- お役立ち記事
- Revolutionizing Japanese Manufacturing: The Impact of Hot Isostatic Pressing (HIP) Processing OEM
Revolutionizing Japanese Manufacturing: The Impact of Hot Isostatic Pressing (HIP) Processing OEM
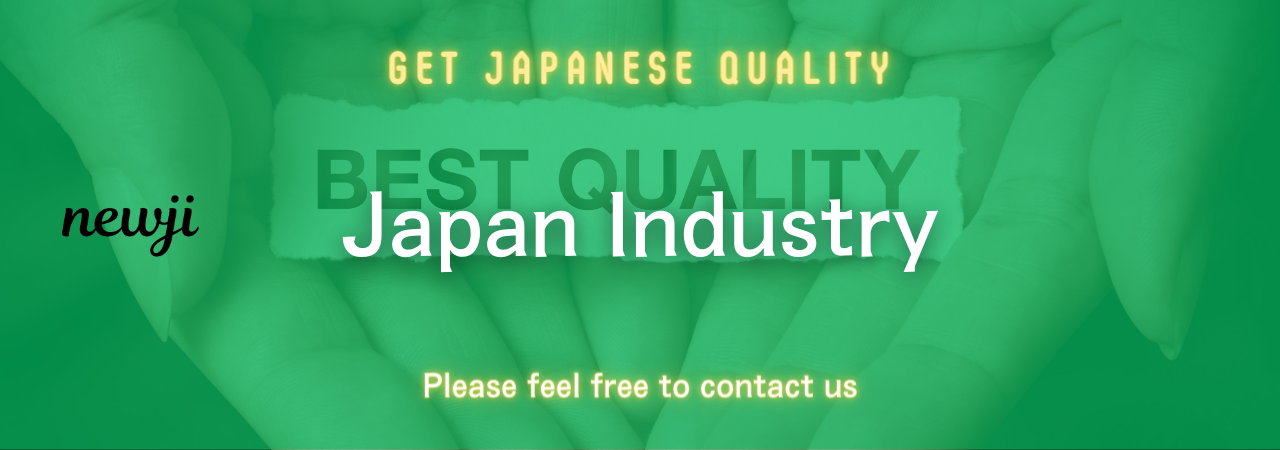
目次
Introduction to Hot Isostatic Pressing (HIP) in Japanese Manufacturing
Hot Isostatic Pressing (HIP) has emerged as a transformative technology in the realm of Japanese manufacturing.
This advanced process enhances the properties of materials, particularly metals and ceramics.
As Japanese manufacturers strive for excellence and innovation, HIP plays a critical role in maintaining their competitive edge.
The integration of HIP processing in Original Equipment Manufacturing (OEM) has revolutionized production capabilities.
This article explores the impact of HIP on Japanese manufacturing from a procurement and purchasing perspective.
We will delve into the advantages and disadvantages, supplier negotiation techniques, market conditions, and best practices associated with HIP processing OEM.
Understanding Hot Isostatic Pressing (HIP)
Hot Isostatic Pressing is a manufacturing process that applies high pressure and temperature uniformly in all directions.
This technique eliminates internal voids and enhances the mechanical properties of materials.
HIP is particularly beneficial for complex components requiring high strength and integrity.
In Japanese manufacturing, HIP is utilized across various industries, including aerospace, automotive, and electronics.
The process involves placing the material in a high-pressure chamber, where it is subjected to uniform pressure and elevated temperatures.
This environment facilitates the diffusion of atoms, resulting in a denser and more robust material structure.
Benefits of HIP in Manufacturing
HIP offers numerous benefits that align with the stringent quality standards of Japanese manufacturing.
Firstly, it significantly improves the density of materials, reducing porosity and enhancing mechanical properties.
This leads to increased durability and reliability of the final products.
Secondly, HIP allows for the production of complex geometries that are otherwise challenging to achieve with traditional manufacturing methods.
This flexibility enables Japanese manufacturers to innovate and design intricate components tailored to specific applications.
Additionally, HIP contributes to the reduction of material waste, promoting cost efficiency and sustainability in the manufacturing process.
Applications of HIP in Various Industries
In the aerospace industry, HIP is crucial for producing high-strength components that can withstand extreme conditions.
Automotive manufacturers utilize HIP to create lightweight yet durable parts, contributing to fuel efficiency and performance.
The electronics sector benefits from HIP through the production of reliable and precise components essential for advanced technologies.
Furthermore, the medical industry employs HIP for manufacturing biocompatible implants and devices, ensuring safety and effectiveness.
Advantages of HIP Processing OEM
Opting for HIP processing within OEM frameworks offers several strategic advantages for Japanese manufacturers.
Enhanced Material Properties
HIP significantly improves the mechanical and physical properties of materials.
This enhancement ensures that components meet the highest standards of strength, durability, and performance.
Such quality is paramount in industries where failure can lead to catastrophic consequences, such as aerospace and medical devices.
Cost Efficiency and Waste Reduction
By minimizing material waste and optimizing production processes, HIP contributes to cost savings.
Japanese manufacturers can achieve higher yields and lower production costs, enhancing overall profitability.
Moreover, the ability to produce complex parts in a single step reduces the need for multiple manufacturing stages, further driving efficiency.
Improved Product Reliability
HIP ensures that products have uniform density and integrity, reducing the likelihood of defects and failures.
This reliability is crucial for maintaining the reputation of Japanese products known for their quality and precision.
Customers can trust that components manufactured through HIP will perform consistently under demanding conditions.
Innovation and Competitive Advantage
Integrating HIP into OEM processes fosters innovation by enabling the creation of advanced and specialized components.
Japanese manufacturers can stay ahead of global competitors by offering superior products that leverage cutting-edge technology.
This competitive advantage is essential in maintaining Japan’s leadership in various high-tech industries.
Challenges and Disadvantages of HIP Processing OEM
While HIP offers numerous benefits, there are also challenges that Japanese manufacturers may encounter.
High Initial Investment
Implementing HIP technology requires significant capital investment in equipment and facilities.
The high cost can be a barrier for smaller manufacturers or those looking to expand their production capabilities.
However, the long-term benefits often justify the initial expenditure, especially for large-scale operations.
Technical Expertise and Training
Operating HIP equipment and optimizing the process demands a high level of technical expertise.
Japanese manufacturers must invest in training their workforce to ensure proficiency in HIP techniques.
The lack of skilled personnel can hinder the effective implementation of HIP, affecting productivity and quality.
Extended Processing Times
HIP processes can be time-consuming, particularly for complex or large components.
The extended processing times may lead to longer lead times and affect the overall production schedule.
Efficient planning and scheduling are essential to mitigate delays and maintain production efficiency.
Material Limitations
Not all materials are suitable for HIP processing.
Japanese manufacturers must carefully select materials that can benefit from HIP to avoid unnecessary costs and processing inefficiencies.
Understanding material properties and compatibility with HIP is crucial for successful implementation.
Supplier Negotiation Techniques for HIP Processing OEM
Effective supplier negotiation is vital for Japanese manufacturers seeking to optimize HIP processing in their OEM operations.
Conducting Comprehensive Market Research
Before entering negotiations, it is essential to conduct thorough market research to understand the landscape of HIP suppliers.
Japanese manufacturers should evaluate potential suppliers based on their technological capabilities, reputation, and pricing structures.
This information provides a foundation for informed negotiation strategies.
Building Strong Relationships
Establishing strong, long-term relationships with HIP suppliers can lead to better terms and collaboration.
Japanese business culture emphasizes trust and mutual respect, which can be leveraged to negotiate favorable agreements.
Regular communication and partnership-building activities foster a collaborative environment conducive to successful negotiations.
Leveraging Bulk Purchasing
Manufacturers can negotiate better pricing by committing to bulk purchases of HIP services or equipment.
Suppliers are often willing to offer discounts or favorable terms in exchange for large orders or long-term contracts.
This strategy not only reduces costs but also ensures a steady supply of necessary services.
Emphasizing Quality and Reliability
Japanese manufacturers should prioritize quality and reliability in their negotiations.
By emphasizing the importance of high standards and consistent performance, manufacturers can secure agreements that align with their quality requirements.
This focus ensures that suppliers remain committed to delivering superior products and services.
Flexibility and Adaptability
Negotiations should also address the need for flexibility and adaptability in supplier agreements.
Manufacturers may require suppliers to adjust to changing demands or specific project requirements.
Incorporating flexibility into contracts allows for smoother adjustments and maintains production continuity.
Market Conditions Affecting HIP Processing OEM
Understanding the market conditions is essential for Japanese manufacturers involved in HIP processing OEM.
Global Demand and Competition
The global demand for high-performance materials and advanced manufacturing processes is increasing.
Japanese manufacturers must navigate a competitive landscape where other countries are also investing in similar technologies.
Staying updated on global trends and innovations is crucial for maintaining competitiveness.
Technological Advancements
Rapid advancements in HIP technology continuously reshape the market.
Japanese manufacturers need to stay abreast of these developments to integrate the latest improvements into their processes.
Adopting cutting-edge technology can enhance efficiency, product quality, and overall competitiveness.
Economic Factors
Economic conditions, such as fluctuations in currency exchange rates and raw material prices, impact HIP processing OEM.
Japanese manufacturers must develop strategies to mitigate economic risks, such as diversifying suppliers or hedging against currency volatility.
Economic resilience ensures sustained operations amidst market uncertainties.
Regulatory Environment
Compliance with international and local regulations is imperative in HIP processing.
Japanese manufacturers must adhere to environmental standards, safety regulations, and industry-specific guidelines.
Staying compliant not only avoids legal issues but also enhances the company’s reputation for responsible manufacturing practices.
Best Practices for Implementing HIP Processing OEM
Adopting best practices ensures the successful integration of HIP processing into OEM operations.
Comprehensive Planning and Strategy
A well-defined plan and strategy are foundational for effective HIP implementation.
Japanese manufacturers should outline their objectives, allocate resources appropriately, and set clear timelines.
Strategic planning facilitates smooth transitions and minimizes disruptions to existing operations.
Investing in Training and Development
Continuous training and development are essential for maintaining expertise in HIP technology.
Japanese manufacturers should invest in training programs that equip their workforce with the necessary skills and knowledge.
A well-trained team ensures optimal utilization of HIP processes and contributes to overall production excellence.
Quality Assurance and Control
Implementing robust quality assurance and control measures is critical in HIP processing.
Japanese manufacturers should establish stringent quality protocols to monitor every stage of the HIP process.
Consistent quality checks guarantee that the final products meet the highest standards and customer expectations.
Collaborative Supplier Partnerships
Fostering collaborative partnerships with HIP suppliers enhances process integration and innovation.
Japanese manufacturers and suppliers should work closely to share insights, address challenges, and explore new opportunities.
Collaborative efforts lead to mutual growth and the development of superior manufacturing solutions.
Continuous Improvement and Innovation
Embracing a culture of continuous improvement drives ongoing advancements in HIP processing.
Japanese manufacturers should regularly evaluate their processes, seek feedback, and implement improvements.
Innovation ensures that manufacturers remain at the forefront of technology and maintain their competitive advantage.
Case Studies: Successful HIP Processing OEM in Japan
Examining successful case studies provides valuable insights into effective HIP processing OEM implementation.
Aerospace Industry Success
A leading Japanese aerospace manufacturer integrated HIP processing to produce high-strength turbine components.
By adopting HIP, the company achieved superior material properties, resulting in enhanced performance and reliability.
This integration not only improved product quality but also reduced manufacturing costs and lead times.
Automotive Sector Advancement
A prominent automotive manufacturer employed HIP to develop lightweight yet durable engine parts.
The HIP-processed components contributed to improved fuel efficiency and performance.
This technological advancement positioned the manufacturer as a leader in innovative and sustainable automotive solutions.
Electronics Manufacturing Excellence
A Japanese electronics company utilized HIP processing to manufacture precise and reliable semiconductor components.
The superior integrity of HIP-processed materials ensured consistent performance in high-demand applications.
This success reinforced the company’s reputation for producing high-quality and cutting-edge electronic products.
Future Trends and the Evolving Role of HIP in Japanese Manufacturing
The future of HIP in Japanese manufacturing is poised for significant growth and innovation.
Integration with Additive Manufacturing
Combining HIP with additive manufacturing techniques can unlock new possibilities in material science and component design.
Japanese manufacturers are exploring this integration to enhance precision, reduce waste, and create complex structures with unprecedented accuracy.
Automation and Industry 4.0
The advent of Industry 4.0 technologies presents opportunities to automate HIP processes.
Japanese manufacturers are adopting smart manufacturing solutions to optimize HIP operations, improve data analytics, and increase overall efficiency.
Sustainability and Green Manufacturing
Sustainability is increasingly important in manufacturing practices.
HIP processing aligns with green manufacturing principles by reducing material waste and enabling the use of sustainable materials.
Japanese manufacturers are leveraging HIP to meet environmental goals and respond to the growing demand for eco-friendly products.
Advanced Material Development
The development of new materials that can benefit from HIP processing is a key area of focus.
Japanese research institutions and manufacturers are collaborating to create materials with enhanced properties, further expanding the applications of HIP in various industries.
Conclusion
Hot Isostatic Pressing (HIP) processing OEM has significantly impacted Japanese manufacturing, driving advancements in quality, efficiency, and innovation.
Despite challenges such as high initial investment and the need for technical expertise, the benefits of HIP—enhanced material properties, cost efficiency, improved reliability, and competitive advantage—are substantial.
By employing effective supplier negotiation techniques, understanding market conditions, and adopting best practices, Japanese manufacturers can successfully integrate HIP into their OEM processes.
As technology and market demands evolve, HIP will continue to play a pivotal role in maintaining Japan’s leadership in high-tech and precision manufacturing industries. Embracing HIP processing ensures that Japanese manufacturers remain at the forefront of innovation, delivering superior products that meet the highest standards of quality and performance.
資料ダウンロード
QCD調達購買管理クラウド「newji」は、調達購買部門で必要なQCD管理全てを備えた、現場特化型兼クラウド型の今世紀最高の購買管理システムとなります。
ユーザー登録
調達購買業務の効率化だけでなく、システムを導入することで、コスト削減や製品・資材のステータス可視化のほか、属人化していた購買情報の共有化による内部不正防止や統制にも役立ちます。
NEWJI DX
製造業に特化したデジタルトランスフォーメーション(DX)の実現を目指す請負開発型のコンサルティングサービスです。AI、iPaaS、および先端の技術を駆使して、製造プロセスの効率化、業務効率化、チームワーク強化、コスト削減、品質向上を実現します。このサービスは、製造業の課題を深く理解し、それに対する最適なデジタルソリューションを提供することで、企業が持続的な成長とイノベーションを達成できるようサポートします。
オンライン講座
製造業、主に購買・調達部門にお勤めの方々に向けた情報を配信しております。
新任の方やベテランの方、管理職を対象とした幅広いコンテンツをご用意しております。
お問い合わせ
コストダウンが利益に直結する術だと理解していても、なかなか前に進めることができない状況。そんな時は、newjiのコストダウン自動化機能で大きく利益貢献しよう!
(Β版非公開)