- お役立ち記事
- Methods and points for establishing a quality assurance system that is important to the purchasing department
Methods and points for establishing a quality assurance system that is important to the purchasing department
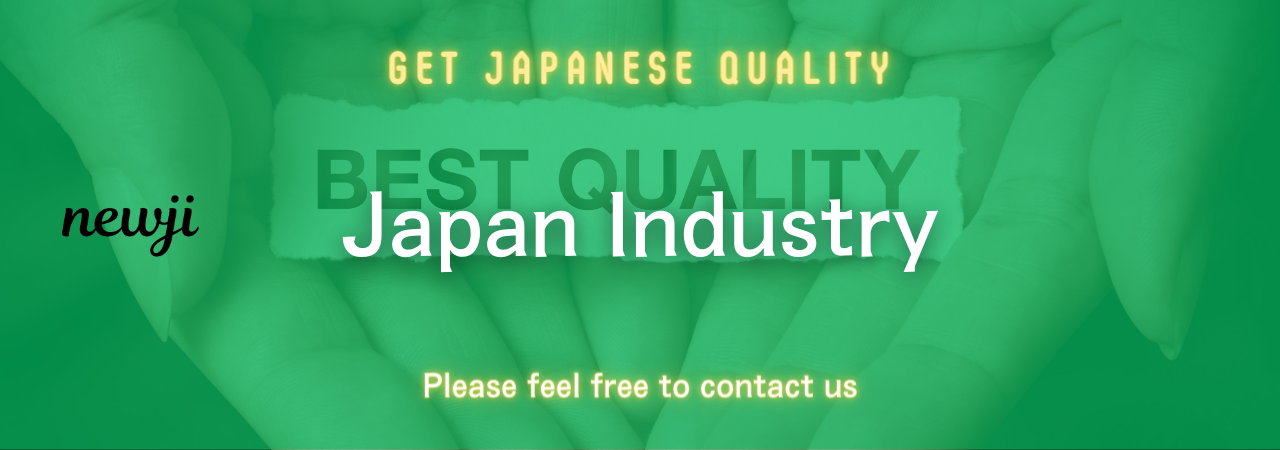
目次
Understanding Quality Assurance Systems
A quality assurance system is vital for any organization, especially within the purchasing department.
This system ensures that products or services consistently meet the necessary quality standards.
By implementing a quality assurance system, companies can minimize defects, improve customer satisfaction, and maintain a competitive edge.
Understanding the fundamental purpose of a quality assurance system is the first step in establishing an effective process.
Key Components of a Quality Assurance System
A comprehensive quality assurance system often includes several critical components.
These elements work together to ensure that products or services are delivered consistently and reliably.
– **Policies and Procedures:** Clear policies and standardized procedures form the backbone of any quality assurance system.
These guidelines establish the standards that all employees and processes must adhere to.
– **Documentation:** Accurate documentation is essential for tracking and verifying quality assurance activities.
It ensures transparency and accountability throughout the organization.
– **Training and Development:** Providing training for employees guarantees they understand quality standards and procedures.
It empowers them to execute their tasks effectively while maintaining a high-quality output.
– **Continuous Improvement:** Regularly measuring performance and seeking improvement opportunities is crucial.
By evaluating data and feedback, organizations can fine-tune their processes for better efficiency.
The Role of the Purchasing Department in Quality Assurance
The purchasing department plays a pivotal role in quality assurance.
Its responsibilities include selecting and evaluating suppliers, assessing product quality, and negotiating contracts.
Here, we’ll delve into how this department contributes to maintaining high-quality standards.
Supplier Selection and Evaluation
Choosing the right suppliers significantly affects the quality of products or services.
The purchasing department must assess potential suppliers based on several criteria:
– **Quality Standards Compliance:** Ensure suppliers comply with recognized quality standards and certifications.
These might include ISO certifications or industry-specific quality norms.
– **Reputation and Track Record:** Evaluating a supplier’s history of quality assurance can provide insight into their reliability.
Past performance data and customer reviews can offer valuable information for decision-making.
Setting Quality Benchmarks
Once suppliers are chosen, the purchasing department must set clear quality benchmarks.
These standards delineate the acceptable quality levels for products or services.
They serve as performance metrics that suppliers must meet or exceed.
– **Detailed Specifications:** Establish comprehensive product specifications to prevent any ambiguity regarding quality expectations.
Including measurable units for each requirement ensures preciseness in evaluation.
– **Regular Quality Audits:** Conducting regular audits can help verify that suppliers remain consistent with quality expectations.
These reviews should include both scheduled and surprise audits to ensure comprehensive evaluations.
Negotiating Contracts
Effective contract negotiations help safeguard quality standards.
The purchasing department must draft contracts that clearly define quality metrics and include clauses for quality-related contingencies.
– **Penalty and Incentive Clauses:** Include provisions that incentivize suppliers for superior performance and impose penalties for poor quality.
Such clauses ensure accountability and motivate suppliers to maintain high-quality standards.
Implementing a Successful Quality Assurance System
Developing a successful quality assurance system requires a strategic approach.
The following methods and points are essential for actual implementation in the purchasing department.
Establish Clear objectives
Start by defining the specific goals of your quality assurance system.
These objectives should be realistic, measurable, and aligned with the overall organizational strategy.
Well-defined goals will guide the structuring of the quality assurance system and facilitate progress tracking.
Create a Culture of Quality
Cultivating a quality-centric culture within the organization encourages employees to prioritize quality in their daily activities.
Emphasize the value of quality assurance during orientation, training sessions, and regular meetings.
Employees should understand the impact of quality on customer satisfaction and business success.
Leverage Technology and Tools
Incorporating technology can significantly enhance the efficiency of a quality assurance system.
Software solutions can automate documentation, streamline communication, and facilitate data analysis.
– **Quality Management Systems (QMS):** Implementing a QMS can help streamline processes and ensure compliance with quality standards.
– **Data Analytics Tools:** Utilize data analytics tools to identify trends, track performance, and uncover areas for improvement.
These insights can inform decision-making and strategy adjustments.
Regular Reviews and Feedback
Continuous monitoring and feedback loops are vital for sustaining quality assurance systems.
Regular reviews help identify inefficiencies and prompt timely corrective actions.
– **Employee Feedback:** Encourage open communication and employee feedback about the quality systems in place.
Their insights can lead to practical improvements.
– **Customer Feedback:** Garner customer feedback too, as it highlights perceptions of quality from an end-user perspective.
Understanding customer experiences can drive improvements that enhance satisfaction and loyalty.
Adapting to Changes and Challenges
The business environment is ever-evolving, meaning quality assurance systems must adapt to changes and challenges.
A flexible system will accommodate alterations in consumer demands, technological advances, and regulatory shifts.
– **Stay Informed:** Keep abreast of industry trends, technological developments, and regulatory changes that affect quality standards.
Updating systems in response to such trends ensures continued relevance.
– **Agile Processes:** Create flexible processes that can pivot quickly in response to external and internal changes.
Agility in process adaptation can prevent disruptions and maintain consistent quality standards.
By thoroughly understanding and implementing these methods and points, a purchasing department can establish a robust quality assurance system.
This system will not only enhance product and service quality but will also strengthen the organization’s position in the competitive market.
資料ダウンロード
QCD調達購買管理クラウド「newji」は、調達購買部門で必要なQCD管理全てを備えた、現場特化型兼クラウド型の今世紀最高の購買管理システムとなります。
ユーザー登録
調達購買業務の効率化だけでなく、システムを導入することで、コスト削減や製品・資材のステータス可視化のほか、属人化していた購買情報の共有化による内部不正防止や統制にも役立ちます。
NEWJI DX
製造業に特化したデジタルトランスフォーメーション(DX)の実現を目指す請負開発型のコンサルティングサービスです。AI、iPaaS、および先端の技術を駆使して、製造プロセスの効率化、業務効率化、チームワーク強化、コスト削減、品質向上を実現します。このサービスは、製造業の課題を深く理解し、それに対する最適なデジタルソリューションを提供することで、企業が持続的な成長とイノベーションを達成できるようサポートします。
オンライン講座
製造業、主に購買・調達部門にお勤めの方々に向けた情報を配信しております。
新任の方やベテランの方、管理職を対象とした幅広いコンテンツをご用意しております。
お問い合わせ
コストダウンが利益に直結する術だと理解していても、なかなか前に進めることができない状況。そんな時は、newjiのコストダウン自動化機能で大きく利益貢献しよう!
(Β版非公開)