- お役立ち記事
- Best practices for purchasing to increase material supply reliability
Best practices for purchasing to increase material supply reliability
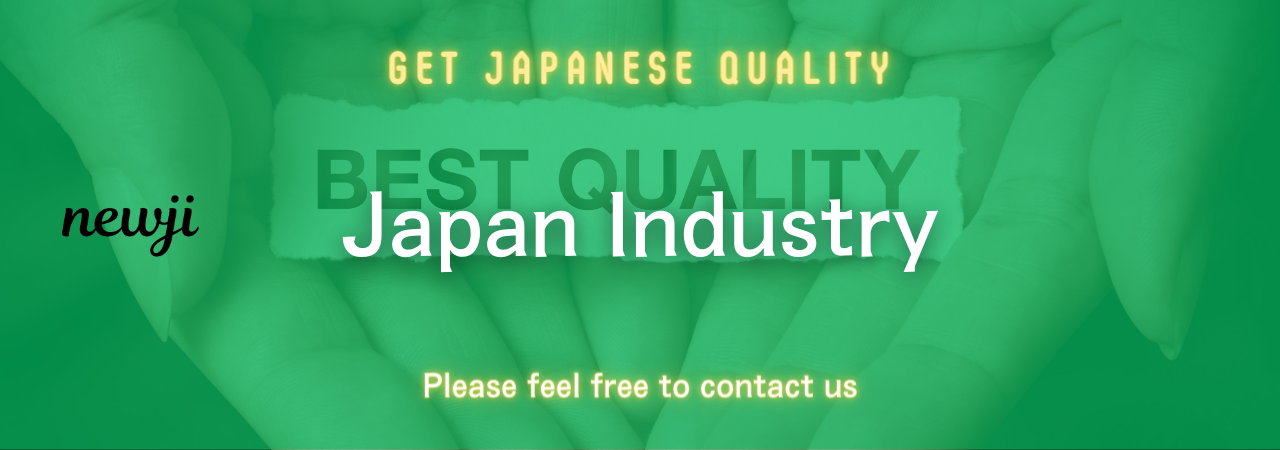
目次
Understanding the Importance of Reliable Material Supply
In today’s competitive business environment, ensuring a steady and reliable supply of materials is crucial for any company’s success.
Material supply reliability directly impacts production schedules, product quality, customer satisfaction, and ultimately, the bottom line.
A disruption in the material supply chain can lead to production delays, increased costs, and revenue loss.
Therefore, implementing best practices in purchasing can help businesses maintain a reliable supply of materials.
Establish Strong Supplier Relationships
One of the key strategies to improve material supply reliability is to build and maintain strong relationships with suppliers.
This means selecting suppliers who are trustworthy, capable, and compatible with your business needs.
Choose the Right Supplier
Start by conducting thorough research to identify potential suppliers.
Evaluate their reputation, reliability, and track record for delivering quality materials on time.
It’s important to assess their production capacity, financial stability, and ability to scale with your business.
Effective Communication
Keeping an open line of communication with your suppliers fosters trust and transparency.
Regular updates and feedback help identify potential problems early and create a collaborative environment to solve any issues.
Implement Strategic Sourcing
Strategic sourcing is a vital approach to ensure a consistent supply of materials.
It involves analyzing procurement activities to find more efficient and cost-effective methods of sourcing.
Understand Market Trends
Stay informed about the latest market trends and influences that could impact material availability, such as natural disasters, geopolitical events, or changes in trade policies.
Understanding these trends will allow you to anticipate supply chain disruptions and plan accordingly.
Diversify Your Supplier Base
Relying on a single supplier can be risky if they face any difficulties.
Diversify your supplier base to mitigate risks associated with dependence on one source.
Having multiple suppliers ensures that you can maintain supply even if one supplier fails to deliver.
Leverage Technology
The use of technology in the procurement process can significantly improve material supply reliability.
Automation, data analysis, and advanced software can enhance efficiency and provide better visibility across the supply chain.
Use Procurement Software
Implementing procurement software can streamline ordering processes, manage supplier relationships, track inventory levels, and analyze purchasing data.
This results in better decision-making and helps prevent shortages or overstocking.
Embrace IoT and AI
Integrating Internet of Things (IoT) devices and Artificial Intelligence (AI) in the supply chain can provide real-time data and predictive analytics.
This technology can forecast demand, optimize inventory management, and alert you to potential supply chain disruptions well in advance.
Establish Robust Contracts
Having well-structured contracts with suppliers ensures mutual understanding and commitment.
Contracts should clearly define expectations, obligations, and consequences for non-compliance.
Include Contingency Clauses
Incorporate contingency clauses in contracts to manage unforeseen disruptions, such as natural disasters or transportation delays.
These clauses should outline alternative actions that suppliers must take to fulfill their obligations.
Regularly Review Contracts
Periodically review and update contracts to reflect changes in the business environment or company needs.
Ensure that terms remain relevant and beneficial to both parties as circumstances evolve.
Monitor and Measure Performance
Regular monitoring and assessment of supplier performance are crucial for maintaining supply reliability.
Set key performance indicators (KPIs) to evaluate suppliers based on delivery time, material quality, and service responsiveness.
Conduct Supplier Audits
Performing supplier audits helps ensure adherence to quality standards and confirm that suppliers have sufficient resources to support your needs.
Identify areas for improvement and collaborate with suppliers to elevate their performance.
Analyze Performance Data
Collect and analyze performance data to identify trends and patterns.
Use insights gained to make data-driven adjustments to purchasing strategies and negotiate better terms with suppliers.
Prepare for Unexpected Situations
No matter how meticulously plans are laid out, unforeseen events can still disrupt material supply chains.
It’s crucial to have contingency plans in place for quick recovery from disruptions.
Develop a Risk Management Plan
Create a comprehensive risk management plan to address potential supply chain disruptions.
Identify risks, develop mitigation strategies, and establish a crisis management team responsible for executing recovery plans.
Maintain Safety Stock
Safety stock acts as a buffer against unexpected spikes in demand or supply interruptions.
Calculate the appropriate level of safety stock based on historical data and projections to avoid production stops.
By implementing these best practices in purchasing, companies can significantly strengthen their material supply reliability.
This proactive approach helps avoid disruptions, reduces costs, and ensures a seamless production process essential for maintaining customer satisfaction and achieving business goals.
Fostering strong supplier relationships, leveraging technology, and preparing for unexpected events will keep your supply chain resilient and ready to meet any challenge.
資料ダウンロード
QCD調達購買管理クラウド「newji」は、調達購買部門で必要なQCD管理全てを備えた、現場特化型兼クラウド型の今世紀最高の購買管理システムとなります。
ユーザー登録
調達購買業務の効率化だけでなく、システムを導入することで、コスト削減や製品・資材のステータス可視化のほか、属人化していた購買情報の共有化による内部不正防止や統制にも役立ちます。
NEWJI DX
製造業に特化したデジタルトランスフォーメーション(DX)の実現を目指す請負開発型のコンサルティングサービスです。AI、iPaaS、および先端の技術を駆使して、製造プロセスの効率化、業務効率化、チームワーク強化、コスト削減、品質向上を実現します。このサービスは、製造業の課題を深く理解し、それに対する最適なデジタルソリューションを提供することで、企業が持続的な成長とイノベーションを達成できるようサポートします。
オンライン講座
製造業、主に購買・調達部門にお勤めの方々に向けた情報を配信しております。
新任の方やベテランの方、管理職を対象とした幅広いコンテンツをご用意しております。
お問い合わせ
コストダウンが利益に直結する術だと理解していても、なかなか前に進めることができない状況。そんな時は、newjiのコストダウン自動化機能で大きく利益貢献しよう!
(Β版非公開)