- お役立ち記事
- Example of restructuring the purchasing department’s procurement process to reduce the risk of material supply delays
Example of restructuring the purchasing department’s procurement process to reduce the risk of material supply delays
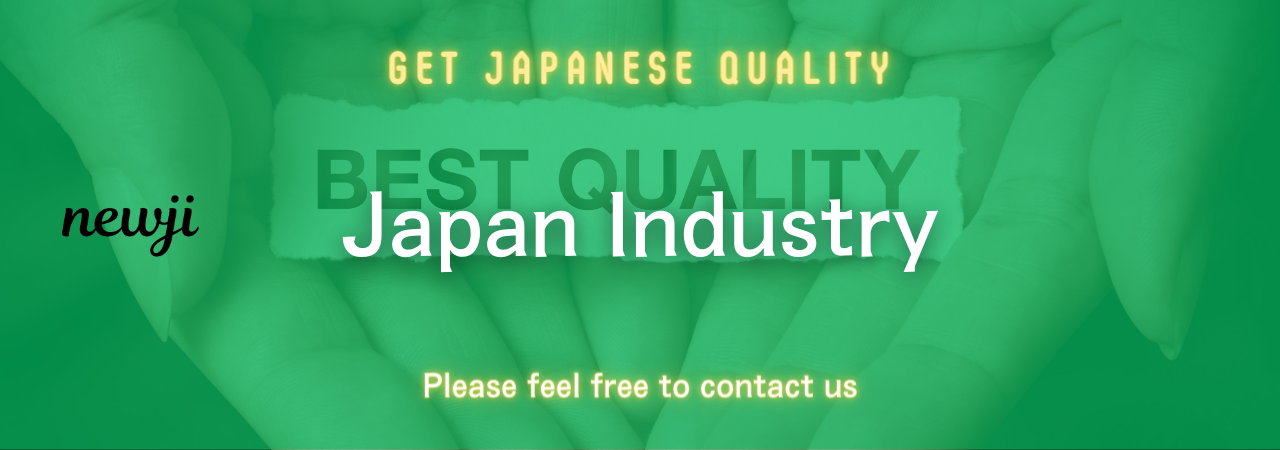
目次
Understanding the Procurement Process
Procurement is a crucial component of any organization’s operations, especially in manufacturing and production sectors.
It involves acquiring goods and services from external sources, ensuring that the right quality and quantity are delivered at the right time and price.
The procurement process is typically handled by the purchasing department, whose main goal is to maintain a steady supply of materials to meet production demands.
However, supply chain disruptions can lead to material shortages, impacting overall productivity.
Therefore, restructuring the procurement process can help mitigate risks of supply delays.
Identifying Challenges in the Procurement Process
Before restructuring the procurement process, it’s vital to identify the existing challenges that can lead to delays.
Common issues include supplier reliability, demand forecasting inaccuracies, and logistical setbacks.
Supplier reliability is a primary concern, as it impacts an organization’s ability to receive materials on time.
Likewise, incorrect demand forecasts can lead to either surplus inventory or shortages, both of which can affect cash flow and production timelines.
Additionally, logistical challenges such as transportation delays and customs clearance also play a significant role in delaying supplies.
Steps to Restructure the Procurement Process
Restructuring the procurement process involves a strategic approach to enhance efficiency and reduce risks.
Here are some practical steps to achieve this:
1. Enhancing Supplier Relationships
Building strong relationships with suppliers is critical for ensuring a reliable supply chain.
Establish open communication channels and develop partnerships with key suppliers to foster trust and reliability.
Regular performance evaluations and feedback can help assess and improve supplier reliability.
Additionally, consider diversifying your supplier base to mitigate the risk of dependency on a single supplier.
2. Implementing Accurate Demand Forecasting
Accurate demand forecasting is essential for balancing supply with production needs.
Leverage data analytics and historical sales data to improve demand predictions.
Implement advanced forecasting tools that can provide real-time insights and adapt to market trends.
Collaborate with the sales and marketing departments to gather valuable input for more precise forecasting.
3. Optimizing Inventory Management
Effective inventory management can prevent both overstock and stockouts.
Adopt an inventory management system that tracks real-time stock levels and alerts the purchasing team about reorder points.
Consider adopting just-in-time (JIT) inventory practices to reduce carrying costs and improve cash flow.
Regular inventory audits will help identify any discrepancies and maintain accurate data.
4. Streamlining Logistics and Transportation
Streamlined logistics and transportation processes are essential for minimizing supply delays.
Work closely with logistics partners to coordinate shipments and track deliveries in real time.
Implement a transportation management system (TMS) to optimize routes, reduce transit times, and minimize costs.
Prepare contingency plans for potential disruptions, like delays at customs or natural disasters.
5. Utilizing Technology Solutions
Technology plays a pivotal role in enhancing the procurement process.
Utilize procurement software that integrates with existing systems to automate routine tasks like purchase orders, invoicing, and supplier management.
Implement e-procurement systems to streamline sourcing and supplier negotiations.
Electronic data interchange (EDI) can facilitate efficient communication with suppliers, reducing lead times and manual data entry errors.
Benefits of a Reimagined Procurement Process
Restructuring the procurement process can yield significant benefits for an organization:
Reduced Risk of Delays
By addressing the challenges in procurement, organizations can significantly reduce the risk of material supply delays.
Improved supplier relationships, accurate demand forecasting, and optimized logistics all contribute to a more reliable supply chain.
Cost Savings
An efficient procurement process helps reduce unnecessary expenses related to expedited shipping, overstock, and low supplier reliability.
Better inventory management leads to lower holding costs and minimizes the risk of obsolescence.
Enhanced Operational Efficiency
A seamless procurement process ensures that materials are available when needed, supporting uninterrupted production schedules.
This results in improved operational efficiency and higher productivity levels.
Improved Supplier Performance
Enhanced supplier relationships lead to better performance, as suppliers are motivated to maintain a high standard of service.
This, in turn, results in faster response times and potentially favorable terms and pricing.
Conclusion
Redesigning the procurement process is vital for reducing the risk of material supply delays.
With a focus on supplier relationships, accurate forecasting, efficient inventory management, streamlined logistics, and technology integration, businesses can achieve a resilient supply chain.
The benefits are substantial, improving not only cost savings but also operational efficiency and supplier performance.
By actively restructuring procurement practices, organizations can secure a more reliable and efficient supply chain, ultimately supporting their long-term success.
資料ダウンロード
QCD調達購買管理クラウド「newji」は、調達購買部門で必要なQCD管理全てを備えた、現場特化型兼クラウド型の今世紀最高の購買管理システムとなります。
ユーザー登録
調達購買業務の効率化だけでなく、システムを導入することで、コスト削減や製品・資材のステータス可視化のほか、属人化していた購買情報の共有化による内部不正防止や統制にも役立ちます。
NEWJI DX
製造業に特化したデジタルトランスフォーメーション(DX)の実現を目指す請負開発型のコンサルティングサービスです。AI、iPaaS、および先端の技術を駆使して、製造プロセスの効率化、業務効率化、チームワーク強化、コスト削減、品質向上を実現します。このサービスは、製造業の課題を深く理解し、それに対する最適なデジタルソリューションを提供することで、企業が持続的な成長とイノベーションを達成できるようサポートします。
オンライン講座
製造業、主に購買・調達部門にお勤めの方々に向けた情報を配信しております。
新任の方やベテランの方、管理職を対象とした幅広いコンテンツをご用意しております。
お問い合わせ
コストダウンが利益に直結する術だと理解していても、なかなか前に進めることができない状況。そんな時は、newjiのコストダウン自動化機能で大きく利益貢献しよう!
(Β版非公開)