- お役立ち記事
- Purchasing department budget allocation strategy holds the key to manufacturing cost control
Purchasing department budget allocation strategy holds the key to manufacturing cost control
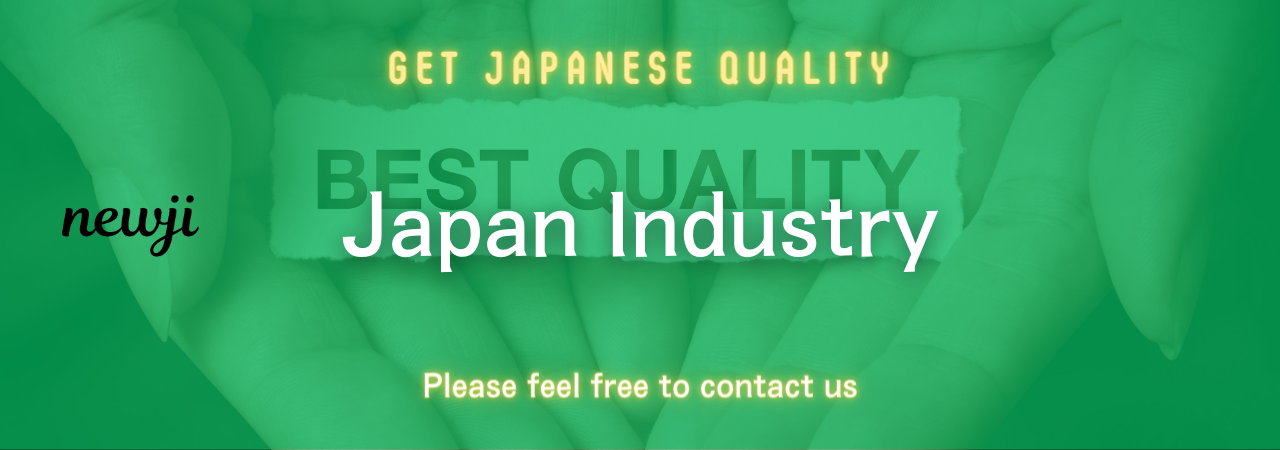
目次
Understanding the Role of the Purchasing Department in Cost Control
In the world of manufacturing, cost control is a critical aspect that can make or break a company’s success.
One of the pivotal departments that play a significant role in managing these costs is the purchasing department.
The efficiency and effectiveness of how a purchasing department allocates its budget can directly influence the overall manufacturing expenses.
The strategy adopted by this department is, therefore, essential for ensuring cost-effective operations and maintaining a competitive edge in the market.
The Importance of Budget Allocation
Budget allocation within the purchasing department involves assigning financial resources to various purchasing needs.
Proper allocation is essential to ensure that the company receives the best value for money while maintaining quality standards.
This careful distribution of resources also helps in identifying areas where savings can be made without compromising on the quality of materials used in manufacturing.
An effective budget allocation strategy allows a company to forecast future needs accurately, manage supplier relationships efficiently, and ensure a consistent supply of materials.
It also plays a crucial role in maintaining a balance between cost, quality, and the timely delivery of goods and services.
Developing a Successful Budget Allocation Strategy
Creating a successful budget allocation strategy requires a thorough understanding of the company’s manufacturing needs and the market conditions.
Here are a few key steps that can help in developing this strategy:
1. Analyze Current Spending
The first step in formulating a budget allocation strategy is to analyze the current spending patterns.
This involves reviewing past expenditures to identify trends and areas where costs can be reduced.
Understanding current spending helps in setting realistic budget limits and prioritizing essential purchases.
2. Set Clear Objectives
Establishing clear objectives is crucial for effective budget allocation.
These objectives should align with the company’s overall goals and include specific, measurable targets.
Clear objectives provide a roadmap for the purchasing department, guiding them in making informed decisions regarding resource allocation.
3. Involve Key Stakeholders
Involving key stakeholders in the budget planning process ensures that different perspectives are considered, leading to a more comprehensive strategy.
This collaboration helps in understanding the needs of various departments, which can be crucial in prioritizing purchasing activities and making budgeting adjustments.
4. Implement Cost-Saving Measures
Implementing cost-saving measures is an essential component of a budget allocation strategy.
This may involve negotiating better terms with suppliers, bulk purchasing, or finding alternative materials that offer the same quality at a lower cost.
These measures help in optimizing the budget and reducing overall manufacturing expenses.
5. Monitor and Adjust the Strategy
Continuous monitoring and adjustment of the budget allocation strategy are necessary to address any changes in market conditions or company needs.
Regularly reviewing the strategy helps in identifying any discrepancies or inefficiencies, allowing for timely adjustments to ensure ongoing cost control.
Leveraging Technology for Efficient Budget Allocation
The integration of technology in the purchasing process can significantly enhance the efficiency of budget allocation.
Utilizing tools such as automated procurement software or data analytics can provide valuable insights into spending patterns and help streamline purchasing activities.
Automated Procurement Systems
Automated procurement systems can help the purchasing department manage their budget more effectively by providing real-time data on spending and inventory levels.
These systems can also automate routine tasks such as purchase order creation and supplier management, freeing up time for strategic planning.
Data Analytics
Data analytics can be a powerful tool for improving budget allocation strategies.
By analyzing historical purchasing data, companies can identify patterns and trends that inform future budgeting decisions.
This data-driven approach ensures that resources are allocated more efficiently, ultimately leading to reduced manufacturing costs.
The Benefits of an Effective Budget Allocation Strategy
An effective budget allocation strategy offers numerous benefits for the manufacturing sector.
By optimizing resource allocation, companies can achieve significant cost savings and improve their profitability.
Moreover, a well-crafted strategy ensures that the purchasing department is better equipped to handle market fluctuations and adapt to changing business needs.
Enhanced Supplier Relationships
A strategic approach to budget allocation can also lead to improved relationships with suppliers.
By understanding the company’s purchasing patterns and priorities, suppliers can offer better terms and more competitive pricing, resulting in a mutually beneficial partnership.
Improved Quality Control
By carefully allocating the budget, the purchasing department can ensure that only high-quality materials are procured, leading to improved product quality and customer satisfaction.
This focus on quality control also minimizes the risk of defects or returns, which can be costly for manufacturing companies.
Increased Operational Efficiency
Finally, an optimized budget allocation strategy enables the purchasing department to operate more efficiently.
With clear guidelines and objectives in place, the department can make quicker, more informed decisions, reducing the time spent on procurement activities and allowing manufacturing operations to proceed smoothly.
In conclusion, the purchasing department’s budget allocation strategy plays a crucial role in controlling manufacturing costs.
By implementing a well-thought-out strategy that incorporates analysis, stakeholder involvement, and technology, companies can achieve cost savings, improve quality control, and enhance overall operational efficiency.
資料ダウンロード
QCD調達購買管理クラウド「newji」は、調達購買部門で必要なQCD管理全てを備えた、現場特化型兼クラウド型の今世紀最高の購買管理システムとなります。
ユーザー登録
調達購買業務の効率化だけでなく、システムを導入することで、コスト削減や製品・資材のステータス可視化のほか、属人化していた購買情報の共有化による内部不正防止や統制にも役立ちます。
NEWJI DX
製造業に特化したデジタルトランスフォーメーション(DX)の実現を目指す請負開発型のコンサルティングサービスです。AI、iPaaS、および先端の技術を駆使して、製造プロセスの効率化、業務効率化、チームワーク強化、コスト削減、品質向上を実現します。このサービスは、製造業の課題を深く理解し、それに対する最適なデジタルソリューションを提供することで、企業が持続的な成長とイノベーションを達成できるようサポートします。
オンライン講座
製造業、主に購買・調達部門にお勤めの方々に向けた情報を配信しております。
新任の方やベテランの方、管理職を対象とした幅広いコンテンツをご用意しております。
お問い合わせ
コストダウンが利益に直結する術だと理解していても、なかなか前に進めることができない状況。そんな時は、newjiのコストダウン自動化機能で大きく利益貢献しよう!
(Β版非公開)