- お役立ち記事
- Revolutionizing Japanese Manufacturing: An Inside Look at Motor Iron Loss Visualization Devices
Revolutionizing Japanese Manufacturing: An Inside Look at Motor Iron Loss Visualization Devices
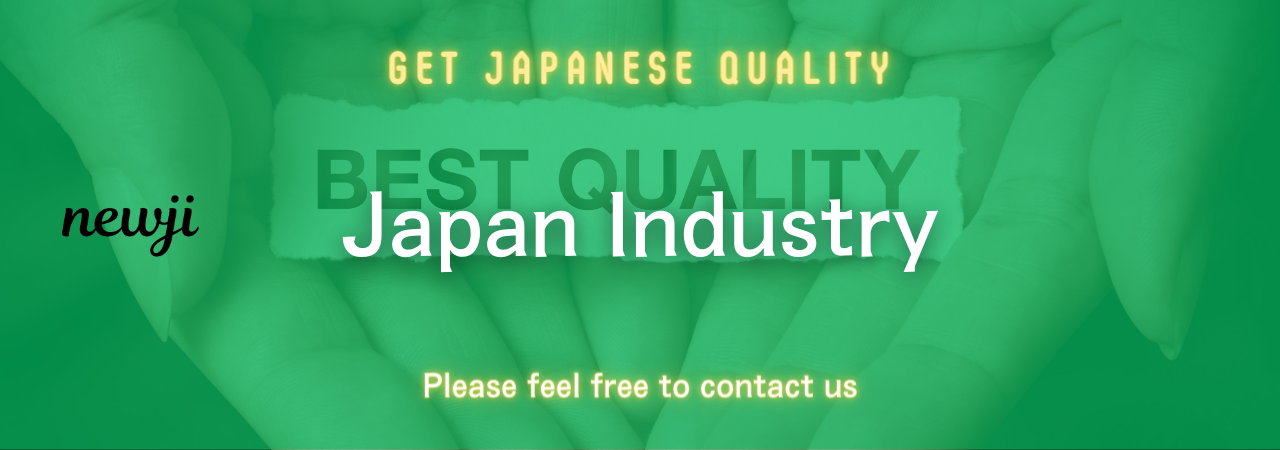
目次
Introduction to Motor Iron Loss Visualization Devices
In the realm of Japanese manufacturing, continuous improvement and precision are paramount. One of the latest innovations driving this excellence is the motor iron loss visualization device. These devices play a critical role in optimizing motor performance, enhancing energy efficiency, and reducing operational costs. By providing detailed insights into iron loss within motors, manufacturers can make informed decisions to fine-tune motor designs and manufacturing processes.
The Role of Procurement and Purchasing
Procurement and purchasing are the backbone of any manufacturing operation. When it comes to integrating motor iron loss visualization devices, a strategic approach is essential to ensure that manufacturers acquire the right tools at the optimal price, with the desired quality and timely delivery. Effective procurement strategies involve supplier selection, negotiation, and supply chain management, all of which are crucial for the successful adoption of these advanced devices.
Supplier Selection
Choosing the right supplier is critical. Japanese suppliers are renowned for their high-quality products and reliability. Key factors to consider include the supplier’s technological expertise, track record, support services, and compatibility with existing systems. Evaluating these aspects ensures that the selected supplier can meet the specific needs of the manufacturing process and contribute to long-term success.
Negotiation Techniques
Negotiating with suppliers involves more than just discussing prices. Building long-term relationships, understanding cultural nuances, and fostering trust are essential components of successful negotiations. Techniques such as comprehensive needs assessment, leveraging volume discounts, and exploring collaborative development opportunities can help achieve favorable terms that benefit both parties.
Advantages of Motor Iron Loss Visualization Devices
Implementing motor iron loss visualization devices offers several significant benefits that can transform manufacturing operations.
Enhanced Energy Efficiency
By identifying and quantifying iron losses, manufacturers can optimize motor designs to reduce energy consumption. This leads to substantial cost savings and supports sustainability initiatives by lowering the environmental impact of motor operations.
Improved Motor Performance
Visualization devices provide detailed feedback on motor performance, enabling engineers to make data-driven adjustments. This results in motors that operate more smoothly, with higher torque and better overall performance, thereby increasing productivity and reliability.
Predictive Maintenance
With real-time monitoring of iron loss, potential issues can be detected early, allowing for proactive maintenance. This minimizes downtime, extends the lifespan of motor equipment, and reduces the costs associated with unexpected failures and repairs.
Disadvantages and Challenges
While motor iron loss visualization devices offer substantial benefits, there are inherent challenges that manufacturers must address.
Initial Investment Costs
The upfront costs of acquiring and integrating advanced visualization devices can be significant. Manufacturers must carefully evaluate the long-term savings against the initial expenditure to ensure a positive return on investment.
Technical Complexity
Implementing and maintaining visualization systems requires specialized knowledge and skills. Training personnel and ensuring system compatibility can be complex and resource-intensive, potentially leading to delays and increased operational costs if not managed effectively.
Data Management
The extensive data generated by these devices necessitates robust data management systems. Ensuring data accuracy, secure storage, and easy accessibility can be challenging, especially for organizations without existing advanced data infrastructure.
Market Conditions for Motor Iron Loss Visualization Devices
The market for motor iron loss visualization devices has been expanding, driven by the global push towards energy efficiency and sustainability. Japanese manufacturers are at the forefront of this market, offering cutting-edge solutions that set industry standards.
Competitive Landscape
The market is characterized by intense competition among established players and emerging innovators. Japanese suppliers maintain a competitive edge through continuous investments in research and development, a focus on quality and reliability, and strong customer support services.
Global Demand
As industries worldwide seek to optimize motor performance and reduce energy consumption, the demand for visualization devices continues to grow. This trend presents significant opportunities for Japanese manufacturers to expand their global footprint and capture new markets.
Best Practices in Procuring Visualization Devices
To maximize the benefits of motor iron loss visualization devices, adopting best practices in procurement is essential. These practices ensure that the acquisition process is efficient, cost-effective, and aligned with the organization’s strategic goals.
Comprehensive Needs Assessment
Before procurement, conduct a thorough analysis of organizational needs, including specific performance metrics required and integration capabilities with existing systems. This assessment helps in selecting devices that best fit the operational requirements and future growth plans.
Supplier Relationship Management
Fostering strong relationships with suppliers through regular communication, collaborative planning, and mutual support ensures a reliable supply chain. Good supplier relationships can lead to preferential terms, priority access to new technologies, and enhanced collaboration in problem-solving.
Quality Assurance
Implement stringent quality assurance protocols to ensure that the devices meet performance standards and reliability expectations. Regular audits, performance evaluations, and adherence to international quality standards help maintain high-quality outcomes.
Cost-Benefit Analysis
Conduct detailed cost-benefit analyses to evaluate the financial implications of acquiring visualization devices. This should include not only the initial purchase costs but also ongoing maintenance, training expenses, and potential savings from improved energy efficiency and reduced downtime.
Integration with Existing Systems
Successfully integrating motor iron loss visualization devices with existing manufacturing systems requires careful planning and execution. Seamless integration ensures that data flows efficiently between systems, enhancing overall operational intelligence.
Compatibility Assessment
Ensure that the new devices are compatible with current production systems and software. This reduces integration issues and facilitates seamless data flow, enabling real-time monitoring and decision-making.
Training and Support
Provide comprehensive training for staff to effectively use and maintain the visualization devices. Access to ongoing technical support from suppliers is also crucial to address any issues promptly and ensure sustained operational efficiency.
Strategic Advantages in Supplier Negotiations
Negotiating effectively with suppliers can yield strategic advantages, such as better pricing, improved terms, and enhanced collaboration. These advantages contribute to the overall efficiency and competitiveness of the manufacturing operation.
Leveraging Long-Term Partnerships
Establishing long-term partnerships with suppliers can lead to preferential treatment, such as priority access to new technologies and bulk purchasing discounts. Long-term relationships also foster mutual understanding and cooperation, facilitating smoother negotiations and collaboration.
Collaborative Innovation
Work with suppliers to foster collaborative innovation, wherein both parties contribute to the development of advanced solutions tailored to specific manufacturing needs. This approach not only enhances product offerings but also strengthens the partnership and drives mutual growth.
Transparent Communication
Maintain open and honest communication with suppliers to build trust and ensure that expectations are aligned. Transparent communication minimizes misunderstandings, fosters a cooperative environment, and enhances the overall effectiveness of the partnership.
Future Trends in Motor Iron Loss Visualization
The field of motor iron loss visualization is poised for significant advancements, driven by technological innovation and evolving industry needs. Keeping abreast of these trends ensures that manufacturers remain competitive and can leverage new technologies effectively.
Advances in Data Analytics
Enhanced data analytics capabilities will enable more sophisticated interpretations of iron loss data, facilitating better decision-making and motor optimization. Advanced algorithms and machine learning techniques can predict performance trends and identify potential issues before they escalate.
Integration with IoT
Integrating visualization devices with the Internet of Things (IoT) will allow for more comprehensive monitoring and real-time data exchange. This integration enhances overall manufacturing intelligence, enabling more responsive and adaptive production processes.
Sustainability Focus
As sustainability becomes increasingly important, visualization devices will play a key role in reducing energy consumption and minimizing the environmental impact of motor operations. Manufacturers will prioritize solutions that contribute to their sustainability goals and compliance with environmental regulations.
Best Practices for Implementing Visualization Devices
Implementing motor iron loss visualization devices requires a strategic approach to ensure maximum benefits and minimal disruptions.
Stakeholder Engagement
Engage all relevant stakeholders early in the process to gather input, align objectives, and secure buy-in. This includes engineering teams, procurement, finance, and operations personnel who will be directly impacted by the implementation.
Phased Implementation
Adopt a phased implementation approach to manage risks and allow for gradual adaptation. Starting with pilot projects can help identify potential issues and refine processes before full-scale deployment.
Continuous Monitoring and Improvement
Establish continuous monitoring and improvement mechanisms to evaluate the performance of visualization devices. Regular reviews and feedback loops help in identifying opportunities for optimization and ensuring that the devices deliver sustained value.
Case Studies: Successful Integration of Visualization Devices
Examining real-world examples can provide valuable insights into the successful integration of motor iron loss visualization devices.
Case Study 1: Enhancing Energy Efficiency in Automotive Manufacturing
A leading automotive manufacturer integrated motor iron loss visualization devices into their production line. By analyzing the data generated, they identified key areas where energy consumption could be reduced without compromising motor performance. This led to a 15% reduction in energy costs and improved overall production efficiency.
Case Study 2: Proactive Maintenance in Electronics Manufacturing
An electronics manufacturer implemented visualization devices to monitor motor performance in real-time. The early detection of potential issues allowed for proactive maintenance, reducing downtime by 20% and extending the lifespan of critical motor equipment.
Overcoming Challenges in Implementation
Implementing advanced visualization devices comes with its set of challenges, but with strategic planning, these obstacles can be effectively managed.
Managing Initial Costs
To address the high initial investment, manufacturers can explore financing options, allocate budgets strategically, and prioritize procurement based on expected return on investment. Additionally, demonstrating the long-term savings and operational benefits can justify the upfront expenditure.
Addressing Technical Complexity
Investing in training programs and hiring skilled personnel can mitigate the technical complexity associated with implementing visualization systems. Collaborating with experienced suppliers who provide comprehensive support and training can also streamline the integration process.
Ensuring Data Security
With the extensive data generated by visualization devices, ensuring data security is paramount. Implement robust cybersecurity measures, establish clear data governance policies, and regularly audit data management practices to protect sensitive information.
Conclusion
Motor iron loss visualization devices represent a significant advancement in Japanese manufacturing, offering enhanced energy efficiency, improved motor performance, and proactive maintenance capabilities. For procurement and purchasing professionals, the effective acquisition and integration of these devices require strategic supplier selection, negotiation, and adherence to best practices. Despite challenges such as initial costs and technical complexity, the long-term benefits and alignment with sustainability objectives position these devices as vital tools for modern manufacturing operations. By staying abreast of market conditions and future trends, manufacturers can leverage these innovations to maintain a competitive edge in the global market.
資料ダウンロード
QCD調達購買管理クラウド「newji」は、調達購買部門で必要なQCD管理全てを備えた、現場特化型兼クラウド型の今世紀最高の購買管理システムとなります。
ユーザー登録
調達購買業務の効率化だけでなく、システムを導入することで、コスト削減や製品・資材のステータス可視化のほか、属人化していた購買情報の共有化による内部不正防止や統制にも役立ちます。
NEWJI DX
製造業に特化したデジタルトランスフォーメーション(DX)の実現を目指す請負開発型のコンサルティングサービスです。AI、iPaaS、および先端の技術を駆使して、製造プロセスの効率化、業務効率化、チームワーク強化、コスト削減、品質向上を実現します。このサービスは、製造業の課題を深く理解し、それに対する最適なデジタルソリューションを提供することで、企業が持続的な成長とイノベーションを達成できるようサポートします。
オンライン講座
製造業、主に購買・調達部門にお勤めの方々に向けた情報を配信しております。
新任の方やベテランの方、管理職を対象とした幅広いコンテンツをご用意しております。
お問い合わせ
コストダウンが利益に直結する術だと理解していても、なかなか前に進めることができない状況。そんな時は、newjiのコストダウン自動化機能で大きく利益貢献しよう!
(Β版非公開)