- お役立ち記事
- Revolutionizing Japan’s Manufacturing: The Future of SiC MOSFET & SiC Power Module Technologies
Revolutionizing Japan’s Manufacturing: The Future of SiC MOSFET & SiC Power Module Technologies
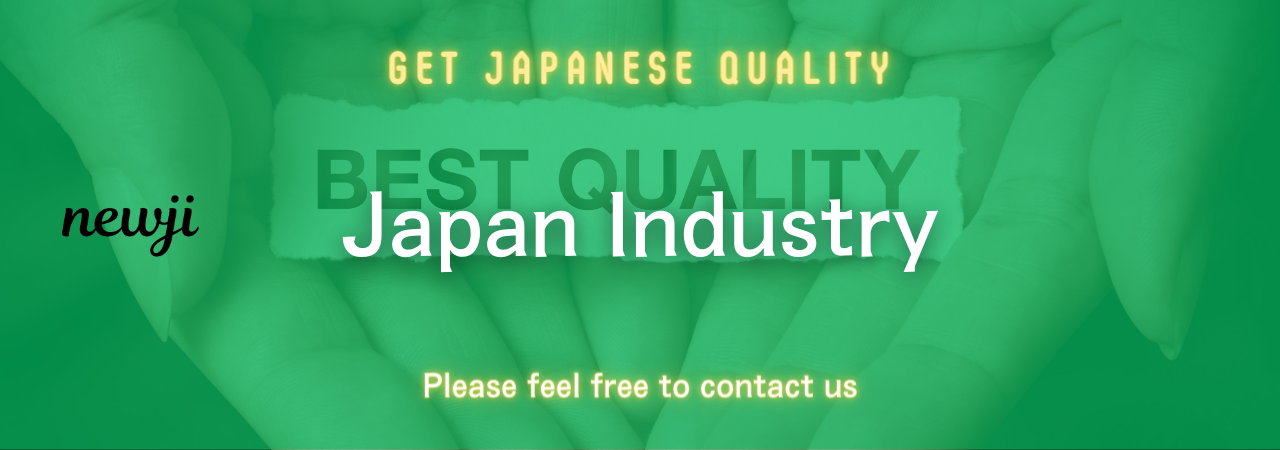
目次
Introduction
Japan has long been a global leader in manufacturing, known for its precision, innovation, and commitment to quality. As the industry evolves, the adoption of advanced semiconductor technologies like Silicon Carbide (SiC) Metal-Oxide-Semiconductor Field-Effect Transistors (MOSFETs) and SiC Power Modules is revolutionizing the landscape. These technologies promise enhanced performance, efficiency, and durability, positioning Japan at the forefront of the next industrial revolution. This article delves into the future of SiC MOSFET and SiC Power Module technologies in Japan’s manufacturing sector, exploring procurement and purchasing strategies, market conditions, supplier negotiation techniques, and best practices to harness the full potential of these advancements.
The Significance of SiC MOSFET and SiC Power Module Technologies
Silicon Carbide (SiC) is a semiconductor material that offers superior properties compared to traditional silicon-based components. SiC MOSFETs and SiC Power Modules are integral to various applications, including electric vehicles (EVs), renewable energy systems, industrial machinery, and consumer electronics. Their ability to operate at higher temperatures, voltages, and frequencies makes them indispensable for modern manufacturing processes that demand efficiency and reliability.
Enhancing Manufacturing Efficiency
In manufacturing, efficiency is paramount. SiC components enable higher switching frequencies, reducing energy losses and improving overall system performance. This translates to lower operational costs, longer equipment lifespans, and enhanced productivity. For manufacturers, integrating SiC technologies means staying competitive in a market that increasingly values sustainability and operational excellence.
Driving Innovation in Product Design
The superior thermal properties of SiC allow for more compact and lightweight designs. Manufacturers can develop products that are not only more efficient but also meet stringent size and weight constraints. This is particularly beneficial in sectors like automotive and aerospace, where space and weight are critical considerations.
Current Market Conditions in Japan
Japan’s manufacturing sector is characterized by its robust infrastructure, skilled workforce, and a strong emphasis on technological innovation. The adoption of SiC MOSFET and SiC Power Module technologies is gaining momentum, driven by both domestic demand and international market opportunities.
Demand and Supply Dynamics
The demand for SiC components is on the rise, particularly in the automotive and renewable energy sectors. Electric vehicles, in particular, are a significant driver, as they require efficient power electronics to maximize battery life and performance. On the supply side, Japan boasts several leading semiconductor manufacturers specializing in SiC technologies. However, the supply chain faces challenges such as high production costs and limited raw material availability, which can impact the scalability of these technologies.
Key Players and Innovations
Japanese companies like Infineon Technologies, Toshiba, and Fuji Electric are at the forefront of SiC technology development. These firms are investing heavily in research and development to enhance the performance and reduce the costs of SiC components. Innovations are focused on improving manufacturing processes, increasing yield rates, and developing standardized modules that can be easily integrated into various applications.
Advantages of SiC MOSFET and SiC Power Module Technologies
The adoption of SiC MOSFETs and Power Modules offers numerous advantages that are transforming manufacturing processes and product offerings.
Efficiency and Performance
SiC devices exhibit higher efficiency due to their ability to switch at faster speeds with lower energy losses. This leads to improved performance in power conversion systems, resulting in energy savings and reduced operational costs. For manufacturers, this means products that are not only more efficient but also more attractive to consumers seeking sustainable solutions.
Thermal Management
One of the standout features of SiC technology is its superior thermal conductivity. SiC devices can operate at higher temperatures, reducing the need for extensive cooling systems. This not only lowers energy consumption but also simplifies the design of electronic systems, allowing for more compact and lightweight products.
Durability and Reliability
SiC components are known for their robustness and longevity. They are less susceptible to degradation under high-stress conditions, making them ideal for applications that demand reliability and durability. This reliability translates to lower maintenance costs and longer product lifespans, enhancing overall value.
Disadvantages and Challenges
Despite their numerous benefits, SiC MOSFETs and Power Modules come with certain drawbacks that manufacturers must navigate.
High Initial Costs
The production of SiC components involves higher costs compared to traditional silicon-based counterparts. This is due to the expensive raw materials and more complex manufacturing processes required. While the long-term benefits often outweigh the initial investment, the higher upfront costs can be a barrier for some manufacturers, particularly smaller enterprises.
Supply Chain Constraints
The supply chain for SiC materials and components is still developing. Limited availability of high-quality SiC wafers and specialized manufacturing equipment can lead to supply shortages and delays. Manufacturers need to establish strong relationships with suppliers and explore alternative sourcing strategies to mitigate these risks.
Technical Complexity
Integrating SiC technologies into existing manufacturing processes can be technically challenging. It requires specialized knowledge, training, and potentially significant changes to production lines. Manufacturers must invest in employee training and collaborate closely with technology providers to ensure seamless integration and optimal performance.
Procurement and Purchasing Strategies
Effective procurement and purchasing strategies are essential for leveraging the benefits of SiC technologies while managing costs and mitigating risks.
Supplier Selection
Choosing the right suppliers is critical. Manufacturers should evaluate potential suppliers based on their technical capabilities, reliability, and ability to meet quality standards. It’s important to conduct thorough due diligence, including site visits, audits, and performance assessments, to ensure suppliers can consistently deliver high-quality SiC components.
Negotiation Techniques
Successful negotiation with suppliers involves understanding their cost structures, production capacities, and market positions. Negotiators should aim for win-win outcomes by building long-term partnerships rather than one-off transactions. Strategies include volume discounts, flexible payment terms, and collaborative development agreements that benefit both parties.
Risk Management
Supply chain risks, such as material shortages, geopolitical tensions, and technological disruptions, can impact procurement. Manufacturers should develop comprehensive risk management plans that include diversification of suppliers, maintaining safety stock, and investing in supply chain visibility tools. Building strong relationships with multiple suppliers can also enhance resilience against potential disruptions.
Best Practices in Procurement for SiC Technologies
Adopting best practices in procurement can help manufacturers optimize their purchasing processes and maximize the benefits of SiC technologies.
Building Strong Supplier Relationships
Fostering strong, collaborative relationships with suppliers can lead to better pricing, improved quality, and access to the latest technological advancements. Regular communication, joint development projects, and mutual support initiatives can strengthen partnerships and drive innovation.
Leveraging Technology in Procurement
Utilizing advanced procurement software and data analytics can streamline purchasing processes, enhance decision-making, and improve supplier management. Technologies such as blockchain can increase transparency and traceability in the supply chain, ensuring the authenticity and quality of SiC components.
Sustainable and Ethical Sourcing
Sustainability and ethical considerations are increasingly important in procurement decisions. Manufacturers should prioritize suppliers who adhere to environmental regulations, ethical labor practices, and sustainability standards. This not only aligns with corporate social responsibility goals but also mitigates risks associated with non-compliance and reputational damage.
The Future Outlook of SiC Technologies in Japan
The future of SiC MOSFETs and Power Modules in Japan looks promising, with continuous advancements and expanding applications driving growth.
Technological Advancements
Research and development efforts are focused on enhancing the performance and reducing the costs of SiC components. Innovations in wafer manufacturing, device packaging, and thermal management are expected to make SiC technologies more accessible and versatile. Emerging applications in areas like 5G infrastructure, artificial intelligence, and smart grids will further propel the adoption of SiC technologies.
Market Growth Projections
The global SiC market is projected to experience significant growth in the coming years, with Japan playing a pivotal role. Factors such as government incentives for green technologies, increasing demand for electric vehicles, and the push for energy-efficient industrial solutions are key drivers. As economies scale and production efficiencies improve, the cost of SiC components is expected to decrease, making them more competitive with traditional silicon-based technologies.
Impact on Global Manufacturing
Japan’s advancements in SiC technologies will have a ripple effect on global manufacturing. By setting high standards for quality and performance, Japanese manufacturers can influence global supply chains and set benchmarks for other regions. Collaboration with international partners and participation in global forums will further enhance Japan’s leadership position in the SiC market.
Conclusion
The integration of SiC MOSFET and SiC Power Module technologies is set to revolutionize Japan’s manufacturing sector. With their superior efficiency, thermal management, and reliability, these technologies offer substantial benefits that align with the industry’s goals of sustainability, productivity, and innovation. However, manufacturers must navigate challenges such as high initial costs, supply chain constraints, and technical complexities. By adopting effective procurement and purchasing strategies, building strong supplier relationships, and embracing best practices, Japanese manufacturers can fully leverage the potential of SiC technologies. As the market continues to evolve, Japan’s commitment to technological excellence and strategic procurement will ensure its continued leadership in the global manufacturing landscape.
資料ダウンロード
QCD調達購買管理クラウド「newji」は、調達購買部門で必要なQCD管理全てを備えた、現場特化型兼クラウド型の今世紀最高の購買管理システムとなります。
ユーザー登録
調達購買業務の効率化だけでなく、システムを導入することで、コスト削減や製品・資材のステータス可視化のほか、属人化していた購買情報の共有化による内部不正防止や統制にも役立ちます。
NEWJI DX
製造業に特化したデジタルトランスフォーメーション(DX)の実現を目指す請負開発型のコンサルティングサービスです。AI、iPaaS、および先端の技術を駆使して、製造プロセスの効率化、業務効率化、チームワーク強化、コスト削減、品質向上を実現します。このサービスは、製造業の課題を深く理解し、それに対する最適なデジタルソリューションを提供することで、企業が持続的な成長とイノベーションを達成できるようサポートします。
オンライン講座
製造業、主に購買・調達部門にお勤めの方々に向けた情報を配信しております。
新任の方やベテランの方、管理職を対象とした幅広いコンテンツをご用意しております。
お問い合わせ
コストダウンが利益に直結する術だと理解していても、なかなか前に進めることができない状況。そんな時は、newjiのコストダウン自動化機能で大きく利益貢献しよう!
(Β版非公開)