintaining efficient workflow.
Budget Planning with Finance
Regular collaboration with the finance department provides insights into costing and budgetary constraints.
By understanding the financial implications, the purchasing department can make informed decisions about inventory investment and supplier negotiations.
Continuous Improvement for Cost Reduction
Cost reduction in inventory management and supply chain construction is not a one-time task but an ongoing process.
Continuous improvement involves regularly reviewing and optimizing inventory practices and supply chain operations.
Implementing Lean Practices
Applying lean principles to inventory management and supply chain processes can help in identifying and eliminating waste, thus enhancing operational efficiency.
Regular Audits and Reviews
Conducting regular audits allows companies to assess the current state of their inventory and supply chain practices.
These reviews provide insights into areas that require improvement, unearthing potential cost-saving opportunities.
Embracing Flexibility
In today’s dynamic market, flexibility in inventory management and supply chain operations ensures adaptability to changing demand patterns and market conditions.
This agility is vital for maintaining cost-efficiency and competitiveness.
In conclusion, the purchasing department plays an integral role in reducing costs through proper inventory management and supply chain construction.
By employing various strategies and fostering collaboration, companies can achieve substantial savings while ensuring that they meet customer demands efficiently.
資料ダウンロード
QCD調達購買管理クラウド「newji」は、調達購買部門で必要なQCD管理全てを備えた、現場特化型兼クラウド型の今世紀最高の購買管理システムとなります。
ユーザー登録
調達購買業務の効率化だけでなく、システムを導入することで、コスト削減や製品・資材のステータス可視化のほか、属人化していた購買情報の共有化による内部不正防止や統制にも役立ちます。
NEWJI DX
製造業に特化したデジタルトランスフォーメーション(DX)の実現を目指す請負開発型のコンサルティングサービスです。AI、iPaaS、および先端の技術を駆使して、製造プロセスの効率化、業務効率化、チームワーク強化、コスト削減、品質向上を実現します。このサービスは、製造業の課題を深く理解し、それに対する最適なデジタルソリューションを提供することで、企業が持続的な成長とイノベーションを達成できるようサポートします。
オンライン講座
製造業、主に購買・調達部門にお勤めの方々に向けた情報を配信しております。
新任の方やベテランの方、管理職を対象とした幅広いコンテンツをご用意しております。
お問い合わせ
コストダウンが利益に直結する術だと理解していても、なかなか前に進めることができない状況。そんな時は、newjiのコストダウン自動化機能で大きく利益貢献しよう!
(Β版非公開)